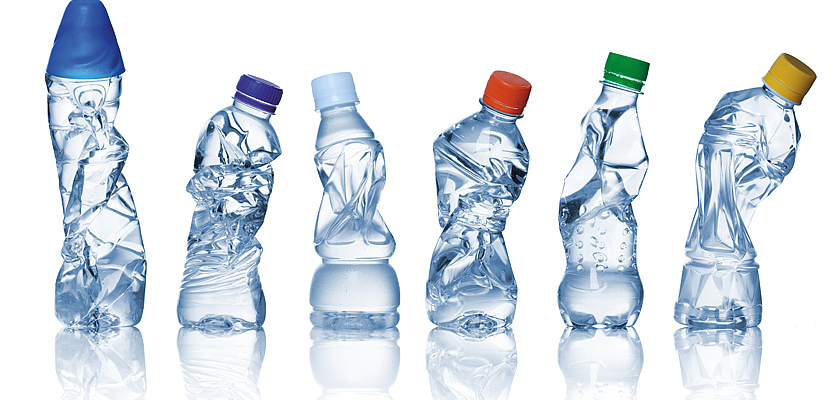
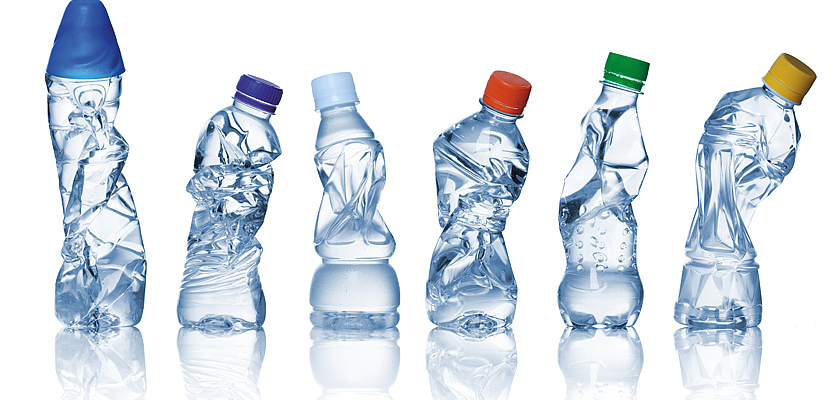
STRETCH BLOW MOULDING
PET to the limit - Determination of extensional material properties from PET close to failure.
The simulation of the stretch blow moulding process at high stretch ratios and high strain rates is not yet state of the art, as models to describe the phenomena occurring there are missing. At the Institute for Plastics Processing (IKV) at RWTH Aachen University, these models are being developed with the use of a Membrane-Inflation Rheometer.
The two-stage stretch blow moulding process enables the economical production of high-quality plastic containers with excellent mechanical and optical properties and at the same time low material consumption /1/. The material used is almost exclusively polyethylene terephthalate (PET), since the processing and moulding properties of PET are particularly suitable for the stretch blow moulding process. About 81 % of the manufactured quantity of PET packaging is used in the beverage industry, but the market share of food packaging and non-food products such as cosmetics, oils and cleaning agents is also growing steadily. By realising lower wall thicknesses and higher stretch ratios, the industry is striving to continuously optimize the material efficiency of these products, since about 70 % of the total production costs of stretch blow moulded PET bottles are determined by the cost of the material /3/. The design of plastic containers with very thin walls can be economically implemented with the simulation of the stretch blow moulding process.
For the design of extremely light preforms, however, current simulations are only capable to a limited extent, since neither the strain rate- and temperature-dependent material model nor the material failure can be modelled accurately at high strain rates (> 5,000 %/s) and stretch ratios (> 5) /4/. Therefore, a failure criterion is to be added to the stretch blow moulding simulation with the aim of predicting the material failure in the forming process. Material failure is defined here as the so-called stress whitening, i.e. the white coloration of highly stretched semi-crystalline plastics. The amorphous matrix between the crystalline areas is stretched so far that intramolecular defects are created. The incident light refracts at these defects and the translucency of the plastic decreases /1/. The extended simulation of the two-stage stretch blow moulding process allows a material efficient development of plastic containers with wall thicknesses just below the failure limit. This paper therefore describes the determination of the material data required for the simulation.
