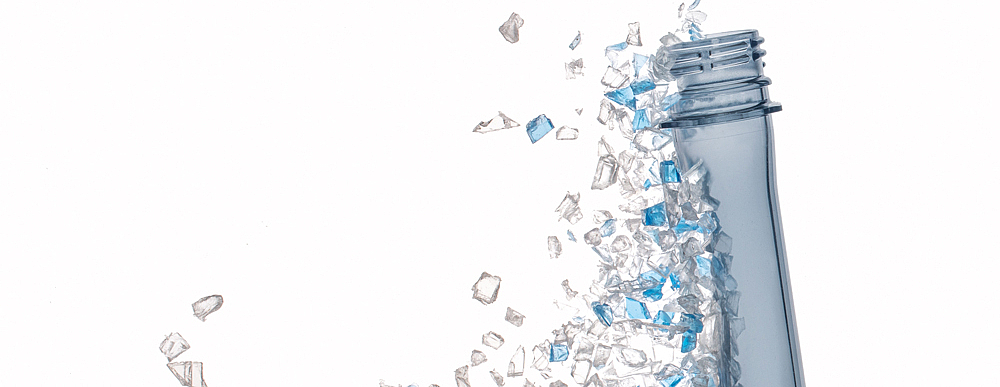
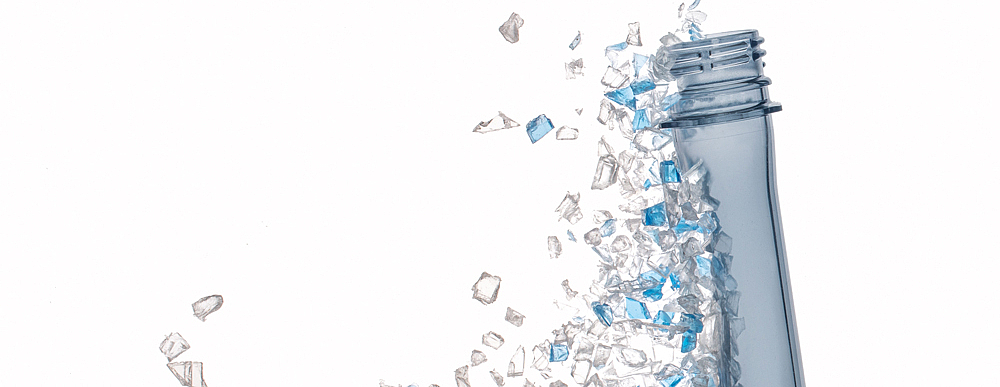
(Photo credit: Shutterstock)
PET flake production
Petainer launch Petainer IR Flake, a new rPET source
Interview by Dr Otto Appel with Dr Michael Joyes, Program Manager at Petainer.
Where is the plant for the production of rPET located?
Petainer IR Flake will be produced using 100% renewable energy in Aš, The Czech Republic. With an enviable central European position, Petainer also serves markets with One-way Preforms, Reusable PET Bottles as well as Reusable 5GAL Water Cooler Bottles, and Oneway Kegs.
What capacity does the system offer?
5,000 tonnes/year.
When will the system go into operation?
Petainer are launching Petainer IR Flake to the market in Q1 2022, with final commissioning of the line completed in November of this year. Petainer will become the first to create preforms from this recycling process.
Is the material flow ensured for the capacity of the plant? How do you manage to ensure this?
The Petainer IR Flake system will complement existing recyled PET streams from a range of hot-washed flake sources. Existing and future Oneway Preform and Reusable PET Bottle customers will have the option to sell baled bottles directly to Petainer, providing the ability for our customers to achieve closed loop recycling.
From which catchment area and from which sources does the PET material to be processed come?
The flake input will be sourced from the German Deposit Return Scheme, where high quality, food grade origin flake can be accessed as well as from the recycling system in the Czech Republic.
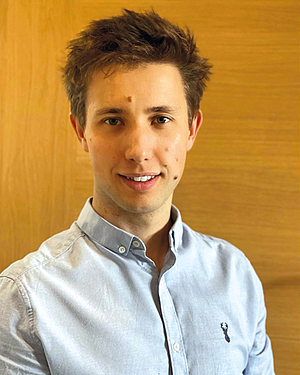
What type and quality is the feedstock?
The feedstock is clear hot-washed PET flakes from greater than 95% food origin. This is guaranteed using Deposit Return Schemes.
How does the process for manufacturing the rPET flakes work?
