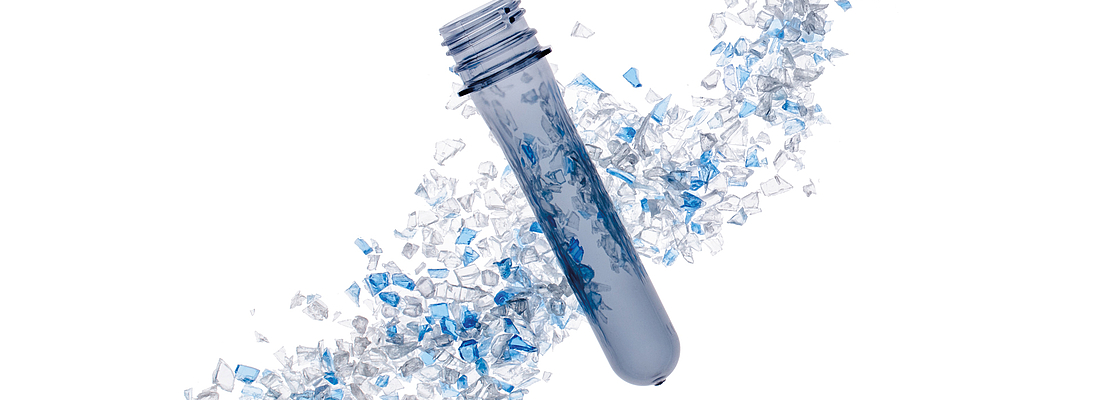
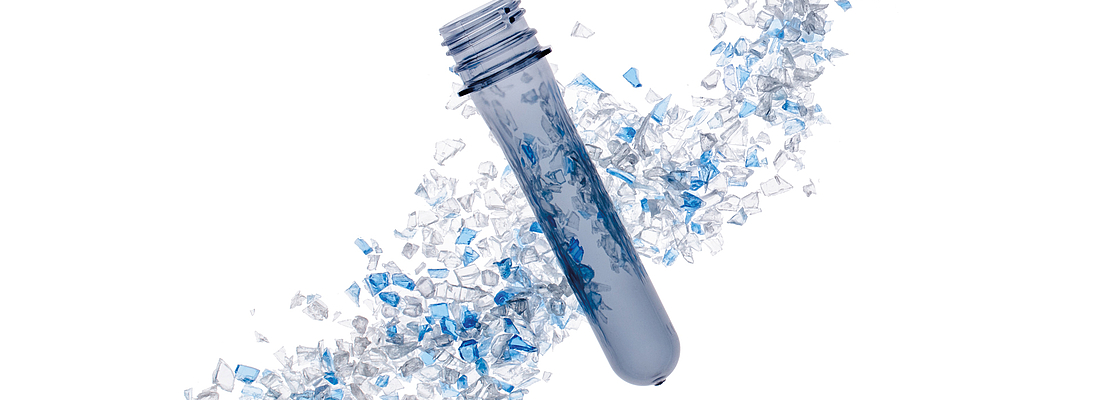
comPETence magazine | ONE:22 | Inspection and Digitalization
rPET and Preform Inspection in the Blowmolder - Understanding the Key Considerations, Benefits and Value
As the packaging industry continues to deploy necessary and ambitious sustainability initiatives, the use of recycled material has become standard practice, but not without a wide range of challenges for manufacturers.
The increased percentage of rPET/PCR in beverage bottles, in combination with lighter weights and faster line speeds, have created an environment wherein the delicate balance between optimum quality and maximum output is more tenuous than ever.
Furthermore, ever-stricter regulations continue to demand an unparalleled focus on food and beverage product and packaging quality so as to ensure consumer health and safety. Successful bottle manufacturers who are using rPET will get the most benefit and value from machine vision solutions when the inspection technology is deployed in the blowmolder rather than in standalone systems.
Garbage In, Garbage Out
The increasing use of rPET introduces distinct production-related difficulties. This is in large part due to the unpredictable nature of PET performance that results from a wide (and minimally controllable) range of material variability.
It’s important to point out that the absolute percentage of the rPET being used isn’t directly proportional to the increased risk of defects. This is because not all rPET is created equal – a small percentage of poor quality rPET can have a more significant impact than a higher percentage of good quality. So it can be a mistake to solely focus on the percentage of rPET; the quality is far more important.
Because of this, many bottle manufacturers have given greater attention to preform quality, in accordance with the old axiom “garbage in = garbage out.” Bad preforms become bad bottles; thus it’s logical to prevent a quality problem rather than react to one later. While there are a variety of strategies from which to choose so as to ensure the quality of the preforms, the critical role of machine vision inspection is more indispensable than ever.