Material behaviour of PET
The crucial factors influencing the mechanical behaviour of the material when stretching PET in the stretch blow moulding process are primarily the strain rate, the stretch ratios and the temperature /5/. PET material characteristics which are determined at temperatures close to the process and at strain rates close to the process with maximum stretch ratio are required.
When stretching PET, strength and stiffness increase with increasing extension. This effect, that depends on the stretch ratio, is known as strain hardening. This is due to the molecular structure of polymer materials. These consist of linear or branched molecular chains, which are aligned with increasing deformation. The orientation leads to an increase in strength and stiffness. The strain rate also has an influence on the stiffness of the material. At low deformation rates, the molecular chains can follow the load and the chains slip off one another. With increasing deformation rates, however, the individual chains can no longer follow the deformation, which leads to an increase in stiffness with a simultaneous decrease in total deformation /1/. The strain hardening and the influence of the deformation rate on the mechanical material behaviour can be seen in the stress-strain diagram in Figure 1. Typical measuring methods allow strain rates up to about 5 and strain rates up to 3,200 %/s. Currently, simulations of the stretch blow moulding process can only use material data determined at these strain rates and stretch ratios. Data for higher degrees of stretching and strain rates at temperatures close to the process are rarely available, as the acquisition of these data is very resource intensive.
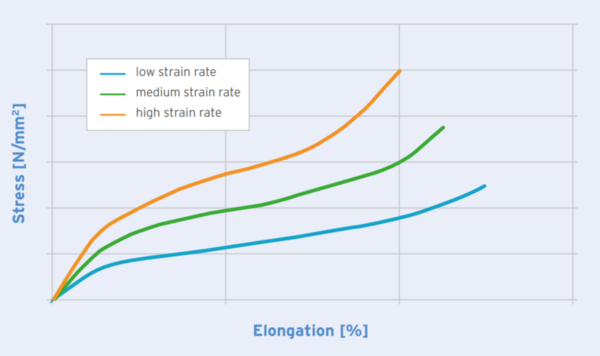
Material data acquisition
A well calibrated material model is the key to accurate simulation. To determine this material data, a measuring method is required that allows the material to be strained at different deformation rates, at different temperatures and until material failure occurs. In addition, the strain must be recorded as a function of time. Due to the stretching behaviour typical of the stretch blow moulding process, the material must also undergo biaxial stretching /6/. Therefore, uniaxial tensile tests are unsuitable.
The company Brückner Maschinenbau GmbH, Siegsdorf (Germany), and the research group Tan et. al. at Queen’s University Belfast, Belfast (Northern Ireland), each developed stretching systems based on the stretching frame principle. In these processes, flat, tempered plastic samples are stretched in two orthogonal axes /7/. A disadvantage of these methods is limited maximum elongation of 500 %, so that the film sample cannot be stretched to failure at high temperatures. In addition, the clamping of the sample leads to necking during stretching and the film is not completely isothermal. The strain rate is also limited to a maximum of 3,200 %/s with this measuring method /8/.
Another measuring technique is represented by the Bubble-Inflation Rheometer (BIR) and the MembraneInflation Rheometer (MIR) developed at the Institute for Plastics Processing (IKV). In both systems, circular, temperature controlled, flat samples are inflated through a medium /9, 10/. Due to the geometric conditions of the BIR measurement, a cubic increase of the bubble volume with time is required for a constant strain rate. Therefore, the maximum strain rate is limited to less than 100 %/s. This is remedied by the MIR, a further development of the BIR. As shown in Figure 2, the sample is inflated on a guiding grid, so that the required volume increase is reduced. In addition, a defined thin spot is created in the pole.
