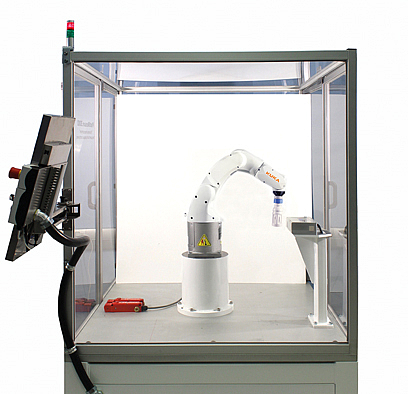
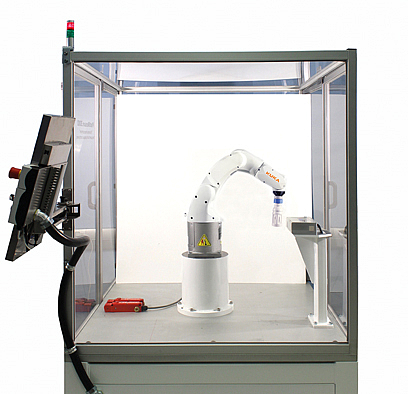
Terahertz metrology solutions are revolutionizing multi-layer wall thickness for distribution control process in the plastic container and preform manufacturing industry
Manufacturers are still manually measuring containers and preforms for overall and individual layer thickness. The processes are inefficient, destructive, labor intensive, and susceptible to operation error. Plastic containers come in all shapes and sizes, but today’s manufacturers are struggling to maintain manufacturing tolerances with complex branding based designs that are stretching the physical boundaries of plastic resin material flow. Constant rapid measurements are required by today’s manufacturers to ensure the products are meeting design specifications during start-up, production and tooling life cycle.
Leveraging the advantages of terahertz metrology, TeTechS has created a complete automated robotic system that solves all of these challenges.
Manufacturers of plastic bottles, plastic tubes, web and sheet products need to precisely measure the multi-layer wall thickness of the products with a noncontact, non-destructive technique, which does not use harmful radiation. Until now, plastic bottle and container manufacturers have been limited by labor intensive (and in many cases destructive) thickness measurement quality control practices. On one hand, techniques such as the Hall effect gauges are contact based and offer poor gauge repeatability, reproducibility and are only capable of measuring overall wallthickness – something that is insufficient when a multi-layer structure is involved. On the other hand, the manual cutting and measuring of plastic bottles which contain barrier layers is destructive, wasteful and susceptible to human error. TeTechS has led the market with installing fully automated measurement systems in key manufacturing facilities that are achieving immediate ROI. Current customers estimate their quality labour savings, scrap savings, and increased production time will return the equipment investment within 8-12 months after implementing the full TeTechS solution.
Although terahertz measurement technology has been explored in the scientific community for several decades, it has not been feasible to industrialize it until recently due to the size, complexity, and cost of the components. Terahertz waves are now widely deployed in metrology, spectroscopy, and inspection applications in many industries including aerospace, medical, pharmaceutical, automotive, security, food and beverage.
TeTechS is at the forefront of the emerging terahertz metrology category with solutions that are revolutionizing distribution control processes in the plastic manufacturing industry by leveraging the unique characteristics of its core terahertz measurement technology to automatically and nondestructively measure wall thickness in both opaque and translucent plastics. The measurement systems are combined with automation and are easy to implement on the factory floor.

Fig 1: Electromagnetic spectrum
Terahertz Metrology & Wave Properties
Terahertz metrology solutions are powered by terahertz waves, a form of light with its waves falling along the electromagnetic spectrum between microwave and infrared (fig. 1). TeTechS metrology solutions draw on the distinctive characteristics of terahertz waves that give it a distinct advantage over visible, infrared, ultrasonic or x-ray technologies.
Properties of terahertz waves include:
- Terahertz waves are in millimeter range and are able to penetrate all non-metallic material
- Terahertz metrology is a reflection measurement and is based on time domain thus it is a ‘true-thickness’ measurement. Thickness is calculated by measuring the time of light in each material type thus it is easy to separate the thickness of plastic and barrier layers in a typical plastic or sheet container wall structure (fig. 2)
- Terahertz metrology enables the identical precision measurements regardless of the material - opaque, light or dark. The gauge does not need to be recalibrated with colorant change as the change in refractive index (speed of light in a material type) is insignificant.