The critical preform defects of the most interest include unwanted particles (rPET), stains or impurities within the plastic, improper stress distribution, ovality, “banana” preforms, and unacceptable color variation or haze. Additional critical defects include contamination, seal surface damage, and support ring cracks introduced between the IM machine and the eventual blow molder infeed. Bottles made with rPET have a much higher risk of improper injection and foreign matter contamination in the plastic, which leads to critical blow-forming defects.
There are several reasons why inspecting preforms is advantageous, and in some cases preferable, compared with inspecting the blown bottle. Because the preform is a smaller object, the camera’s field-of-view is therefore smaller, which results in a higher useful pixel resolution of the inspection image. This allows for detection of smaller defects by the inspection system.
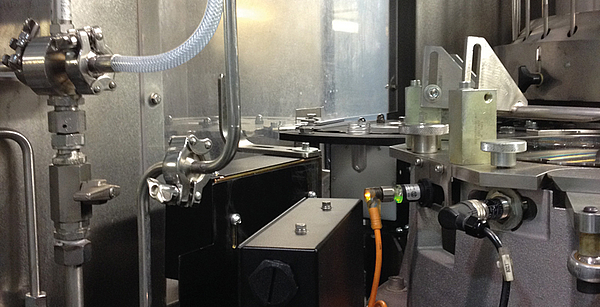
Another advantage to inspecting preforms is that the geometric facets which are molded into the sidewall of most bottle designs can serve as “hiding places” for black specks and other similar defects which are common to rPET. It’s far easier for the vision system to identify these inclusions in the straight wall of a preform when there’s no possibility that a shadow or other unwanted “noise” could affect the inspection image.
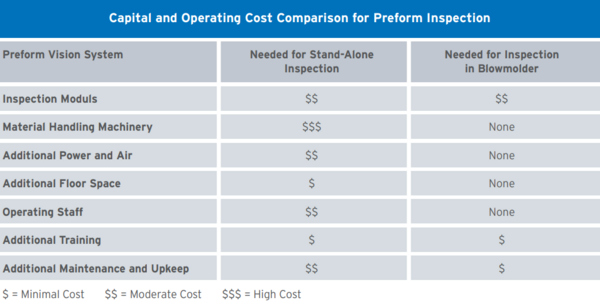
Because of this, it’s imperative to inspect 360-degrees of the preform sidewall. Most blowmolding machines do not have sufficient space to allow a 360-degree view of the blown bottle, thus some areas of the bottle sidewall may go un-inspected. But several leading inspection suppliers offer camera modules which image a full 360-degrees of the preform sidewall, thus maximizing defect detection.
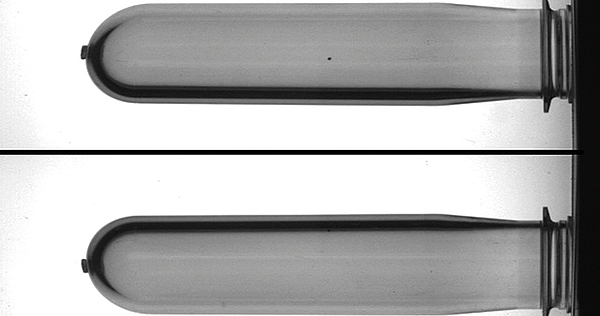
Beyond the common rPET-related flaws, many common defects are much more detectable in the preform state, such as bubbles, stones, long gates, etc. The leading vision suppliers offer a suite of inspection modules which are installed in the blowmolder to detect the vast majority of these defects without the need for additional or external material handling, which we will subsequently discuss.
It’s also worth mentioning that there is an economic advantage to identifying and removing defective preforms prior to blowing – put simply, blowing a preform into a bottle carries a cost. There’s no sound reason to add value to a defective part during the manufacturing process which will be rejected and scrapped later (or if not, could result in even greater cost in terms of product leakage and potentially brand damage further downstream).
Not a question of IF, but WHERE and WHEN
The issue then isn’t whether to inspect the preform, it’s determining the most sensible and valuable approach to doing so. Effective and accurate inspection is paramount, but one mustn’t lose sight of the cost vs. benefit balance, the impact on business / production processes, physical space and labor resources.
There are several off-line stand-alone systems which provide an extensive range of inspection capabilities, and this may be the primary objective for some bottle manufacturers. A stand-alone system may offer a broader range of inspections for characteristics such as the thread area or dimensional measuring, which could be more difficult to achieve in a blowmolder.
However, a compelling argument can be made that inspecting the preforms inside the blowmolder is the superior approach, both from a practical and an economic viewpoint – there’s no requirement for additional space, and very little incremental cost.
First, consider that off-line vision inspection requires material handling. The bulk of the total cost found in off-line preform inspection machines is in the material handling, which can make the capital investment quite high. Fortunately, the blowmolding machine already provides the requisite handling to inspect preforms. The introduction of compact camera modules into that space has been done successfully, and at much lower expense, for many years and across most major blowmolding platforms.