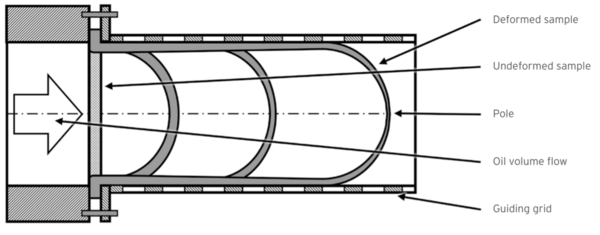
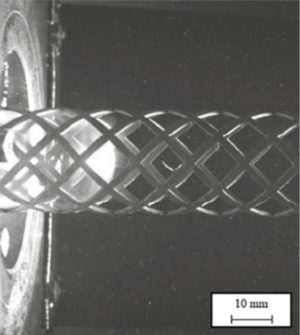
The MIR allows a precise analysis of the deformation behaviour and finally also the failure behaviour of a film in an isothermal environment, at temperatures and strain rates that can be adjusted over a wide range. The structure is shown schematically in Figure 3. The main components of the MIR are a pressure tank and a cylinder between which a circular film is clamped. Both pressure tank and cylinder are filled with temperature-controlled silicone oil. During the measurement, a piston in the cylinder moves in the direction of the sample. This forces the oil towards the sample and causes the sample to be inflated. In order to guarantee a uniform deformation, the sample is deformed along a guiding grid. This creates a defined thin point in the pole.
Due to the large installation space of the pressure tank, the MIR enables high elongation, so that samples can be stretched until failure. In addition, strain rates of 10 %/s up to 10,000 %/s can be achieved by using a powerful electric motor for piston propulsion. The process of deformation is recorded by highspeed cameras to locate the point of failure and to calculate the stretch ratio and the stress at the time of failure. The strain rate is dependent on the piston speed and therefore cannot be directly adjusted. However, the strain rate can be controlled approximately by using a reverse engineering approach.
The images are captured orthogonal to the sample film. The samples are marked for evaluation of the strain state. The mark displacements resulting from the deformation of the sample are successively digitally evaluated for each camera image. Thus, the strain state as a function of time is determined. In order to calculate the stress states in the sample film, the pressure difference between both sides of the sample is also recorded and then synchronised with the strain measurements. That way, a stress-strain curve can be generated at high strain rates and in an isothermal environment.
Figure 4 shows images of the testing process at a strain rate of 1,000 %/s. The measurement until failure takes only fractions of a second, depending on the strain rate.

A further advantage of the MIR is the determination of the type of failure behaviour, because it is possible not only to analyse failure by crack formation, but also to consider failure by stress whitening. This type of failure is very significant in the industry, as plastic containers with signs of whitening are already considered to be rejects. In order to prevent stress whitening, it is state of the art to dimension the plastic containers to the safe side. This means that the material potential cannot be fully utilised.
Evaluation and interpretation of the results
Based on the extensional measurements of a PET film, type Ramapet R180, Indorama (Thailand) produced with the MIR, the following test results are described as examples. The film thickness was 1070 µm. The piston speed was set to provide strain rates between 100 %/s and 10,000 %/s. The temperature is kept constant at 100 °C. The stretch ratio and the pressure difference at the point of failure were measured, and the stresses in the film sample were determined from these measurements. Each experiment was repeated three times. The samples were tested in the MIR until they burst, whereas the evaluation of the image and measurement data was carried out until the appearance of stress whitening. This moment can be determined very well on the basis of the high-speed images.
Figure 5 shows the stretch ratio at the moment of failure as a function of the strain rate. The highest degree of stretching of 4.8 is achieved at the lowest strain rate of about 100%/s. With increasing strain rate, the stretch ratio decreases, because with increasing deformation rate, it becomes harder for the polymer chains to follow the deformation and failure of the amorphous matrix between the crystalline oriented regions occurs. A low strain rate therefore leads to a higher orientation and later failure.
