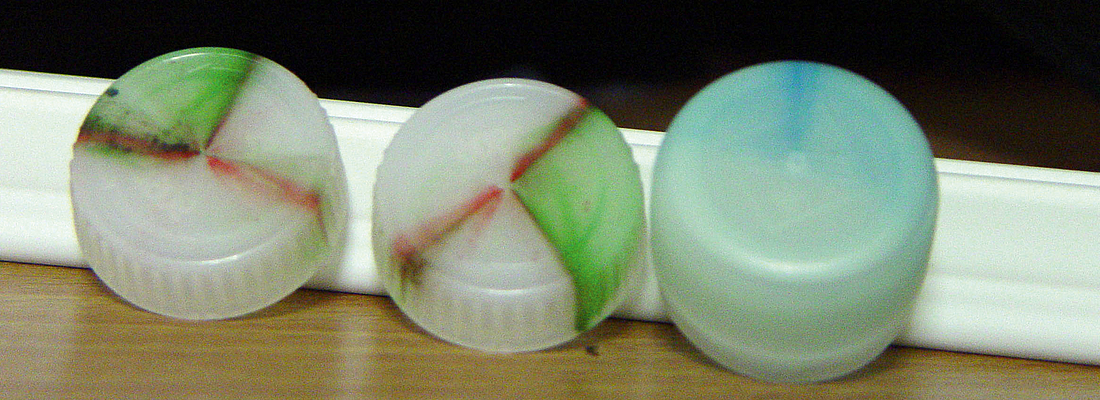
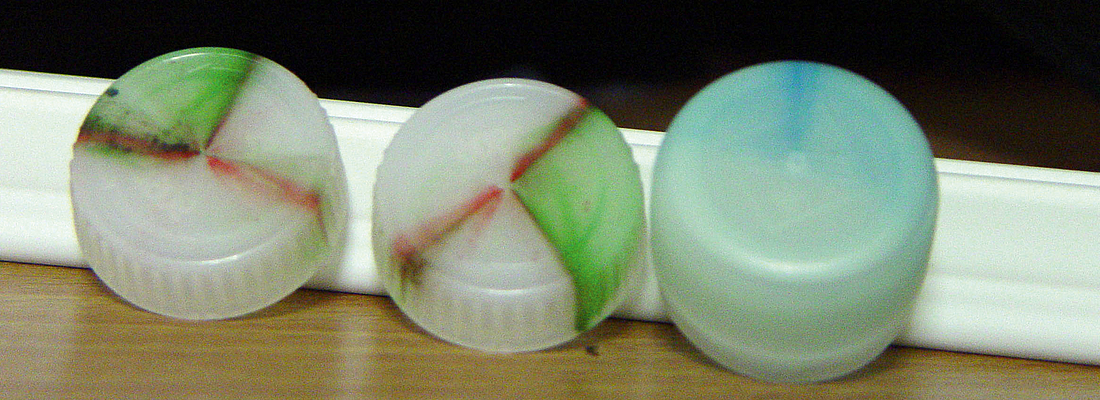
Huge volumes of plastic resins are wasted every day due to product contamination and ineffective changes to resin and/or colour. This large amount of plastic scrap has a significant effect on the environment. As a result, THE PROBLEM OF PLASTICS is a recurring topic in newspapers, television and other media.
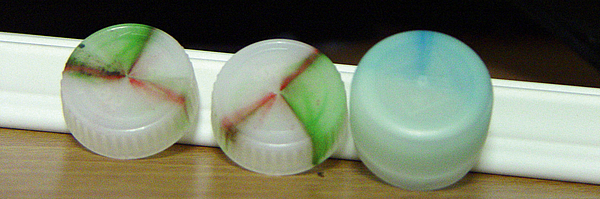
FIG 1: The first shots of processed pieces with so-called stripes
POLYMERS AND THEIR “LONG LIFE“
All polymers are generated from hydrocarbons or their derivatives, which originate from crude oil or biological sources such as cellulose, fatty acids or other sources. The chemical bond carbon-carbon and the other chemical bonds (C-N, C-H, C-O etc.) on which a polymer is based, remain very strong and stable over time. As a result of this feature, polymers have a long life, and are also weather resistant and extremely strong. This is why we can find them almost everywhere in our daily life in the form of various objects. But unfortunately, in addition to these positive features that make them suited for use in industry, they have a very low degree of biodegradability and consequently a significant environmental impact.
Due to this fact, it is very important that they are not thrown away, but recycled and re-used. We also think that it is important that as few virgin polymers as possible are turned into waste material before they have fulfilled the function for which they are processed.
A polymer cannot be recycled indefinitely
When a polymer is heated for processing, the heat stress causes the molecular chain of the polymer to break and oxidize, resulting in a weaker molecular structure and therefore weaker chemical-physical features. During the first processing this heat stress is not so important, because almost all polymers already contain stabilizing additives.