TeTechS gauges translate the waveforms reflected by the terahertz source and are received by TeTechS proprietary optical components and output into a userfriendly customizable user interface. TeTechS has developed a library of material properties that enable plant quality control managers to quickly enable precise measurements across many types of material structures.
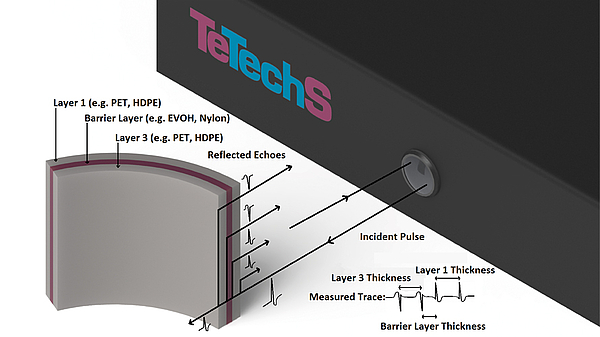
Fig 2: Measurement
Measurement
The PlastiMeasure 3000 utilizes the TeraGauge 5000 (Pic 3) to measure the layer and wall thickness of the plastic containers.
The system features:
- Measurements up to 10 layers with a minimum thickness of 25 micron with 10 micron accuracy
- The gauge R&R for the PlastiMeasure 3000 (repeatability and reproducibility ) is 4% including automation.
- The system is programmed to present the container to the gauge in a perpendicular position at the desired measurement point to enable the receiving antenna to capture the reflected echo. Factories are able to accurately measure difficult curves and corners in most containers that are impossible to measure using manual measurement techiques.
Automation
Today, most manufacturers are using both hall-effect magnetic gauges for overall thickness measurements and digital microscopes to measure individual layers. These measurement techniques have several drawbacks:
- Gauge R&R: with contact and destructive measurement techniques, gauge R&R is typically greater than 10%. TeTechS PlastiMeasure 3000 has gauge R&R less than 3% in a fully automated robotic system.
- Manual measurement methods are time consuming. It can take hours to completely measure selected points and layers of all the cavities in a rotary wheel blow molding system vs a few minutes in PM3000.
- There is a shortage of skilled quality control labor available in all shifts for a typical 24/7 manufacturing facility thus the production output during the offhours is of lower quality.
- Manual measurements and manual data entries are subject to human bias and error.
TeTechS metrology solutions enable rapid precision measurements to be implemented by manufacturing plants. Products are global and brand owners require consistent measurements and accurate data in multiple plants throughout the product life cycle. Although many factories desire to transition to Industry 4.0 practices, manual and destructive test methods for rigid plastics manufacturing do not align with the industrial evolution to the Industry 4.0.
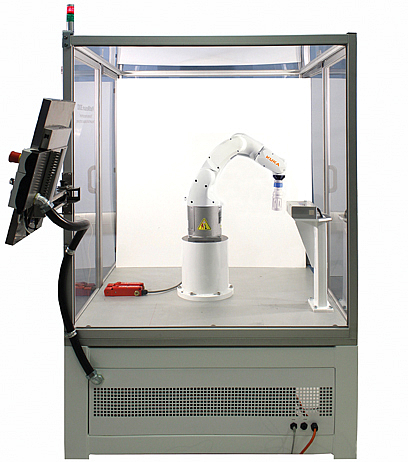
Fig 3: PlastiMeasure 3000
Case Study
A plastics manufacturing company was challenged with maintaining consistent distribution on a high production volume 250 ml plastic container with a challenging wall structure (picture – the customer does not approve including a product photo in this article). The TeTechS automated robotic system was implemented which enabled the customer to measure overall wall thickness and catch potential quality issues in real-time.
The quality control team was able to optimize the tooling and parison for an extrusion blowmolding line thus producing a much higher and more consistent quality product. Since TeTechS PlastiMeasure metrology solution was implemented, the production line has produced more than 100 million containers in the past 12 months in continuous operation with the previous quality issues resolved.