Also important is the fact that the more times the preforms are handled/transported during the process, the greater the risk of physical damage. In particular, the sealing surface and the neck support ring are quite vulnerable to nicks or chips which would not be detected should they occur downstream of an offline inspection machine. However, inspecting the preforms in the blowmolder is the optimal location to ensure that the most common or problematic defects, especially those related to rPET, are detected and removed, and with no risk of damage to the preforms.
Installation of a preform inspection system in a blowmolder, especially one in which bottle inspection is already deployed, requires minimal capital, no additional floor space, no additional staff or training, and no incremental operational or cost burden for power consumption, maintenance, change parts, or machine downtime for changeovers.
Data, Data, Everywhere
As Industry 4.0 initiatives continue to become mainstream business practices, the critical role of data in process management cannot be understated. Successful digitization of modern manufacturing facilities depends on the implementation of circular data flows which gather and analyze information about a process so as to optimize the efficiency of production machines.
The more closely-coupled the data is to the relevant process, the greater the impact that the data can have on process improvement. But disconnected processes and operations sever this relationship, or at a minimum reduce the operational value of the data. When a sophisticated inspection system is installed in the blowmolder, there can be immediate, real-time benefit to using the data stream to continually optimize the process.
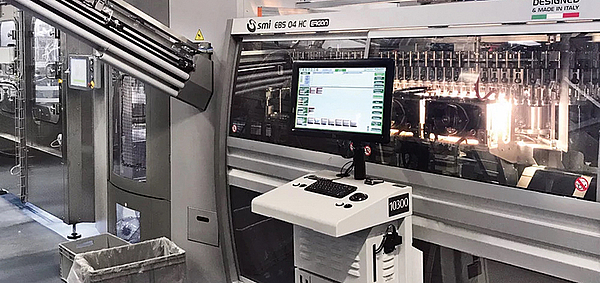
This is another reason most data-driven manufacturers are increasingly avoiding stand-alone machinery. Though much data may be gleaned from stand-alone inspection systems, that data is of little practical benefit in a fully-digitized manufacturing environment. The massive amounts of data acquired via the inspection system are of most value when that system is directly coupled to the production machinery.
The Broadest Capabilities at the Lowest Cost
Vision suppliers whose offerings include inspection inside the blowmolder commonly provide inspections for both the preform as well as the blown bottle. This may seem redundant and unnecessary, but there are good reasons why both are critical, especially when using rPET.
For reasons already described above, inspection at the preform stage detects many common defects which are very difficult to identify once the bottle has been blown. But there are a range of critical defects which occur during the blowforming process, such as base holes, under-blown bottles and improper material distribution. These defects must be identified as the bottles exit the mold.
The ultimate advantage is that a single vision system is capable of performing inspection operations in the blowmolder at both the preform and the bottle stage, and the most sophisticated systems allow for more than 12 cameras and sensors to be connected to a single control processor, improving ease-of-use and cost-effectiveness.
Photos: Pressco, Header: Shutterstock
The comPETence center provides your organisation with a dynamic, cost effective way to promote your products and services.
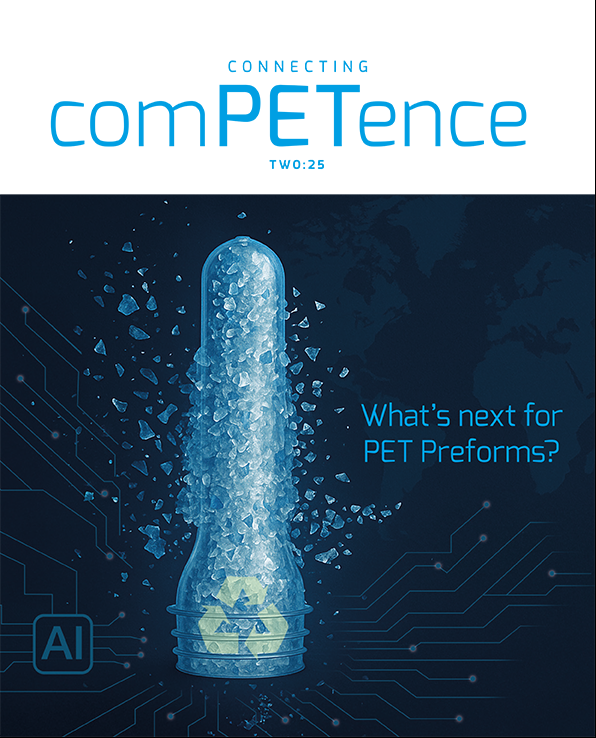
magazine
Find our premium articles, interviews, reports and more
in 3 issues in 2025.