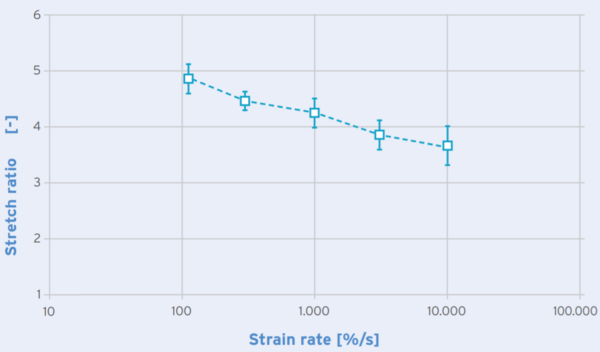
For the preform processor, this means that the processing speed (and with that, the strain rate) must be reduced if the stretch ratio of the formed plastic container is in the critical range.
The increase in stress with increasing strain rate in the test specimen was already shown in Figure 1. This is not the case for the stress at the moment of failure. The stress curve in Figure 6 shows that the stress decreases with increasing strain rate. One reason for this behaviour is the lower degree of stretching at this point in time, which leads to a less pronounced orientation and correspondingly lower stress. Furthermore, the material data on which Figure 1 is based are only available up to a stretch ratio of 3. The stress-strain behaviour of PET at higher degrees of stretching and higher strain rates has been mostly unknown up to now, due to the disadvantages of the stretching frames.
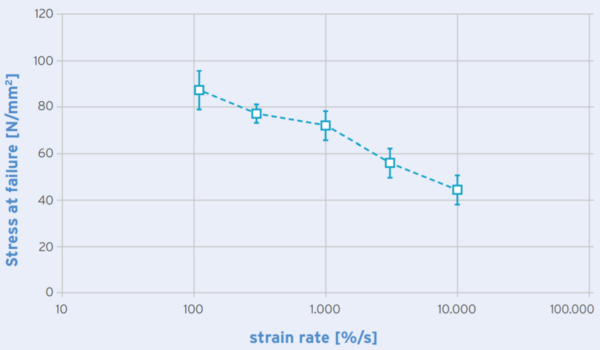
Summary and Outlook
In order to enable the development of packaging products with ever thinner walls and reduced material consumption in the stretch blow moulding process, it is necessary to extend the established simulation approaches by a failure model. Only with an accurate prediction of the extensional deformation behaviour it will be possible to utilise the maximum material potential of PET in the production of highly stretched plastic containers. The basis for a conclusive simulation is a material model for the highly stretched state. The MembraneInflation Rheometer allows the stressstrain behaviour of PET to be determined at temperatures and strain rates close to the process and at maximum stretching degrees. In addition, the detection of stress whitening is possible.
The obtained measurement results indicate that higher degrees of stretching can be achieved with a reduced deformation speed. In addition, this effect can be used to reduce the reject rate due to material failure in already running processes.
In further work, the complete stressstrain curves as a function of strain rate and forming temperature are determined. With the determined data a failure criterion is developed and integrated into the simulation of the twostage stretch blow moulding process. For the first time it is now possible to predict the occurrence of stress whitening in a simulation.
Acknowledgment
The research project (20258 N) of the Forschungsvereinigung Kunststoffverarbeitung has been sponsored as part of the “Industrielle Gemeinschaftsforschung und -entwicklung (IGF)” by the German Bundesministerium für Wirtschaft und Energie (BMWi) due to an enactment of the German Bundestag through the AiF. We would like to extend our thanks to all organisations mentioned.
