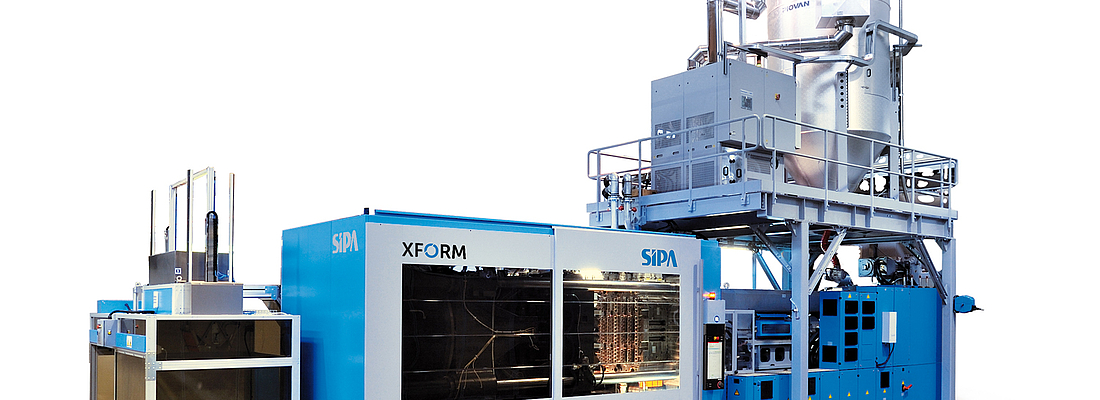
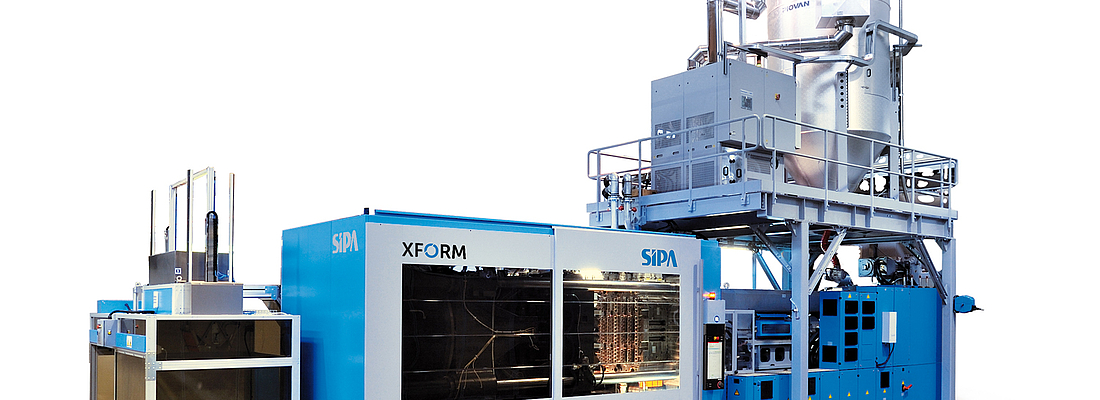
SIPA counts itself among the very few PET technology suppliers around the world capable of providing cutting-edge equipment to make high-performance, low-weight preforms and containers. As far as preforms are concerned, it is alone in offering not only traditional injection molding systems branded XFORM, but also a ground-breaking extrusioninjection-compression technology, XTREME, capable of making the lightest high-performance preforms possible.
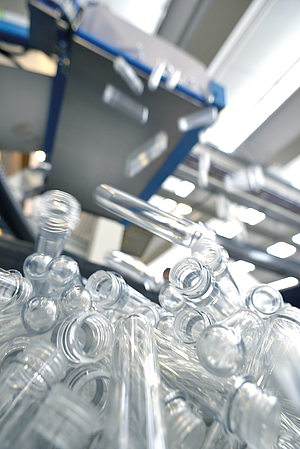
XTREME, already in commercial use at several customers, will take preform production into a new era, whether it involves virgin material or post-consumer recyclate, rPET. The advantages are especially significant when it is paired with EREMA’s Vacurema post-consumer bottle recycling system in XTREME Renew, another unique system, capable of producing high-quality food-contact capable preforms in up to 100% rPET flakes.
