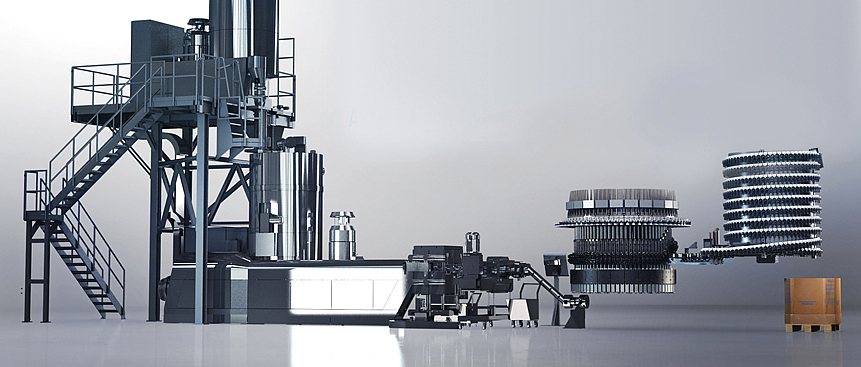
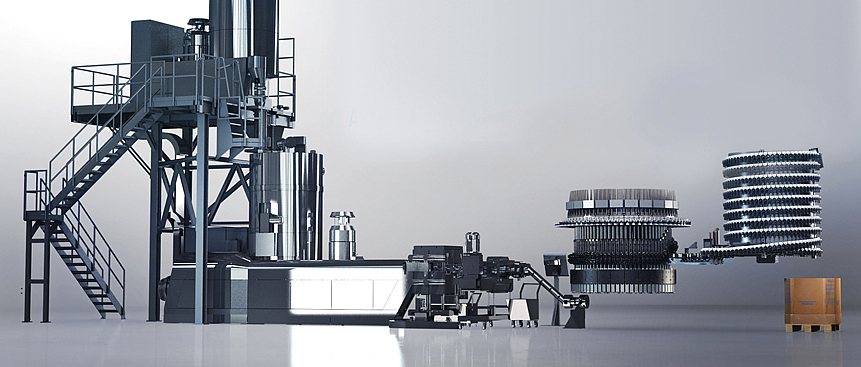
From washed flakes to food-grade preforms in a single thermal cycle – Circular Economy Becoming Tangible
SIPA-EREMA-Co-Development XTREME Renew converts post-consumer PET bottle scrap into preforms
The first process step (Vacurema by EREMA) converts conventional washed PET bottle flakes into decontaminated food-grade PET melt with increased viscosity (IV). The melt is then, for the second step, fed to the SIPA section of the compact plant, which produces preforms using the injection-compression moulding technology.
What makes it so special: The recyclate goes through only one thermal cycle. According to the codevelopers, the quality of the preforms produced in this way benefits compared to the standard process, in which the recyclate is granulated and then melted again: the yellowing is less, while the transparency increases. SIPA also highlight that XTREME Renew preforms are up to 10% lighter than conventional injection moulded preforms. In addition, XTREME Renew aims to reduce logistics and transportation costs by 20% and total operating costs by 15%.
The developing partners impress with further figures: Even with established rPET systems, preform production from recycled material already saves 60% of carbon dioxide compared to production using virgin material. With XTREME Renew, these emissions are reduced by a further 25% by integrating the various stages of the overall process into a single plant. Electricity consumption drops by 30%.
Back to the process: In the end, there are two options: A) The preforms fall into octabins. Or B): The manufacturer takes advantage of the compatibility and connect the SIPA stretch blow moulding equipment, continues the process and produces ready to fill PET bottles.
XTREME Renew technology found its first commercial application late last year: EREMA and SIPA collaborated with two Japanese partners – Kyoei Industry (a major recycling company) and Suntory (one of the largest beverage producers in the world) on an installation in Kasama in Japan. The system can produce over 300 million rPET containers per year. The Japanese companies have already ordered the second XTREME Renew line.
