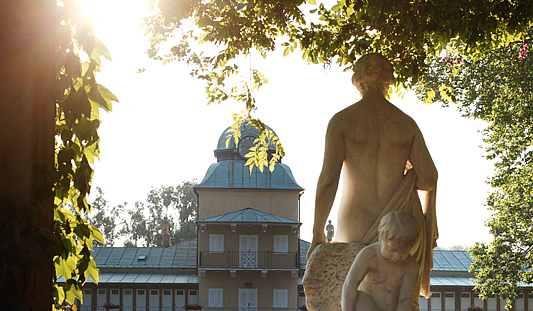
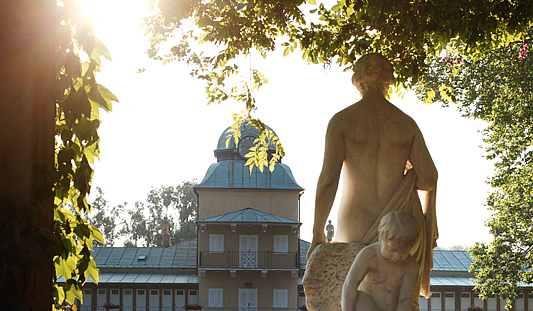
Photo credit: V?slauer Thermalbad GmbH
Teamwork and Respect — Sustainability at Vöslauer A company principle in action
PET Bottles, PET Recycling and rePET — Over 20 Years of Development
The Vöslauer production site in Lower Austria, not far from Vienna, is buzzing with activity. A steady stream of lorries enters the site while others leave at the same brisk pace.
We touched on this during our talk with Herbert Schlossnikl, Managing Director of the mineral water bottling company Vöslauer Mineralwasser GmbH, when we met him at his workplace in April 2019. Logistics and transport are two of many central points in Vöslauer Mineralwasser GmbH’s sustainability report. “At the moment, lorries are the most cost-effective solution for us. But one of our sustainability goals is to transition from road to rail. We currently transport about 30% of our goods by train. We want to significantly increase that percentage.”
Core values
Sustainability has traditionally been an important value at Vöslauer. The company has published eight sustainability reports since 2008 — comprehensive documents covering the company, its products and its water source /1/. One whole chapter is dedicated to packaging and recycling, while another is titled “Number 1 in climate protection”. Other core values are gender equality and equal opportunity employment, work-life balance, diversity, and health and safety for all employees — “a culture of respect”, as it was described in the most recent report published in 2017. The company takes its responsibility to the local region seriously, including both its source and the surrounding area. Compliance is an inherent part of the company’s ethics, and Vöslauer takes a comprehensive approach to raising awareness of sustainability among staff, suppliers and customers alike.
The occasion for our visit is the recent introduction of bottles made from 100% recycled PET. We already knew that Vöslauer was a trailblazer for PET within the filling industry, and that it was one of the first businesses to start working on processing and recycling used PET. We’ve also seen similar initiatives from other companies. In particular, many manufacturers have recently announced efforts to step up the use of recyclate in the interests of sustainability and the environment. But there are still complaints that processing recycled PET causes problems in bottle production and filling; the debate surrounding recycled PET for drinks bottles is (still) a heated one. We’re interested in the specific path that PET and its recyclate follow at Vöslauer Mineralwasser GmbH, a regional business, compared with the big multinationals.
Herbert Schlossnikl, Managing Director of Vöslauer Mineralwasser GmbH, isn’t the type to complain. He comes across as forward-looking and optimistic, a typical engineer focused on finding solutions. In his years as Director of Engineering, he worked closely with beverage packaging technology. It was back then that we got to know each other personally, and still today he speaks fondly of his time gathering information and inspiration for technological developments at the PETnology Conferences.
Pioneering circular thinking
Schlossnikl says: “We introduced PET bottles for our products in 1996. At that time, refillable glass bottles were falling out of favour. Our options were a classic refillable glass bottle system like the one in Germany, or a deposit system with the plastic from single-use bottles being reused. Even back then, we firmly believed that if we opted for single-use, we would have to close the loop.”