But if production becomes waste before entering the end-users market, these polymers must be properly recycled.
Production costs
When changing from a dark colour to a clear colour, the first shots of processed pieces have so-called stripes, or other kinds of contamination stemming from previous production. These shots cannot be reused for other clear colours and are typically reground in order to produce black or very dark coloured pieces (figure 1).
As not all companies produce large quantities of dark pieces, it is often necessary to recycle them. If we consider that a certain first choice virgin material has a price X, requires a certain quantity of electric energy E for its production, requires machine and operator time T, as well as regranulation time Tr and a quantity of energy for regranulation Er, in order to obtain a final product, which is decreased by the value Xr as compared to the initial product price, we observe a time and capital loss Ls (loss due to scraps) which can be quantified as follows :
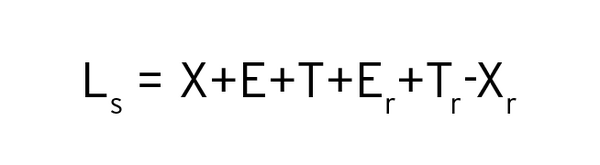
The value of Ls is much higher if the polymer is a so-called noble polymer. For example, this value will be higher for a crystal polycarbonate than for a polyethylene. Calculating the production cost Pc consists of the material used in production Xp, the energy used in production Ep and the machine and operator time Tp, minus the aforementioned loss:

From this equation we can deduce that there are three different ways of reducing production costs:
-reduce the waste production
-increase the production duration
-improve the regeneration process for scraps
In our opinion, point 1 is the best way to reduce the production costs, as it is not always possible to influence points 2 or 3. Modern purging compounds make it possible to produce between 2 and 200 times less waste during colour and/or material changes. Therefore we can now add a variable for the purging compound to our equation, considering the cost for the purging compound Xpu, the energy Epu and the time Tpu
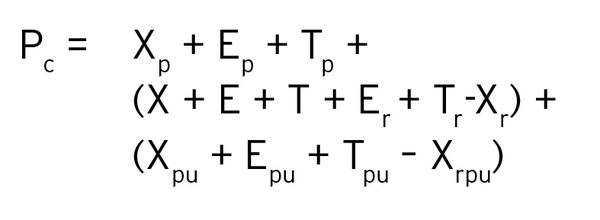
where Xrpu refers to the recovery from regranulating the purging compound. The following equation can be used to calculate the efficiency of purging:
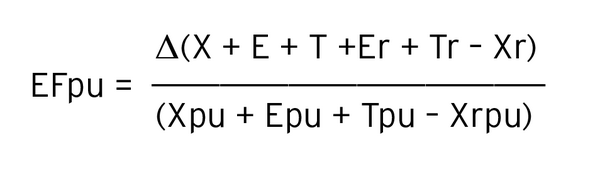
where ? (X + E + T + Er + Tr – Xr) is the differential of material, energy and time consumption for the colour change. The higher the efficiency of the purging compound, the lower the consumption of material for the scrap. And once again we would like to point out that time and energy factors have to be taken into consideration as they influence the production costs. Thus far we have spoken mainly of the production costs, which are certainly the first step toward efficient, competitive and correct production.
Let us now analyse the use of purging compounds from an ecological point of view: A company that produces several tons of waste per month can avoid up to 99% of this waste through proper use of an efficient purging cycle and careful recycling. We can state that ULTRA PLAST consists in a carrier material (polymers) and an active part which is made only of food and pharmaceutical materials, (exempted from REACH).
It operates at temperatures between 120-420° C and works by causing chemical reactions that remove the plastic residues from the cylinder wall and the screw. All that remains after use is a residual polymer material filled with inert minerals, which can either be disposed of as plastic waste or recycled as mineral-filled plastic. The resulting purged material can even be considered biodegradable, as the active part of the purging compound makes the resulting material foamy and porous so that it can be easily attacked by bacteria, rain and snow. But this is only true if the purge is controlled after the first phase, i.e. after it becomes foamy. If it is regranulated or re-moulded it behaves as a normal polymer charged with 5% inert minerals. If it is processed again and mixed with other polymers at 10%, it completely loses its biodegradability. This feature may be important for those who dispose of the purge waste (low environmental impact) and for those who re-use the purge in their production cycle.
Certified in compliance with FDA regulations (U.S. Food and Drug Administration) for use in food and pharmaceutical formulations, the ULTRA PLAST product is odourless, non-toxic and free of ammonia, silicon and wax. Its only by-products are water vapour and carbon dioxide.
All grades of ULTRA PLAST purging compound have internal chemical reactions which are activated by the heat of your plastic processing equipment.