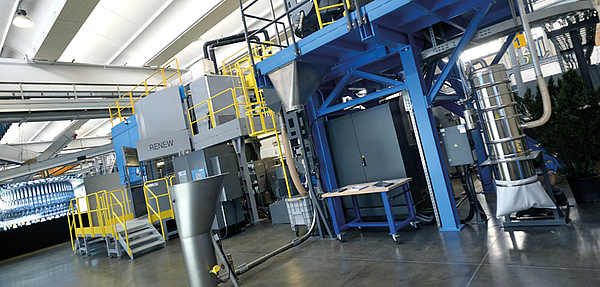
XTREME Renew – From Waste to Resources - The Interview
In July 2019, SIPA opened its doors in Vittorio Veneto, Italy, to provide a deep insight into the XTREME Renew system. We were allowed to be part of the event and, after interesting lectures and a comprehensive factory tour, had the opportunity for an intensive discussion.
CC: The really new technology of XTREME – preform production by Injection Compression Moulding – was intriguing at its first presentation at Drinktec Exhibition in Munich in September 2017 and the standard was literally revolutionized. Now the combination with the Vacurema recycling plant from EREMA. Here again opens up a new world. How did the development go?
AN: We started developing compression moulding for preforms ten years ago. Yes, indeed: 10 years! We were very excited about inventing an alternative to the standard process. We have developed various test machines. It was a timeconsuming process, there were also setbacks. In the end, we were able to prove that Injection Compression Moulding works for preforms.
CC: Did the idea of integrating upstream processes come up only after completing the development?
AN: Yes, exactly. Already during the development, we have anticipated further options and opportunities. When everything went well, we looked at the process and its potential. Its potential before and after the Injection Compression Moulding process. This coincided with the appearance of the plastic crisis: littering, attacks on plastic packaging, social changes. We recognized the opportunities - and the potential of the system.
CC: What are the key benefits?
AN: For this we first have to define the systems. Basically, it’s about the way from the rPET raw material to the preform. We compare the standard process - from rPET pellets to preforms - with the XTREME Renew combi option - from washed flakes to preforms. If I summarize this, then I can say the following: XTREME Renew uses less energy, emits less, saves material, produces faster. Not only do most of these points mean environmental benefits, they are also economic benefits as they save costs. From the economic point of view it is also interesting that the system is very compact, so requires less space in production. This saves on logistics and transport. And last but not least: The result, namely the preforms, are clearly different from those that are traditionally produced: they are lighter because they are thinner, and they are more transparent.
CC: From the strategist’s point of view, do you consider XTREME Renew more interesting for recyclers or for bottlers? What does it mean for converters?
AN: You have to approach this question by looking first at the overall situation. Currently there is uncertainty in the market. Of course, due to the bad reputation of plastic and plastic packaging, also regarding the questions of the upcoming regulations. Through changes in consumer behavior. Interested customers also have the following questions: Will there be enough material to recycle? Will the quality of the collected material be good enough? Will all this be reliably available? We understand that the current situation does not make it easy for our customers to make decisions, make investments. And - and this applies to all newly developed technologies - decision-makers must be convinced that a development keeps its promises.
CC: Imagine that there will soon be PET bottle scrap available in reliable volumes and good quality. What happens then?
AN: That can indeed lead to dramatic changes. For some time now, we have been observing that the brands are announcing new sustainability goals, for example by increasing the percentage of recycled content in their packaging. Interest in XTREME Renew has increased significantly since the launch. If the initial conditions are stable over time, namely the availability of collected PET bottle material in sufficient quantity and quality, then XTREME Renew, as fully developed technology, will be the favoured option for new investments. And there is another point: rPET should not be more expensive than virgin material
CC: Now we are back to the question: Is XTREME Renew more suitable for recyclers or for bottlers?
FP: It’s certainly easier for recyclers to change or expand their business model: with XTREME Renew they can sell preforms instead of rPET and achieve a nice margin. For converters, and even more for bottlers, with XTREME Renew they would have to integrate the recycling process upstream into what they are already familiar with. However, we believe that XTREME Renew will become relevant to both groups, simply because it will bring benefits to both areas. Above all, I think of the water preform.
CC: Does Europe have a pioneering role in tackling environmental and waste problems?
RG: Europe is certainly at the forefront when it comes to driving forward the percentage of recycled content. And we have never seen the European Commission and the European Parliament in such a short time ready to make decisions. They are very committed, so this is a priority, and therefore the amount of PET will soon be available. The question is the fight between the bottle-to-botte and the bottle-to-fibre recycling. Brand owners are moving, they are getting involved in the collection and claim some of the collected PET bottles for themselves. So, they want to get back the amount they put on the market. I am convinced that we will see big changes both in terms of legislation and in terms of quantities available. Europe is at the forefront. The other parts of the world will follow as soon as they see that the concept of circular economy is really successful. There is no other way.
