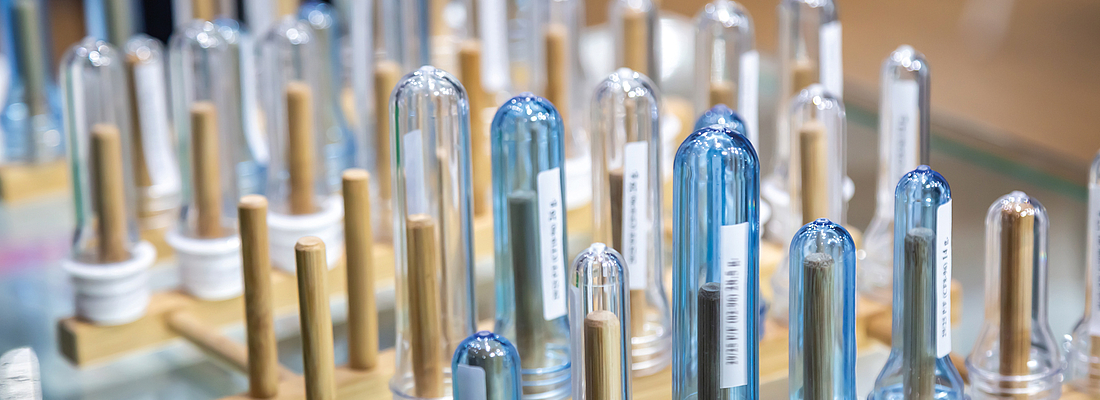
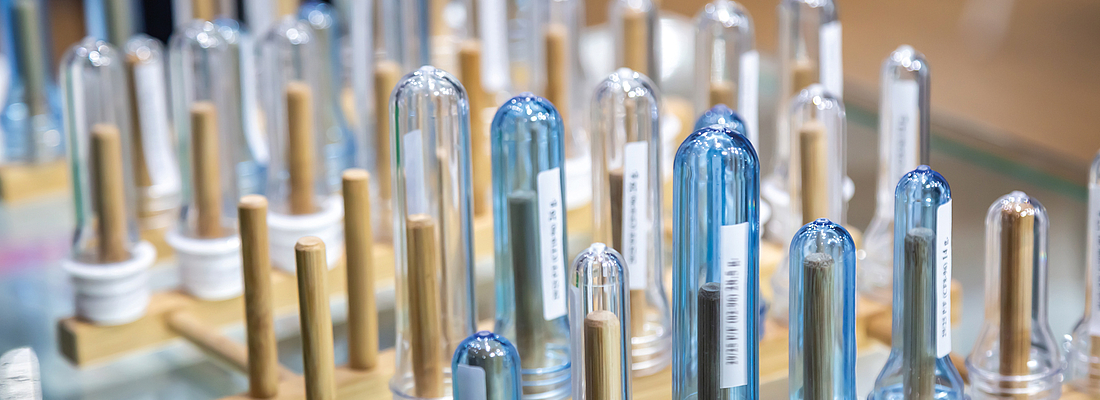
Photo credit: Shutterstock
comPETence magazine | ONE:22 | Barrier
PEF as a barrier layer: does it influence the bottle blowing process?
The stretching behavior of PET is well known at converters and brand-owners, leading to stable blowing operations, even for complex bottle designs. The addition of a barrier layer can have a significant effect on the overall preform stretching behavior and consequently on the processability into the bottle shape.
The processing window will be influenced by the quantity and location of the barrier layer, but importantly also by the barrier material that is used. In this article the stretching behavior of a major incumbent barrier material will be compared with a new barrier material that will enter the market in 2024: Polyethylene furanoate or PEF. Produced by Avantium Renewable Polymers, PEF is a polyester made from renewable resources and has outstanding gas barrier properties. It is therefore very suitable as a barrier layer in PET-based multilayer bottles. Using the INDICATE machine from Blow Moulding Technologies this article investigates the stretching behavior of barrier preforms during the blowing process. It concludes that the influence of a PEF barrier layer on the blowing behavior of the preform into a bottle is even lower than that of an incumbent barrier solution. This confirms observations from blowing trials with PEF-containing PET multilayer preforms on pilot lines and gives confidence on the processability and application of PEF as a barrier layer in industrial bottle blowing equipment.
