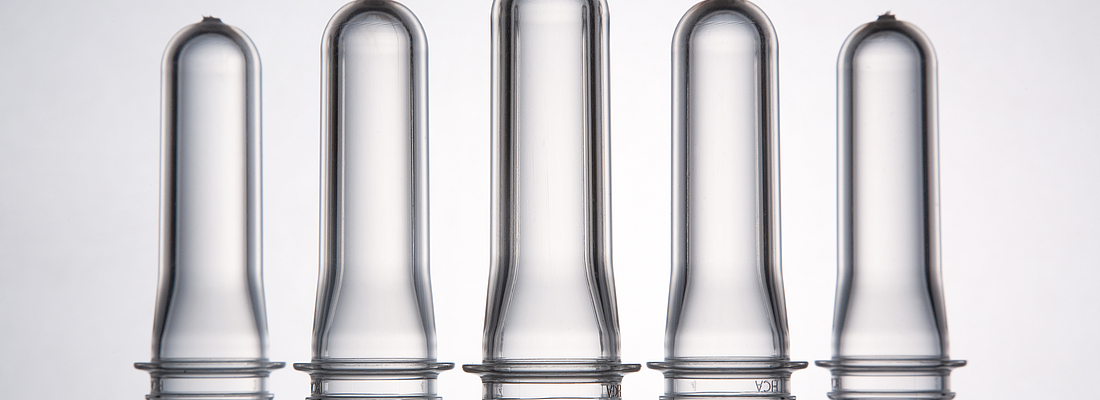
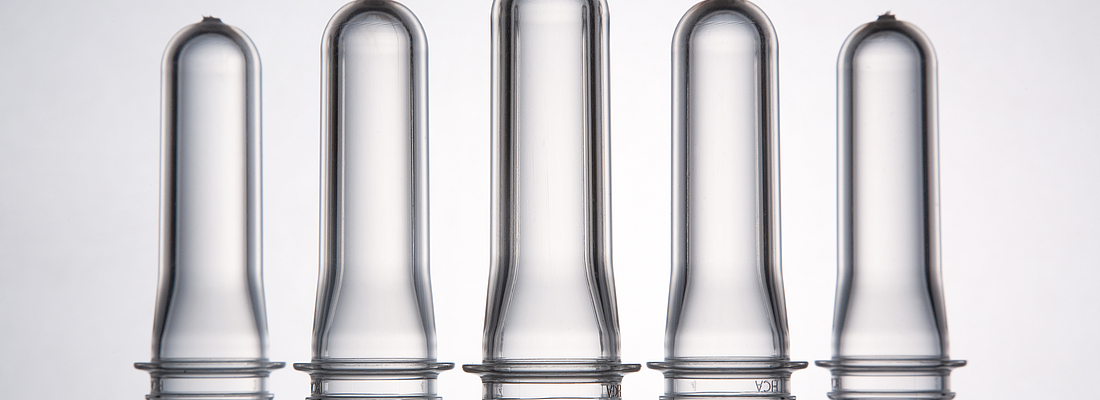
In today’s packaging market scuff marks and surface scratches are no longer acceptable on PET containers. During production of preforms, e.g. conveying and storage bin filling, the preforms fall, bounce and hit each other creating scratches. These are subsequently enlarged into visible surface imperfections during the stretch blow moulding process. One solution to this problem focuses on the reduction of the coefficient of friction (COF) during preform production. Lowering of the COF results in an easier release of the preforms from the cavities, scratch-free preforms and fewer drop marks due to lower friction from preforms falling into the octabin. Holland Colours’ new slip additive, Holcoslip 271-series, which has this desired effect, will be the main topic of this article.
Introduction
PET packaging looks and performs well and offers many marketing advantages in terms of design possibilities, user friendliness, mechanical strength, and cost. Ever increasing demands of brand owners and consumers for perfect products require producers to take complicated steps to prevent damage and preserve perfect appearance. In preform production, robotic collection and soft drop systems are one way to approach this problem, however, these involve significant investments and have a substantial impact on the factory infrastructure. Furthermore, this approach does not address the main cause of the problem: the high coefficient of friction (COF) of PET at the moment of ejection from the preform mould. During the manufacture of preforms this high COF can manifest itself in a number of ways:
A less than optimum packing density when preforms are packed into a box. This leads to higher storage and transportation costs.
Poor flow on conveying equipment and hence reduced throughput.
Surface defects due to poor scratch resistance and scuff marks caused by the impact of falling preforms on top of each other during release into e.g. the octabin and during conveying of preforms in general.
It is possible to reduce this COF by using additives. A cost effective additive system for polyesters that reduces the coefficient of friction of the polymer and thus overcomes the above deficiencies is therefore a much desired product.
Slip additives
Additives that are effective in reducing the COF of the surface of polymer products are known in the industry as slip agents or slip additives. In order to be acceptable for food contact and cosmetic containers, the fabricated polyester product containing the slip agent must exhibit low colour shift and high clarity, a minimum effect on taste and odour of the packaged good. Furthermore, the agent has to comply with international food contact legislation. This imposes other important requirements on a slip agent in addition to its friction-reducing properties.
Common slip agents for polyesters are ester amides and aliphatic esters, as can be understood from recent (patent) literature. The slip additive itself is added during the injection moulding process The working mechanism of these slip additives involves the migration of the additive to the surface of the preform, thereby forming a very thin film which is responsible for the reduction of the COF.