When Petainer decided to invest in a new recycling process, they started with what the end consumer was looking for; clear bottles with few imperfections, manufactured sustainably. This drove the decision to opt for flakes instead of pellets, building on Petainer’s 25 years of processing rPET flakes. The process subjects hot-washed PET flakes to infra-red (IR) light in a rotating drum to remove moisture and contaminants.
The flakes are maintained within a set temperature range for a given residence time to meet the strict conditions needed for food-contact. The rotating helix-drum ensures consistent exposure of the flakes to IR light. Finally, the flakes are subjected to a finishing step in a desiccant drier prior to use. Petainer’s process removes the energy intensive extrusion step, and as this means less melting, the product has better colour values and a lower CO2 footprint.
Does the process end with PET flakes or can rPET granules also be produced?
The process currently ends with the production of food contact rPET flakes, which are then used to produce PET preforms. There is the option, in the future, to extrude these flakes into pellets.
Which applications are possible with the Petainer rPET flakes?
Petainer believe strongly in the circular economy, so ensuring that they could provide a closed loop option for customers was a cornerstone of the investment in this new project. Petainer IR Flake is food contact safe, which allows Petainer to use it for new preforms and bottles, as opposed to sending for use in other industries such as clothing and manufacturing. Petainer IR Flake will be used predominately for beverage applications including water, carbonated beverages, juices, beer, alcoholic drinks, as well as food and household products. Crucially, customers can opt in for bottleto-bottle recycling and create a closed loop for their products. We can inject up to 50% Petainer IR Flake and mix with 50% rPET pellets to provide 100% rPET solutions. In the future we will look to add the process of extrusion of rPET flakes into rPET pellets to provide customers with the widest selection for their products.
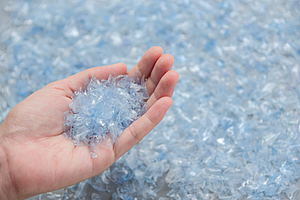
Are trays also processed?
Currently only hot-washed flakes from beverage bottle sources are planned for use as input.
What is Petainer’s view of alternative recycling processes such as chemical and enzymatic recycling?
Chemical and enzymatic recycling processes show promise for applications where the input of rPET flakes is not of sufficient quality to be mechanically recycled. The cost, energy and carbon footprint of these technologies makes them unsuitable for the processing of high-quality PET waste, where mechanical recycling should be used.
Why is Petainer entering the PET recycling business?
Petainer has a long history of manufacturing PET packaging with sustainability built into the products it creates. In the Nordics, Petainer are the largest convertor of rPET flakes with their Lidkoping factory now processing more rPET material than virgin PET material. To support customers in Central Europe to increase to similar levels of recycled PET in their products, it was decided to invest in a process to replicate the successful business model in the Nordics, whilst guaranteeing supply and quality. The process to make Petainer IR Flake is energy efficient, removing energy intensive steps such as extrusion, resulting in a lower carbon footprint than rPET pellets and other rPET flakes on the market. This means Petainer customers who can achieve a closed loop, will receive the maximum benefits for switching over to IR Flake.
Why did you decide to produce rPET flakes?
Petainer has been converting rPET flakes into preforms for over 25 years and are considered experts in the intricacies of using this form of recycled PET feedstock. There are several advantages of using PET flakes over rPET pellets, due to the lack of an extra melting step to convert flakes into pellets, these include a lower carbon footprint, less yellowing and fewer volatile organic compounds. This technology complements extensive knowledge of using rPET flakes, along with ambitions to increase recycled PET use for our customers.
What economic advantage do you expect from it?
Increasing numbers of brands are putting the climate and environment at the forefront of their thinking, looking to reduce carbon emissions and ensure their products are recycled successfully. This comes as EU legislation to protect the planet comes into force. These changes put demands on the amount of overall rPET, leading to both challenges of availability and quality. Using rPET is the most effective way of reducing one’s carbon footprint as it has a quarter of the greenhouse gas emissions as virgin PET. Petainer IR Flake will add to the amount of available rPET, and Petainer will continue to work with its customers to meet their carbon reduction targets and build strategies to achieve net zero goals.
What role does the decision play with regard to the image as a packaging manufacturer?
The investment into recycling technologies demonstrates Petainer’s commitment to PET as a sustainable packaging solution. It is well known across the packaging industry that PET has the lowest carbon footprint of all packaging types, and this investment shows that Petainer intends to reduce this carbon footprint further through the inclusion of ever greater levels of recycled content. The inclusion of rPET serves not only to reduce the product’s carbon footprint, but also to increase demand for recycled material, increasing collection rates and in turn reducing plastic waste.