Barrier requirements in rigid packaging
PET is the material of choice for beverage packaging due to its ideal combination of performance, design freedom, ease of processing and excellent recyclability. However, when it comes to the gas barrier, limitations of PET are quickly reached when it comes to sensitive food and drink products or products that face long logistic timelines. In these cases PET alone is not enough to guarantee sufficient shelf life and an additional barrier is introduced in the form of an inorganic plasma coating; an active oxygen scavenger; or a passive barrier layer. Plasma coatings are effective but offer limited flexibility in bottle design and require very high initial investment costs, while active scavengers are easy to incorporate into PET but impact recyclability. Active scavengers can also only be used as a barrier for oxygen, necessitating an (additional) passive layer when a barrier for CO2 is required. Therefore, in this article we focus on a passive barrier layer as the middle layer of a PET based multilayer (MLY) bottle. In the current market the primary materials for such a layer are (semiaromatic) polyamides, which provide an excellent barrier against O2 and especially CO2. Polyamide (PA) has poor compatibility with the polyester PET, resulting in easy delamination of the barrier layer and haze formation when blended. Recycling of such multilayer bottles therefore relies on thorough separation of the polyamide layer after shredding and washing.
The influence of a PEF barrier layer on the blowing behavior of the preform into a bottle is lower than that of an incumbent barrier solution.
PEF as a barrier layer in PET bottles
Avantium recently published an article in comPETence detailing the possibilities of using PEF as an alternative gas barrier layer in PET bottles and the potential advantages it has over incumbent technologies /1/. In this article the technical feasibility of producing PET/PEF/PET multilayer preforms was shown, as well as the possibility of blowing these preforms into bottles with the same dimensions and weight distribution as bottles made from mono-material PET preforms. All of this could be done in conventional multilayer preform coinjection molding machinery and bottle blowing equipment using settings similar to those used for PET without a barrier layer.
What has not been reported yet is the effect that the barrier layer has on the blowing behavior of the bottle during the stretch blow molding process. The present article aims to give insights into and quantify the influence of a PEF barrier layer on the stretching behavior of a preform into a bottle. A comparison will be made with a plain monolayer PET preform and a multilayer PET preform containing a polyamide layer.
Experimental
The INDICATE free stretch blow molding device of Blow Moulding Technologies /2/ was used to investigate the effects of a barrier layer on process is recorded with two high-speed cameras. In this way image correlation can be employed to determine the out of plane corrected strain of the preform/balloon as a function of time. With the combination of all sensor data the (local) stressstrain behavior can calculated for the material in realistic bottle (pre-)blowing conditions.
Three preform types were investigated, all produced by Husky on their HPP5 Multi-Layer System:
- Monolayer PET preform without a barrier layer
- Multilayer PET preform containing a PA barrier layer
- Multilayer PET preform containing a PEF barrier layer
For preform 2 a barrier layer of 6 wt% polyamide was used, which is a common amount in commercial products to achieve bottles with sufficient barrier properties. The bottle blowing process of such preforms is known to be achievable from countless use cases and therefor provides an excellent benchmark.
For preform 3 a core-biased barrier layer of 10 wt% PEF will give barrier properties comparable to PA layer in preform 2, and the main results are shown using this preform. Preforms with a either a 10 wt% PEF center-biased barrier layer or a 5 wt% PEF core-biased barrier layer were also investigated and will be briefly discussed to show the influence of barrier material amount and layer positioning.
The preforms were all heated to 115 °C in the oil bath and had an outer temperature of 105 °C at the start of the stretch blow molding. The settings used for the stretch blow molding were as follows: 6 bar line pressure; 150 ms blow duration; 1.0 m/s stretch rod speed.