The date is significant — while the concept of a loop is commonplace now, it didn’t yet play a major role back then. The PET recycling industry was for the most part still focused on the fibres and filaments business. The term ”bottle-to-bottle recycling” had not even been invented. But that’s exactly what Vöslauer was doing with PET: introducing the material into a loop. The first step was selling the Vöslauer PET bottle in a crate of nine, introduced in 2003. Over 95% of the bottles were returned to Vöslauer. According to Schlossnikl, they had a strong team that worked well together from the beginning, including the German company Texplast. He adds, “We owe a lot to Fritz Kehlert. It was under his leadership that Texplast processed the first Vöslauer bottles into regranulate. In the early days we already had over 1,000 tonnes of PET bales per year. That was quite something.” The company’s second partner was ALPLA: “Werner Rosenberger from the Steinabrückl facility was always particularly receptive and took on the challenge of reutilising our own used material for bottle production.” The conditions in those early days were very different. “There was no designated permit back then, so Vöslauer had to apply for a special one — and we got it. We started with a proportion of 30% recycled material, which we then increased to 50%. We’re now filling our first products into bottles made from 100% recycled material.” And this recycled material earned its own name at Vöslauer and with the company’s current partners: rePET. “We’re very strongly positioned in terms of logistics, which really boosts our efficiency. We source large quantities of recycled material from the Austrian collection system. The company PET to PET Recycling Österreich is located just 20 km away, and ALPLA’s PET production facility is also close by.”
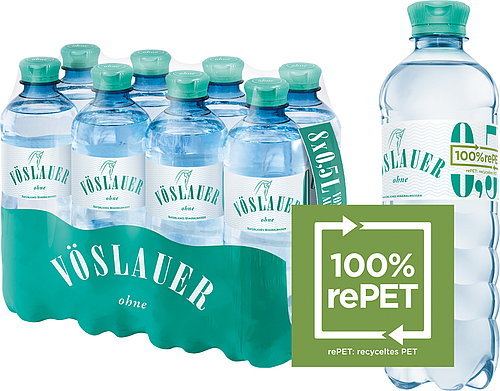
That is all to say that Vöslauer was a pioneer in PET recycling. Does the company also see itself as a leader in this field? “Yes, we communicate the good results of our circular work,” the engineer replies succinctly and almost modestly. The sustainability report and today’s corporate communication make it clear how much the company cares about demonstrating that efficient bottle production with a high proportion of rePET is possible — and moreover that it is not just feasible and worthwhile from an environmental point of view, but also in financial terms. The profitability of PET production is determined by the price ratio of recycled material to raw material. This is a drawback, says Schlossnikl: “It’s currently cheaper to buy in virgin resin than recyclate. But our approach was designed for consistency in the long term and isn’t affected by fluctuations in price. We can live with that.”
Vöslauer’s rePET

Schlossnikl goes on to describe the two different methods that Vöslauer uses to generate rePET. After shredding and washing, the feedstock material — known as washed flakes — is ready for further processing. There are two options for these washed flakes. The URRC process generates food-grade flakes, while the Starlinger technique produces regranulate. “Mixing the two — flakes and regranulate — has proven to be a solid approach. That’s what we’re using now to produce bottles out of up to 100% rePET.” Of course, the recycled material can cause problems, says Schlossnikl, but the production team deals with these masterfully thanks to their many years of rich experience. “The brand-new 100% rePET bottles do attract the odd complaint in the rare cases where a bottle makes it through the filling line to the consumer with a black speck. But most of these bottles never get that far, because they burst in the stretch-blow moulding machine or while they are preceded by CO2 pressurization in the filling process. We get about one complaint a month.” Listening to Schlossnikl, it becomes clear why there are so few complaints. After all, he did mention how experienced his staff are. Experience means low staff turnover, which in turn means a good working environment. And that ties in with another aspect of the sustainability report: employee welfare.
Lack of objectivity
The widespread negative image that plastic has gained is a concern for Schlossnikl, who says it has grown worse in recent years. While it was hotly debated in the past, he explains, there was always room for balanced, objective discussion, which he feels is now being lost. “ALPLA’s newly published life cycle assessment shows that single-use PET bottles and refillable glass bottles have about the same impact, with a slight advantage for PET. And that’s assuming 30 cycles for a glass bottle, which isn’t the case in practice. But that hasn’t stopped NGO representatives from claiming that this study, too, shows that glass is more sustainable — even while it was being presented. That goes to show how hard it is to stick to objective information. But we have to make that happen.”
Vöslauer has been working toward this goal for 10 years with its sustainability reports. The reports also give a great deal of prominence to the company’s carbon footprint and all its activities and efforts to reduce its emissions. The goal is clear: “We want to be a carbon-neutral business by 2025.” Where production is concerned, the sustainability report is based on the concept of the recycling economy. The process of transitioning to 100% rePET bottles for the company’s own brands by 2025 has already begun. And, of course, Vöslauer’s dedication to sustainability doesn’t stop at packaging. The company’s aim is for everything that is developed, consumed or produced to be made from 100% recycled material by 2025. That includes all materials and products used in-house. On a technical level, Vöslauer is currently looking at the other plastic materials used for bottles. By 2025, it aims to make all films and labels from 100% recycled material, too.