Fourth generation XFORM
SIPA has high hopes for XTREME and XTREME Renew. But at the same time, it is not taking its foot off the innovation pedal for injection molding. Here, SIPA offers quality and quantity in the form of XFORM. The world was introduced to XFORM in 2012, and already last year the system entered its fourth generation, XFORM GEN4 XP. This incorporates advanced technology to deliver the lowest conversion cost alongside unmatched speed, flexibility, and ease of use.
As is well-known, XFORM is available in several sizes, with clamp forces of 250, 350 and 500 tonnes. These can run with molds holding respectively up to 96, 128, and 180 cavities. New technology incorporated into all these systems has been designed to handle the most demanding applications. It delivers very short cycle times; it offers industryleading energy efficiency; and it has the lowest maintenance cost in the sector.
As with all previous XFORMs, the XFORM GEN4 XP accepts virtually all legacy tooling produced by any major mold maker.
Powered by the latest generation of servo-driven hydraulic pumps, the XFORM GEN4 XP has record-low lockto-lock time, paired with an increased injection rate. Total energy efficiency has also been increased: in a typical set-up with the machine set-up to full screw utilization and PET with an IV of 0.80, the XFORM GEN4 XP consumes just 0.195 kW of energy for every kg of material processed. One of the reasons for the improvements in dry cycle time and energy efficiency is the introduction of a kinetic energy recovery system acting on the toggle drive.
New accu layout
SIPA’s XFORM platform has already gained a reputation for its ease of maintenance, but on the GEN4 XP, it is easier than ever. One of the reasons for this is a modified accumulator area layout: the accumulators are now mounted on a pull-out rack inside the machine frame. In addition, the oil tank has been redesigned so that it does not need to be emptied in case of maintenance. Those processors operating in the hills and mountains – and there are more than a few – will also be interested to know that it can also be used at altitudes of up to 3000 m without any modifications.
The net result of all these improvements is that XFORM GEN4 XP users can operate even more consistently, at higher speeds, spending less on energy and maintenance, using a machine that will reduce conversion cost to very low levels.
The operator experience on the XFORM has also been further enhanced in the GEN4 XP. This is achieved through an HMI with a large 21.5-inch touch screen with high-definition graphics, swipe functions just like a smartphone or tablet, a multi-function control knob for one-handed operation, and fast response times unaffected by processor load. The HMI incorporates an advanced automatic process set-up and an indepth part quality troubleshooting tutorial, which together will help users improve machine up-time, lower scrap rates, and depend less on highly skilled machine operators.
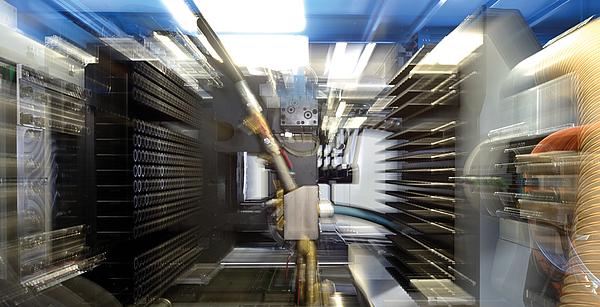
More open than ever
Apart from injection molding machines (and stretch-blow molding equipment incidentally), SIPA produces some of the best PET preform molds on the market, which is why many companies operating XFORM machines also choose SIPA molds. But around the world, there is a considerable amount of legacy tooling still being used, produced by diverse manufacturers.
One of the great advantages of the XFORM concept is its openness. It has led the way in its ability to accept preform tooling from other major producers. In recent months, SIPA has added new features to further facilitate use by its customers of existing tooling.
____________________________________________________________
FACTS & FIGURES
XFORM GEN4 XP
Production and machine data
Screw diameter: broad range, up to 140 mm
Throughput: up to 1.350 kg/h
Clamping force: from 2.500 to 5.000 kN
Example production data:
Preform weight: 25,7g
Neck size: 26/22 CMW
Mould: 96 CAV
Cycle time: 9,1s
Energy consumption: below 0,2 kWh/kg
____________________________________________________________
The new XFORM 250 GEN 4 XP preform injection molding system, for example, not only accepts non-SIPA molds and endof-arm tooling (EOAT), it also accepts pin plates for preform cooling and removal coming from alternative suppliers.