Results
As mentioned earlier, the full blowing process was recorded using a high-speed camera, and Figure 1 shows what the balloons originating from the three preforms look like during the blowing process, from left to right 45 ms, 55 ms, 75 ms, 90 ms and 150 ms after process initiation. The color indicates the local strain in the hoop direction.
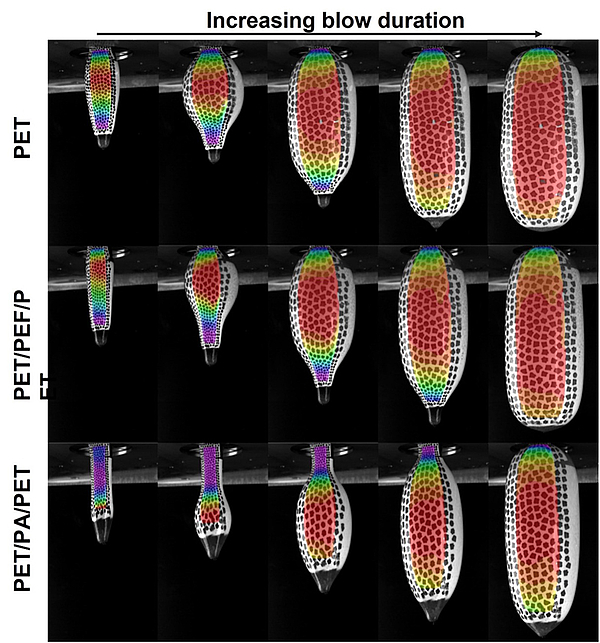
What is immediately obvious from the comparison in Figure 1 is the shape of the final balloon after 150 ms of blowing. The shape and volume of the PET reference and the PET/PEF/PET multilayer balloon are comparable, while the balloon with a PA barrier layer is significantly narrower. The reason behind this is the stiffness of the barrier materials: PEF has a higher modulus than PET at room temperature (3.6 GPa compared to 2.2 GPa) and a glass transition temperature (Tg) that is 10 °C higher, meaning the temperature gap between Tg and stretching temperature is significantly smaller /3/. The Tg of the polyamide resin used is comparable to that of PET, but the modulus at room temperature is significantly higher (4.7 GPa) and is known to not drop as much as PET (and PEF) above Tg /4/. The higher stiffness of especially the polyamide barrier layer prevents the balloon from stretching as far as the monolayer PET when using the same pressure. Apart from the end result, the development of the preform shape during blowing is visibly distinct for the multilayer preforms. The first expansion in the hoop direction for the monolayer PET preform takes place starting from the middle of the preform. However, the hoop expansion when a PEF layer is present starts nearer the preform neck, while the polyamide layer causes the preform to start expanding from the base of the preform. For all preforms the preform base is the last part to fully stretch, and the stiffness of the polyamide layer is high enough that it prevents the bottom of the PA multilayer balloon from completely stretching in the hoop direction using these settings. The stretching evolution will influence weight distribution along the preform length in the final bottle, and explains why settings need to be tweaked for multilayer bottle blowing specifically to optimize base weight.
In order to look at more than visual data, Figure 2 shows the true stress versus local nominal strain in the hoop direction of a point in the middle of the preform during the whole blowing duration. The increased stiffness of the multilayer preforms is apparent from the increased slope of the stressstrain curve following the trend in stiffness: PET monolayer < PET/PEF/PET multilayer < PET/PA/ PET multilayer. At a nominal strain of 2.8, the slope of the PET monolayer stress-strain curve abruptly changes. This strain value is known as the Natural Draw Ratio (NDR) and indicates the start of strain-induced crystallization. It has previously been established that the NDR of PEF is higher than that of PET, and that the stress increase after NDR is quicker for PEF than for PET /5/. Figure 2 shows that this trend is visible even with only 10% of the preform consisting of PEF, with the NDR for the PEF multilayer bottle appearing at a strain of 3.2. Finally, the total strain and thus the total expansion for the PEF multilayer balloon is the same as for a PET monolayer, while it is smaller for a balloon containing a polyamide layer.