_____________________________________________________
/1 / THIELEN, M.; HARTWIG, K.; GUST, P.: Blasformen von Kunststoff-Hohlkörpern. München, Wien: Carl Hanser Verlag, 2019
/2 / WELLE, F.: Polyethylenterephthalat (PET). Kunststoffe 104 (2014) 10, pp. 74-76
/3 / FORSTHÖVEL, J.: Polyethylenterephthalat (PET). neue verpackung 9 (2009) 1, S. 42-44 /4 / NIXON, J.; MENARY, G. H.; & YAN, S.: Finite element simulations of stretch-blow moulding with experimental validation over a broad process window. International Journal of Material Forming 10 (2016) 5, pp. 793-809
/5 / JABARIN, S.A.: Orientation Studies of Poly(Ethylene Terephthalate). Polymer Engineering & Science 24 (1984) 5, pp. 376
/6 / MARTIN, P. J.; TAN, C. W.; TSHAI, K. Y.; MCCOOL, R.; MENARY, G.; ARMSTRONG, C. G.; HARKIN-JONES, E. M. A.: Biaxial Characterisation of Materials for Thermofor¬ming and Blow Moulding. Plastics, Rubber and Composites 34 (2005) 5-6, pp. 276-282
/7 / THIBAULT, F.; MALO, A.; LANCTOT, B.; DIRADDO, R.: Preform Shape and Operating Condition Optimization for the Stretch Blow Molding Process. Polymer Engineering and Science 47 (2007) 3, pp. 289-301
/8 / MENARY, G. H.; TAN, C. W.; HARKIN-JONES, E. M. A.; ARMSTRONG, C. G.; MARTIN, P. J.: Biaxial deformation and experimental study of PET at conditions applicable to stretch blow molding. Polymer Engineering & Science 52 (2011) 3, pp. 671-688
/9 / MICHAELI, W.; HARTWIG, K.: Biaxiale Dehnrheometrie. Kunststoffe 96 (1996), pp. 85-88 /10 / HABERSTROH, E.; DETROIS, C.: MembraneInflation Rheometry – A New Way of Measuring Biaxial Deformation Behaviour at Process-Relevant Conditions. Proceedings of the Annual Technical Conference (ANTEC) of the Society of Plastic Engineers (SPE), New York, 1999
/11 / DETROIS, C.: Untersuchungen zur Dehnrheologie und Verarbeitbarkeit von Halbzeugen beim Thermoformen sowie Simulation und Optimierung der Umformphase. RWTH Aachen, Dissertation, 2001
The comPETence center provides your organisation with a dynamic, cost effective way to promote your products and services.
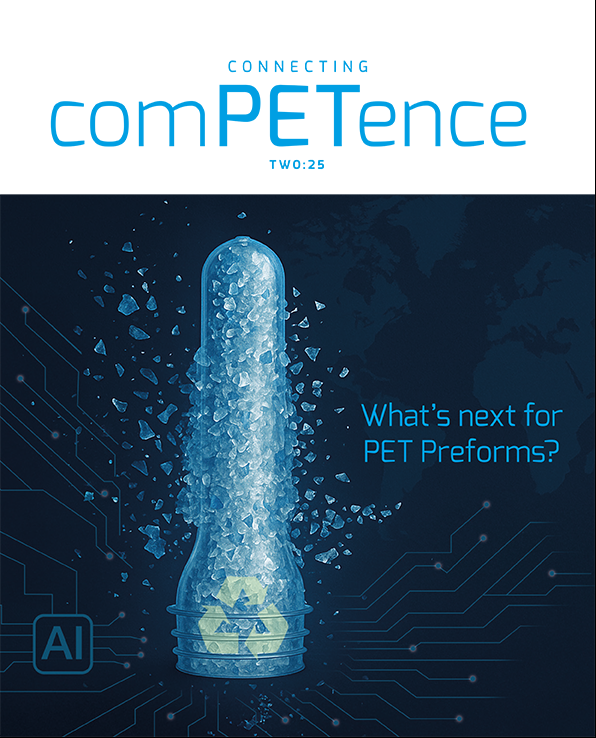
magazine
Find our premium articles, interviews, reports and more
in 3 issues in 2025.