We are entering a period of great uncertainty. Buying decisions are going to be harder than ever to make for companies in a highly competitive business like rigid packaging. Allowing customers to use their existing pin plates on new SIPA machines is one of the latest examples of how SIPA is trying to make their lives a little easier.
No shaking
It is not the only way. A short while ago, a SIPA employee was watching an XFORM 500 system equipped with a 180-cavity mold running at full tilt, with a cycle time of 5.4 seconds. Normally, when a machine of that size and type is operating flat-out, it makes its presence known. The air vibrates, you may even feel throbbing through the floor.
Just out of curiosity, the technician put a glass of water on the frame of the machine. There was hardly a ripple on the surface.
This was not a one-off. It is a characteristic of all XFORM machines. And the larger machine, and the higher the cavitation, the more characteristic it is.
That goes some way to explain why XFORMs are so reliable. Vibration obviously puts stress in a system, and when that system is running fast for very long periods – which is often the case in PET preform production – that stress is significant. It can cause premature wear on moving parts, leading to high maintenance costs on the machine and the tooling, especially on large systems.
In fact, the clamping systems, linear bearings, tooling tapers – essentially the entire system structure – undergo massive stress. Component lifetimes drop. But the XFORM can operate with ultra-high cavitation tooling, with very short cycle times, and still run extremely smoothly.
What helps make this possible is an extremely robust clamp design and an extremely smooth clamping profile that comes from the servo-driven toggle. This yields a smooth performance that hardly wavers over time, helping keep maintenance costs low. In fact, maintenance costs on machine and tooling on the XFORM are significantly lower than almost any other PET preform system in the market.
XActive-cleaning cuts dust in hot runner systems
As was mentioned in the introduction to this article, SIPA has taken a highly innovative approach to tackling the problem of recycling used PET bottles in the development with EREMA of the XTREME Renew system. But this is not the only route that SIPA is pursuing: XFORM systems too can produce highquality preforms in rPET.
Special measures need to be adopted to make this possible, however, since rPET does have special characteristics. One of these relates to fine PET particulates – powder, dust, call it what you will – and how it can accumulate in hot runner systems. These are a concern in any preform processing system, but when it comes to rPET, the concern is greater.
Over time, PET dust builds up on the inside the cylinders of the actuators. Initially, this powder does not cause any problems, but as it accumulates, it inhibits the movement of the pistons, eventually severely compromising the quality of the preforms. If not treated, this accumulation can cause the system to seize up completely.
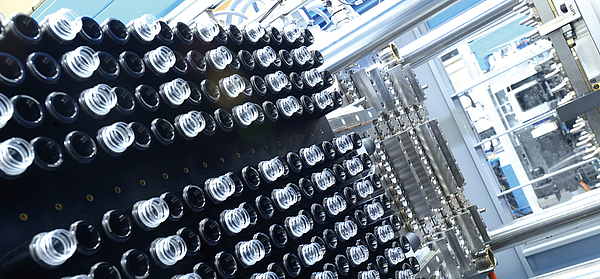
A more cost-effective solution
Important producers of hot runners have known about this problem for a long time, and a lot of work has gone into developing ways to counter it. SIPA is among the leaders in this area. It has developed solutions that keep production of dust to very low levels. With the growing use of rPET, SIPA several months ago decided to take a new look at dust, and to devise an easier and more cost-effective solution to the problem. Simplicity is key to ensuring that the risk of malfunction is minimized.
The highly ambitious goal was to have a complete hot runner system that needs maintenance only to carry out standard renovation operations – that is, to replace worn components. SIPA aimed for a system that could run continuously for five million cycles before those moving parts subject to wear – piston seals, valves, and so on – needed to be replaced. In a system running with a cycle time of seven seconds, that means it would be able to work continuously for 10,000 hours.
Guided by this vision, SIPA’s engineers came up with a system, which SIPA has since patented, which adapts the compressed air flows, normally used to move the hot runner valves, to also blow out the very few plastic particles that deposit inside the actuators each cycle. SIPA calls the system XActive-Cleaning.