Benefits
TeTechS PlastiMeasure 3000 (Fig 3) is a fully automated solution that enables identical precise terahertz based thickness measurements to be taken safely and efficiently in a robotic cell:
- Data can be automatically uploaded to the plant SPC or reviewed by the operator in a quality lab or ‘at line’.
- Tolerances can be programmed for each measurement point and visually output so the operator is immediately notified of any points that are out of specification.
- The plant quality control team can save multiple settings that are recalled by the operator.
- The system is hands-off freeing the operator during the measurement cycle. Samples are loaded onto a conveyor feeder or nested tray and picked up automatically by the robot commencing the cycle and enabling the desired points to be measured.
- There is no calibration required after the one time parameter setting of the part in the PlastiMeasure 3000 system.
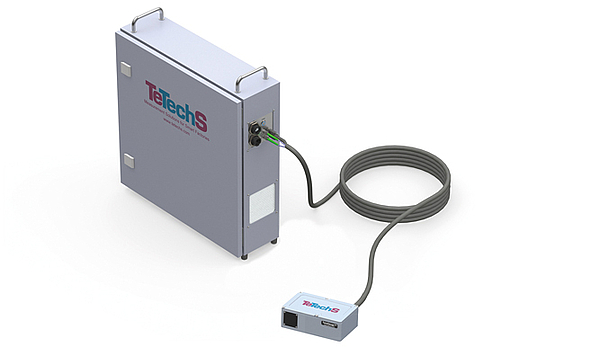
Fig 4: TeraGauge 5000
Conclusion
Terahertz metrology solutions are poised to change the face of rigid plastics manufacturing by providing faster, repeatable, and reliable non-destructive measurements.
Consumer preference for product packaging design experience is driving the desire of the brand owner for sophisticated packaging to retain and increase market penetration for fickle tastes. Increased container design complexity has created manufacturing headaches to control material distribution during the manufacturing process and maintain tightly controlled quality tolerances. Terahertz metrology based solutions are the must-have technology for rigid plastic manufacturing quality control.
Currently, terahertz metrology is deployed for many distribution control applications. With the technology rapidly iterating, manufacturing facilities are introducing the technology to automatically measure the barrier wall thickness with non-destructive testing.
One last exciting thought, we envision a future when the PlastiMeasure 3000 is installed at-line, with in-line sensors added to provide real-time measurements to 100% of the products being produced on the factory floor line.
(Read also “Terahertz Technology: A new wave in thickness measurement”; comPETence ONE:17, p. 66-68)
The comPETence center provides your organisation with a dynamic, cost effective way to promote your products and services.
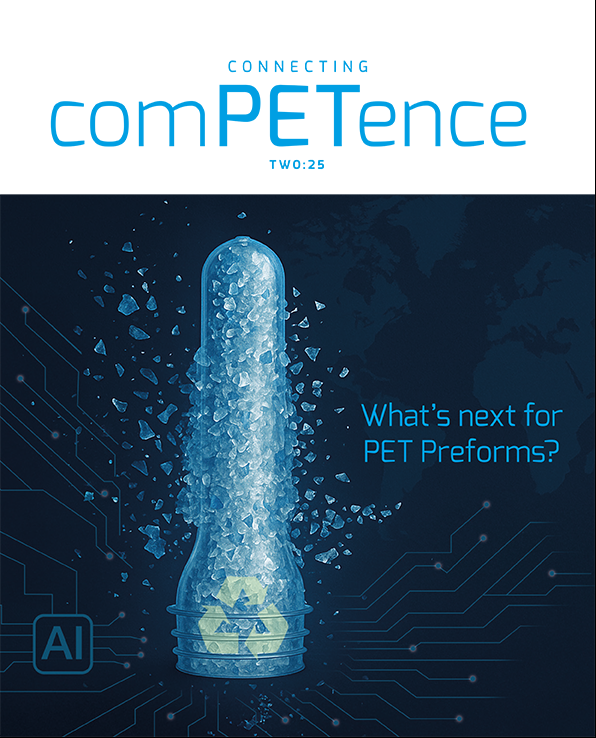
magazine
Find our premium articles, interviews, reports and more
in 3 issues in 2025.