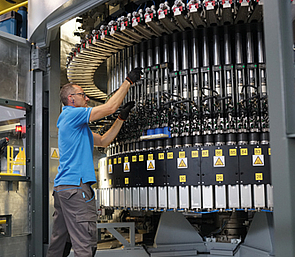
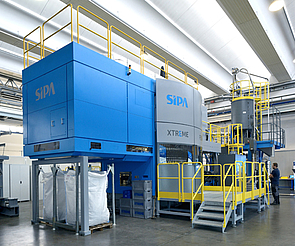
CC: Let’s take a look at the SIPA portfolio: When you travel to a customer and you have both concepts in your pocket: Standard and XTREME Renew. Which do you recommend?
AN: You want to hear that we only want to sell XTREME Renew. Still the following is essential: Only the best for the customer. Always individual solutions. In a large factory, Xform, our standard system, may fit better if the new investment is designed for compatibility. However, for a new business model, for example, if we are looking for an individual solution and we can help the customer save on production costs while increasing the sustainability of their production, then of course we recommend XTREME Renew if they want to produce rPET preforms. Not to forget the possibility to integrate our Xtreme technology directly into a blower and a filler block to save TCO and space with our XTREME Sincro Cube technology.
CC: How important is CO2 reduction for your customers?
AH: At the moment, the argument does not have the meaning it should have. CO2 emissions do not incur costs. Not yet. Should that change, if by law CO2 emissions should result in costs, this could be the first question customers ask.
CC: Today we learned a lot about the opportunities and advantages of the XTREME Renew, for example in terms of energy savings, also in terms of material savings, and the thinner preform base compared to the standard. What did you test and how did you do it?
AH: We started with applications for still beverages on the field, and now we are developing applications for CSD. We have done tests on various types of packaging, for example on single serve CSD bottles, we also tested lightweight bottles. We reached good mechanical performances, in terms of topload and also in terms of stress cracking. Even having less material in the base, the bottles were withstanding the requirements.
CC: I have a specific question about stress crack. In your presentation you said, “No stress cracking in preforms from the XTREME Renew system”. Stress cracking is a significant value for bottlers, brands like Coca-Cola or Pepsi. How did you test this and what are the results?
AN: We have performed proto tests in our lab and also with customers and the results have exceeded our expectations. From these results we have fully passed stress cracking resistance requirements by lightweighting the base of the preforms, and so stretching better the amorphous area in the base, and with the unique capability of the XTREME to reduce the crystallinity level around the gate. The reduction in the thickness of the preform base was -50% for single serve CSD bottles while for a 2.5-liter CSD bottle, a -35% lower thickness was achieved.
CC: The global economy seems to be cooling down, your competitors have just adjusted their earnings outlook. How is Sipa?
AN: You have seen our factory workshop: it is full. We have expanded our facilities; we definitely needed more space. And this year we have by far the best year for SIPA. With the traditional preform system. We still believe that PET as a packaging solution is more efficient and economical than others in terms of the environment and compared to cans or glass. What we need to manage is the collection of bottles. It is an educational matter, also a legislative matter.
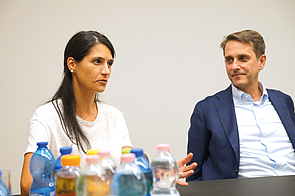
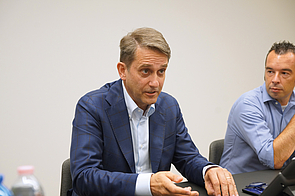
CC: For some time, we engineers have been dealing with something we are unfamiliar with: emotions. Our actions and pursuits are usually characterized by numbers, data, facts. Does the negative sentiment towards plastic packaging affect your daily business?
RG: We recognize the situation clearly. And we also take responsibility. We must all be committed to protecting the climate, preventing the further rise in temperature. At present, marine litter appears to be rated more negatively compared to climate change. However, we firmly believe that climate change is the real problem. Therefore, the reduction of emissions is very important. That’s why we’ve chosen a system that does not just focus on recycling plastics, but also saves lots of energy, logistics and CO2. In our view, this is a more global approach to the problem. To improve collection and recycling: The technology is there. Sorting, even with very sophisticated devices, is there. XTREME Renew is the next level.