Does the installation have the character of a pilot project or will it remain the only system?
This is the first installation of this system for a PET convertor focused on preform manufacturing. If successful it could be envisaged that this process would be replicated at other Petainer sites.
Who are the buyers - besides Petainer itself - for the preform and bottle business?
We are the first in this industry for preforms.
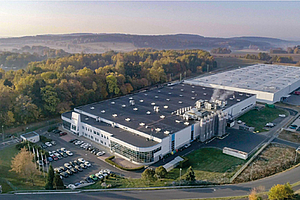
Where does Petainer see the PET industry in terms of sustainability and consumer reputation in 2030?
It’s no secret that plastic packaging has come under fire in recently because of the serious issues of plastic waste leaking into the environment. To some extent, the PET bottle has been a victim of its own success due to its low cost, lightweight and versatile nature. PET bottles meteoric rise as a packaging solution since the first PET bottle patent in 1974 has allowed brand owners to rapidly expand their product lines globally. The darker side of this has been the leakage of packaging, at intolerable levels, into the environment.
The correct response to this must be twofold. Firstly, PET “waste” must no longer be seen as waste, but as the truly valuable resource it is, due to its fully recyclable nature. A combination of legislation and consumer demand for an increase of recycled content in PET is going some way to change this perception.
Secondly, simple and robust collection systems must provide consumers with an easy and practical way of recycling PET that maintains its quality and prevents contamination from other recycling streams. Deposit Return Systems provide one such way to ensure that high collection rates are reached.
Reusable products are proven to be the most sustainable. They reduce the amount of virgin material required and greenhouse gas emitted. Reusable PET bottles are therefore increasingly important in the global supply chain. Currently they have limited but effective use in Germany, where the population has adapted to incorporating reusable bottles in their daily lives. Adoption of reusable systems outside Germany will ultimately reduce plastics waste but investment is required. Petainer continues to lead the way in this market with improved designs to increase the number of trips, whilst incorporating higher levels of rPET content.
''The correct response to this must be two-fold. Firstly, PET “waste” must no longer be seen as waste, but as the truly valuable resource it is, due to its fully recyclable nature.'' - Dr Michael Joyes
By 2030, with high collection rates, high rPET inclusion and a higher market share of reusable PET products, PET packaging will be seen as the low carbon solution fit for the circular economy.
What significance will PET recycling then have for Petainer?
It’s clear that the demand from the consumer, reflected by brand owners through their rPET inclusion and carbon reduction targets, is for ever increasing rPET inclusion. The challenge for PET converters like Petainer is to ensure they can meet this demand with high quality rPET sources.
The comPETence center provides your organisation with a dynamic, cost effective way to promote your products and services.
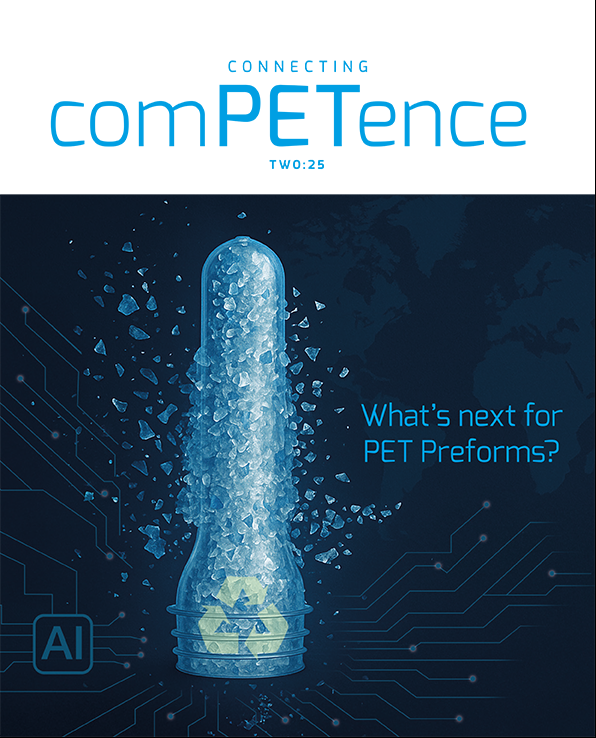
magazine
Find our premium articles, interviews, reports and more
in 3 issues in 2025.