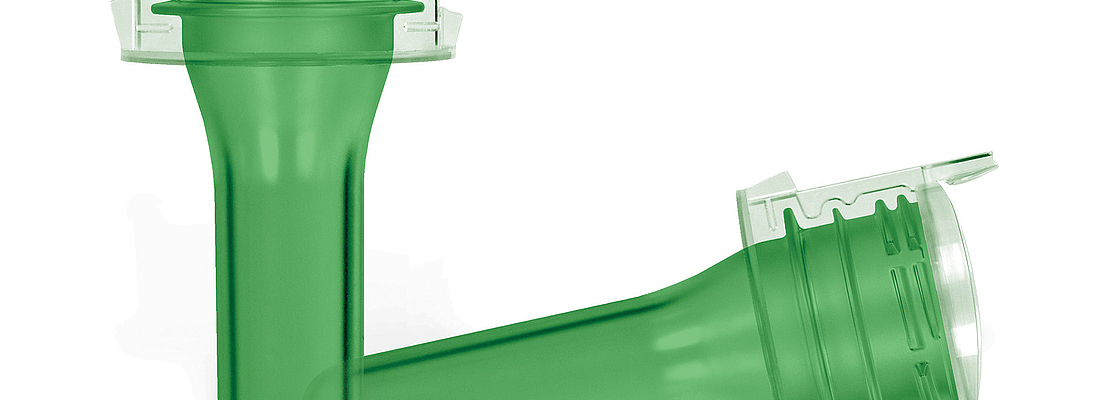
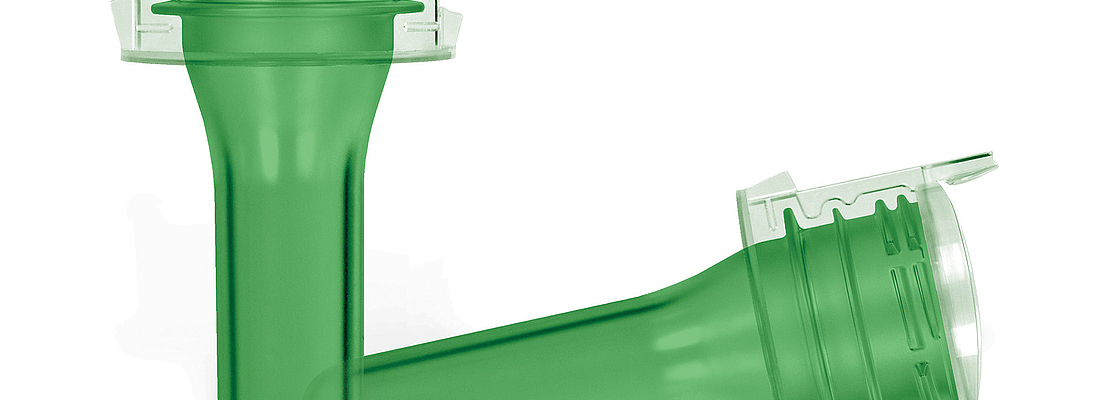
Molds have to be cleaned. There’s no way to avoid it. Molds need vents large enough for air to escape the cavity but small enough so the plastic won’t, so they are small and prone to clogging. Clogged vents result in trapped air, and trapped air results in part defects.
But what if the mold could clean itself?
Throughout the years, there have been two commonly practiced methods of mold cleaning – hand cleaning and dry ice blasting.
While extremely effective, hand cleaning is a complex process that requires the mold components to be individually removed, cleaned, rinsed, dried and replaced with the use of spray cleaners, solvents and brushes. This method is labor intensive and time consuming, and naturally it has a negative effect on productivity.
The other traditional cleaning method is dry ice blasting. This non-abrasive method allows a mold to be cleaned directly in the press, while the mold is still hot, and does not cause a secondary waste stream. Grain-sized carbon dioxide pellets are introduced into the air stream and are shot out through nozzles at high speed to quickly remove residue. This method is popular because of its effectiveness and versatility. However, dry ice is expensive and requires special handling, due to its high sublimation rate – approximately 10% of its volume can be lost per day.
The problem with each of these methods is the amount of labor and downtime required. Manual cleaning requires skilled maintenance personnel, who are generally in high demand at any plant. Manual cleaning must be thorough to avoid processing defects, therefore can be time-consuming. Every time manual cleaning is performed, it is possible to damage the tool during the cleaning process, or even upon entering or exiting the machine between the mold halves.
Compounding the impact of manual maintenance on productivity is the increasing speed of systems. As cycle times decrease, molds naturally require maintenance more often. As a result, the benefit of increased productivity must be weighed against a significant rise in cycle-based maintenance activities.
To combat these issues, leading equipment suppliers are investing in developing innovative solutions to help make the mold cleaning process faster, easier and safer. An example is Husky Injection Molding System’s new self-cleaning mold technology.