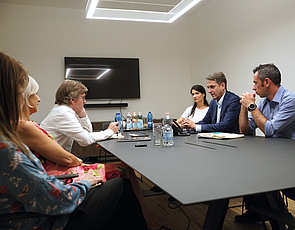
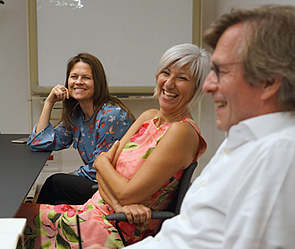
CC: Did we - as an industry - make mistakes? Not having the eye on the end of the chain?
AN: Basically, we engineers have the task to develop technical solutions, to improve systems, to make them more effective. We have succeeded very well over a long period of time: The industry, with all its competition, is working year after year to find better solutions in terms of costeffectiveness, total cost of ownership, energy consumption, lightweighting, and so on. The competition provides improvements year after year. The efficiency of the systems has developed incredibly compared to the time 10 or 20 years ago. The competition resulted in many performance improvements.
RG: Certainly, there were also omissions in education.
AH: I now realize that there are more and more partnerships between different parts of the industry. For example in our case: a recycling company that is partnering up with a beverage producer. This is something that has not been seen on the market before. Therefore, I believe that trying to bring together more and more stakeholders, taking into account the whole lifecycle of a material, will probably help to solve the problems that we have today, namely pollution. If we have failed in something, it is likely that we have focused on our own business, without looking behind us or in front of us.
RG: We did not listen to the preliminary signals. We were so successful with this packaging. We as machine manufacturers, and also the brand owners. The success of PET was enormous. When we saw the first signals, they were so far away. If we react too slowly now, we run the risk of failing because of our success.
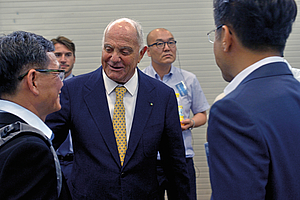
Gianfranco Zoppas: I believe it is vital that a circular economy is implemented as quickly as possible, or our industry risks becoming a victim of its own success. Without it, the levels of plastics packaging re-use will not be enough for a fully sustainable packaging sector. I hope and trust that our actions will provide an important boost in making PET packaging sufficiently sustainable for its future success.
CC: Do you see a chance to influence consumers more directly?
AN: As I said before, our main target is finding industrial solutions to solve problems. That’s what we did with XTREME Renew. So, we are ready, the development work is done, the result is ready for action. Everyone can use it: recyclers, converters, brands. If legal requirements are now created, then the technology is already ready. If we manage to stay one step ahead in the future, we will do everything right.
CC: Many thanks for this interview
The comPETence center provides your organisation with a dynamic, cost effective way to promote your products and services.
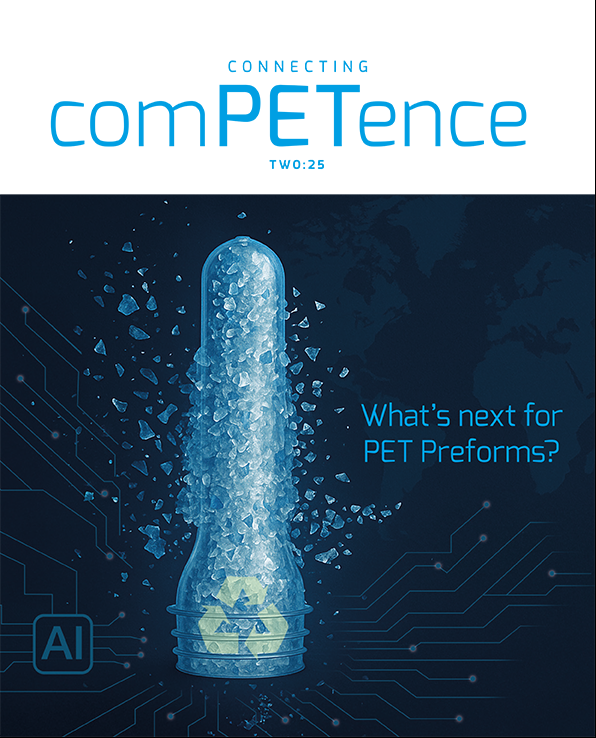
magazine
Find our premium articles, interviews, reports and more
in 3 issues in 2025.