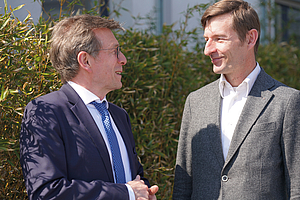
Dealing with developments
We’re interested to know how the company sees the EU initiative on tethered caps. Schlossnikl says: “I think we felt the same as many others in the industry. We couldn’t understand the logic behind the decision. Tethered caps are counterproductive in terms of material usage. The feedback we’ve heard from the collection systems is that most bottles come back together with their cap. In the recycling process, it’s easy to separate PET from PP using the sink-float method. But what’s done is done and we have to look to the future.” The custom Vöslauer caps will pose a particular challenge. Even under the new regulations, there’s no question of introducing standard caps. Schlossnikl is optimistic, and after our conversation with him we wouldn’t have expected anything else. “This example shows that new regulations always trigger a process of innovation at the same time.”
We also talk about other modern technologies that could be used. For example, direct printing for bottles and caps — is that something that Vöslauer would consider for its bottles? “Even assuming there were failsafe ways to prevent the colour agents from migrating into the beverage and contaminating it, the fact remains that bottles which have undergone direct printing have a lower recovery rate in the recycling process, since a lot of the shredded flakes will be coloured. My personal opinion is that direct printing is counterproductive in terms of recyclability,” says Schlossnikl.
Or, for instance, chemical or biological recycling. It’s the sustainability aspects that make Schlossnikl sceptical: “To be frank, I find it hard to believe that these recycling methods could offer a better energy balance than the closedloop material cycle that we’ve already established with PET to PET and ALPLA.”
As open-minded as he is, Schlossnikl’s scepticism is founded on trust in the established system. But if sophisticated new approaches to PET and PET recycling were introduced that corresponded with Vöslauer’s philosophy of sustainability, then the company would certainly be open to change, he says. The engineer remains true to himself: solution-oriented with the environment in mind.
The facility is still bustling as we leave. The whole of Austria is supplied from this site, with exports being sent out to Hungary and Germany. And that increasingly by rrail — for the sake of sustainability.
_______________
/1/ Vöslauer’s sustainability reports are based on the Global Reporting Initiative (GRI) guidelines. Specific key figures and indicators are used in accordance with these guidelines. This enables simple comparison of sustainability reports and business activities.
/2/ Vöslauer-Partner für PET-Recycling: PET to PET, ARA, ALPLA
- PET to PET Recycling Österreich GmbH is a member of the groups Coca-Cola HBC Austria, Radlberger Getränke, Rauch Fruchtsäfte, Spitz and Vöslauer Mineralwasser, and describes itself in its own terms as the only PET recycling facility serving the drinks industry in Austria. It took up operation in August 2007 and recycled more than one billion PET bottles in 2018, corresponding to a total material weight of 24,500 tonnes. This represents an increase of 9% over 2017.
- ARA was founded in 1993 as a packaging collection and recycling system and is now a driving force within the Austrian recycling economy thanks to its expertise in the field.
- ALPLA is a leading international manufacturer of packaging systems, bottles and caps. The family-run business uses state-of-the-art technology and innovative solutions to produce rePET preforms, which Vöslauer then reprocesses into bottles.
The comPETence center provides your organisation with a dynamic, cost effective way to promote your products and services.
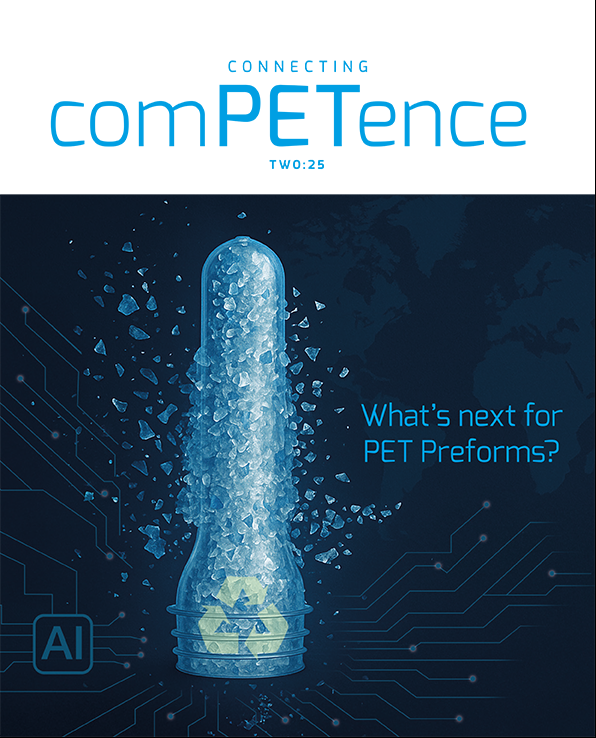
magazine
Find our premium articles, interviews, reports and more
in 3 issues in 2025.