However, known slip agents do not all perform sufficiently well, high dosing levels are required (increasing costs), and hence there is room for improvement. Other slip agents have the disadvantage of a melting point only slightly above ambient temperatures in industrial environment, which makes them difficult to handle in such an environment. To overcome this, masterbatch concentrates with typically lower loadings than 50% are used, with a much lower effectivity and higher cost. Holland Colours’ new slip additive, Holcoslip 271-series, is a liquid which performs very well at low dosing levels, as will be shown in the following paragraphs, and also meets the above mentioned requirements.
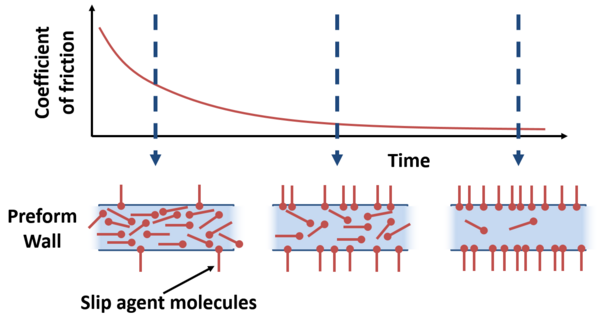
FIG 1: Schematic depiction of the working mechanism of slip additives
Determining the coefficient of friction
To objectively determine the effectiveness of slip additives it is common practice to use the method described in ASTM D-1984 adapted for plaques. The procedure makes use of a moving sled with a sample plaque moving over a stationary plane with a second sample plaque. The ratio of the force required to move one plaque over another to the total force applied normal to those surfaces gives the coefficient of friction. The kinetic coefficient of friction, which is the coefficient of friction once the plaques are in motion, was deemed most representative of the interaction of polyester articles in real life situations and therefore this value was used to compare the slip agent samples.
Measurements
The COF for several candidates was determined. Plaques were measured approximately 1 hour after injection moulding after storage in a climate controlled environment, to exclude influence of temperature difference and moisture on the test results as much as possible. The COF of several examples is shown in Figure 2 as a percentage of the COF value of the PET reference sample without additive.
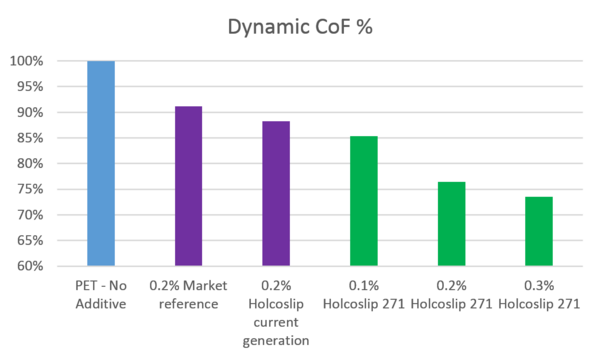
FIG 2: COF determined for several slip additives vs PET reference without additive
Conclusion
The results show that all candidates have an improved COF vs the PET sample without additive. However, Holcoslip 271-series already presents better slip performance at half the dosing level vs alternatives. Next to this typically at least 10% more preforms can be stored into an octabin compared to those containing no additive, reducing storage and transportation costs. The new generation slip additive can also be used at a considerably lower dosing level, typically to 50% lower, to reach the same effect as competitive solutions in the market. Furthermore, Holcoslip 271-Series is compatible with most liquid additive / colorant dosing systems.
Holland Colours has been supplying colorants and additives for the PET packaging market for almost four decades. Our latest developed new generation slip agent (Holcoslip 271-Series) expands this portfolio to provide our customers with more efficient and cost effective solutions.
The comPETence center provides your organisation with a dynamic, cost effective way to promote your products and services.
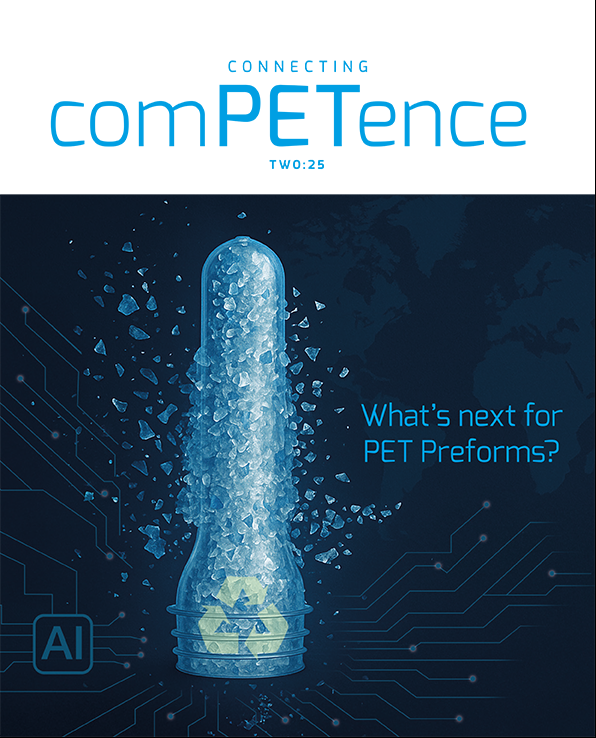
magazine
Find our premium articles, interviews, reports and more
in 3 issues in 2025.