This reaction, which is safe for the environment, for you and for the materials of your plastic processing equipment, releases a series of complex chemical reactions which vigorously attack residual resin. ULTRA PLAST is safe for humans or environment as it has the following features:
-Compatible with all thermoplastics
-Stabilized for elevated temperatures
-No mechanical scouring agents
-No corrosive chemicals
-Functions with a penetrating mechanism
-Remove deposits and degraded resins
-Made from FDA component
-Environmentally friendly
-Non-toxic ingredients
-Recommended for a variety of applications,
including hot runners
With the following benefits
-Less wear on process equipment
-More productive use of labour and materials
-Fewer product defects - less scrap reprocessing
-Up to 90% less downtime
-Improved performance
-Ammonia, silicon and wax free
-No need to dismantle equipment
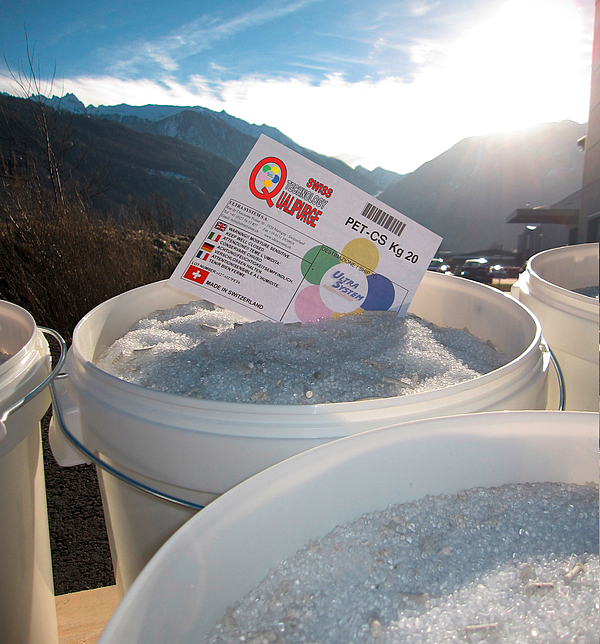
Now we can ask ourselves the following question: Wouldn’t it be cheaper to recycle all scrap production and wouldn’t there be fewer problems if purging compounds were used?
As we have already mentioned, saving time is important for production and saving energy is not only an economic factor but above an ecological duty for us all.
Above all as we already mentioned before, time saving is important for production and energy saving is not only an economical factor but above an “ ecological duty” for all of us.
What happens to a polymer when it reaches the consumer market if it has not been reprocessed correctly? Let’s take, for example, objects like garden furniture or other items exposed to weather or to mechanical and heat stress. The fragile characteristics of a reprocessed polymer will result in rapid wear and damage to the item produced, compromising its appearance and causing it to be disposed of sooner. Every manufacturer of plastics and plastic items is responsible for the costs of production, as well as for the costs, including indirect costs, to the environment as a result of production. Careful handling and using purging compound and professionally recycling scraps, manufacturers can avoid high production costs and unpleasant consequences for future generations.
However everyone can do something to reduce plastic pollution.
Plastic really is fantastic. The problem is improper disposal. Remember that a moment of carelessness may last for generations.
The comPETence center provides your organisation with a dynamic, cost effective way to promote your products and services.
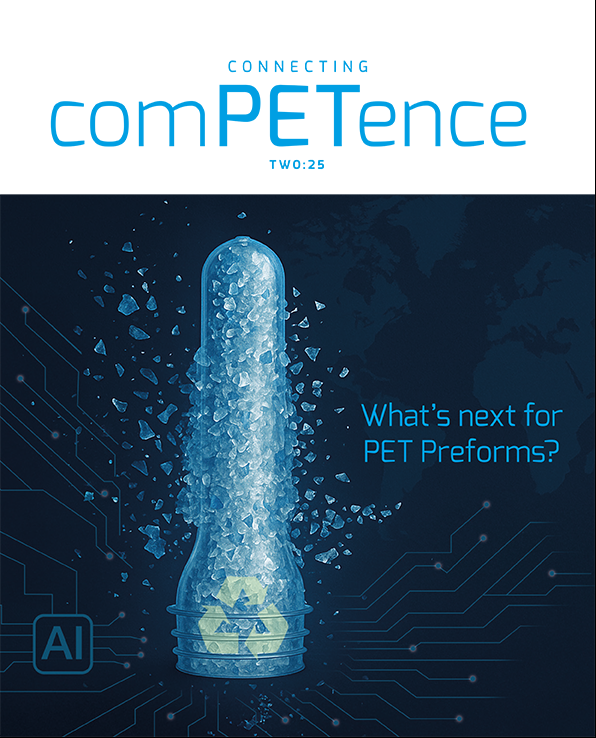
magazine
Find our premium articles, interviews, reports and more
in 3 issues in 2025.