XActive-Cleaning principles
The hot runner system is equipped with a supplementary circuit incorporating a series of valves which, controlled with appropriate logic, govern the entry and discharge of air from the cylinders, making sure that any PET dust particles created in the system are evacuated every cycle. This solution should on its own be sufficient to keep the system clean. But just to be absolutely sure, there is also a “boost” function that can be activated to perform a forced cleaning cycle, at intervals that can be set by the user (every 40,000 cycles for example). This process lasts for a few tens of seconds, so it has no impact on productivity
Minimal modifications to existing equipment are needed
A hot runner system incorporating XActive-Cleaning includes additional channels within the plates themselves, so there are no obvious differences from a conventional hot runner system, apart from an additional air connection with the XActive-Cleaning device. The cylinders for actuating valve movements have a special design, and there is also some special pipework feeding the box where the dust is collected.
This box is located on the ground near the injection machine’s HMI zone. The connection between the XActiveCleaning device and the machine is purely pneumatic. No changes at all are needed to the injection machine.
The XActive-cleaning system is machineindependent and operates using pneumatic valves operated by the same circuit that manages the movement of hot runner valve, so no modifications are necessary to the pneumatic system. The only extra task that the operator has to carry out is the regular cleaning of the easy-to-access filters installed on the external box.
Industry-leading expertise in very high cavitation molds
As already noted, SIPA has engineering expertise in molds and hot runners, as well as machines for PET preform injection molding systems. As an illustration of this prowess, SIPA not long ago conceived, designed, built, and delivered a preform mold hot runner system with 192 cavities for one of the world’s leading PET container makers, based in North America. This presented an important challenge in ensuring even and consistent filling of all cavities, at high speed, without excessive force. SIPA met the challenge with the help of its Xflow melt distribution system, which is now available for use on GEN3 and GEN4 XFORM 350 and 500 systems.
Xflow incorporates an innovative hot runner manifold design that SIPA believes provides the best balance of melt distribution in the industry. In fact, it exhibits the lowest pressure drop ever measured. That is one reason why the maintenance interval – five million cycles – is so long, since wear and tear are considerably reduced. Xflow makes high-cavitation systems possible, without having to compromise on balance, pressure losses, and the formation of acetaldehyde due to polymer degradation. Xflow can also be applied to molds with more modest levels of cavitation with equally impressive results. Xflow applies the most advanced concepts of polymer fluid dynamics to hot runner engineering.
By taking melt rheology aspects into account, it is possible to obtain balancing results quite beyond those of traditional systems. SIPA has been implementing Xflow in its hot runner systems for several years now.
The comPETence center provides your organisation with a dynamic, cost effective way to promote your products and services.
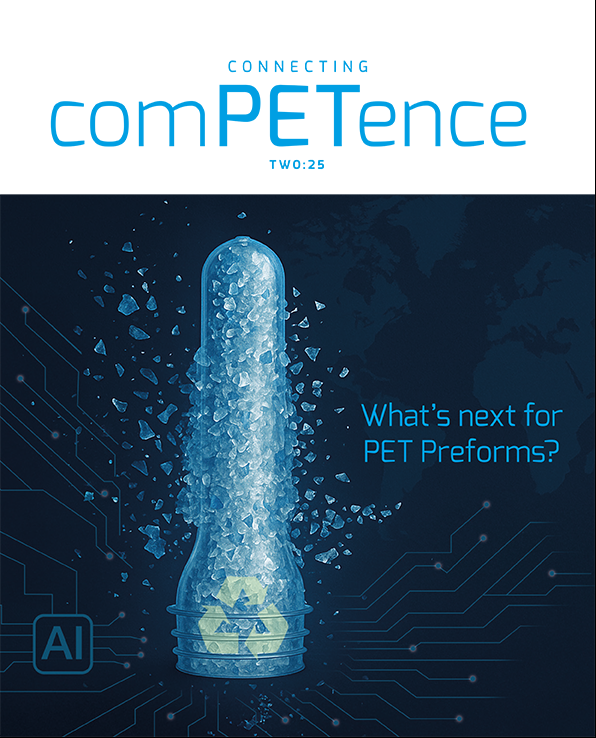
magazine
Find our premium articles, interviews, reports and more
in 3 issues in 2025.