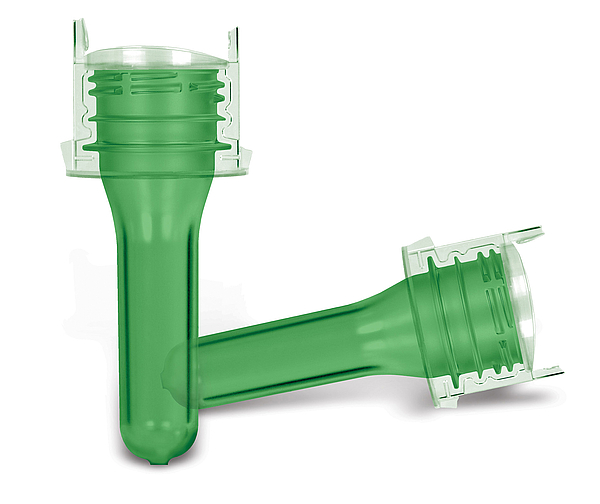
At the recent NPE 2015 tradeshow, Husky introduced its self-cleaning mold technology, which was demonstrated on a HyPET HPP5 system running a 5.5 second cycle time. On this system was the Reduced Maintenance Package, which combines self-cleaning with greaseless wear components, which saved up to 400 hours of downtime per year, boosting productivity by five percent.
Husky’s Reduced Maintenance Package allows their customers to skip some of the traditional maintenance interruptions of 4-6 hours, and replace them with self-cleaning, which takes place in a single extended cycle of the machine. Unlike complex traditional cleaning methods, the self-cleaning process is simplified to the touch of a button on Husky’s Polaris HMI screen. In addition, self-cleaning is an automated process, which eliminates the need for the operator to enter the machine and can be performed as often as needed. With virtually no time penalty on production self-cleaning helps to overcome the contradiction between cycle time and mold maintenance, and aids in increasing productivity by significantly extending manual cleaning intervals.
The secret to the self-cleaning mold technology is controlled flash. Controlled flash is the intentional flash of the tool into the vents where dust and debris collects, using precisely controlled gaps to ensure flash does not travel beyond the target area. During a self-cleaning cycle, the vents are filled by the overflow of PET from the preform. The overflow of PET, called PET flash, then sticks to the dust in the vents, and the flashed preforms, complete with dust, are then ejected, leaving cleaned vents behind.
Self-cleaning mold technology is already being embraced by Husky’s customers. An established preform manufacturer located in the United States purchased the Reduced Maintenance Package with a new HPP5 system in early 2015. Traditionally this customer needed to manually clean the vents every 50,000 cycles or defects such as top sealing surface shorts, flow lines on the thread finish, or shorts in the leading thread would begin to appear in the parts. As their operation runs continuously they were sensitive to downtime, and with their existing mold cleaning methods they were having difficulty keeping up with required maintenance activities.
The ergonomic and downtime concerns with dry ice cleaning caused this customer to look into the development of costly equipment to automate the dry ice cleaning process. After discovering and implementing Husky’s self-cleaning mold technology, the need for dry ice cleaning was reduced drastically enough that this investigation has been halted. Using self-cleaning mold technology, this customer has reached 570,000 cycles and still does not require dry ice cleaning. Their estimated savings in maintenance time is more than 320 hours per year.
While self-cleaning does not completely eliminate the need for traditional mold cleaning methods, it represents a significant evolution that offers manufacturers increased flexibility in their operations. And while there will always be a need for methods such as hand and dry ice cleaning, self-cleaning addresses many of the common issues associated with these methods by minimizing labor and downtime, as well as reducing risk of damage to the mold and making the cleaning process safer.
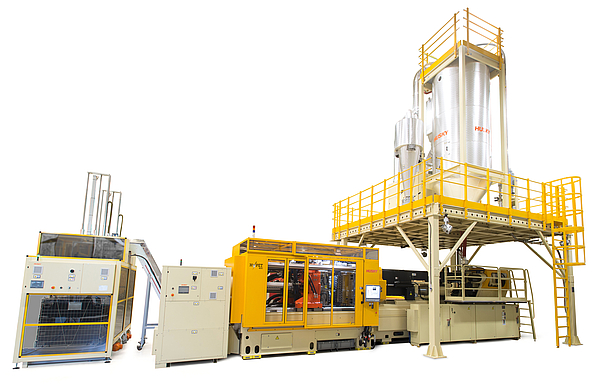
The comPETence center provides your organisation with a dynamic, cost effective way to promote your products and services.
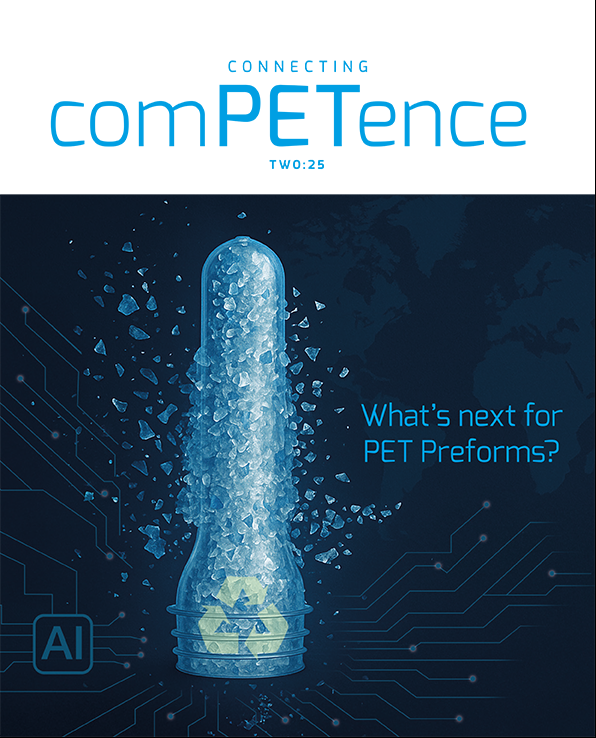
magazine
Find our premium articles, interviews, reports and more
in 3 issues in 2025.