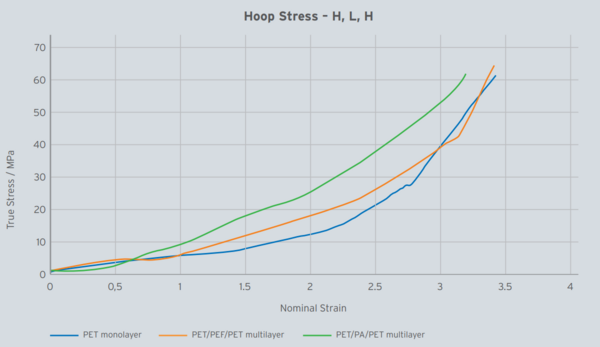
It is worth noting that the positioning of the barrier layer in the PET/PEF/PET multilayer preforms is optimized for maximum barrier improvement. That is to say, the PEF layer is located very close to the core of the preform and therefore stretch ratios are higher than if the layer was located in the center of the preform wall. This positioning leads to the highest strain-induced crystallinity in the barrier layer and thus a better barrier performance, while also having the most influence on the stretching characteristics /1/. Changing to more center biasing of the PEF barrier layer or decreasing the thickness of the barrier layer will bring the stretching behavior closer to that of the monolayer PET preform as can be seen in Figure 3. Such adjustments in layer positioning and amount will come at the cost of a decrease in barrier properties.
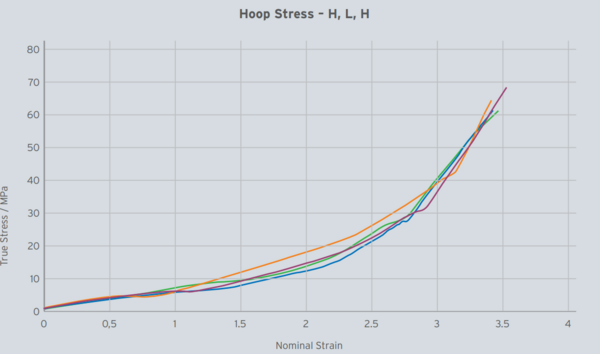
Adjusting the stretching behavior
As mentioned before, it is possible to blow PET/ PEF/PET multilayer bottles using the same process conditions as for a monolayer PET preform /1/. However, the progression of the balloon during the blowing process is influenced by the presence of a barrier layer and consequently changes need to be made for optimization of the weight distribution of the resulting multilayer bottle. Adjustments are small enough that it is possible to do this during bottle blowing optimization, but using the abilities of the INDICATE the parameters that will have the biggest influence can also be predicted beforehand. By changing the preform temperature, blowing pressure, flow index, stretch rod speed, and pre-blow delay on the INDICATE equipment the processing window for multilayer PET/PEF preforms has been screened and quantified. These experimental results do not only give confidence of finding a robust commercial production process, but also give guidance on how to converge on the sweet spot during processing.
These experimental results do not only give confidence of finding a robust commercial production process, but also give guidance on how to converge on the sweet spot during processing.
Conclusion
In this article it was shown that the evolution of the bottle during the bottle blowing process is influenced by having a barrier layer in a PET preform. The bottle shape progression when using PEF as the barrier layer is only slightly altered, when compared to a preform containing the typical polyamide barrier layer, where the hoop expansion starts towards the base of the preform. This in turn influences the weight distribution of the resulting bottles. As there are many examples in practice where good multilayer bottles with a PA barrier layer are produced, these results show that it will also not be an issue to find a stable process for blowing PET/PEF multilayer bottles, confirming our findings from previous trials. The relatively minor differences, compared to PET monolayer, that the PEF barrier layer induces likely provide a broad operating window. Finally, using the INDICATE device allows a prediction of the adjustments that do have to be made and allows for better preparation before starting process optimization.
Acknowledgements
The support of Husky for the preform production and the know-how of co-injection is greatly appreciated. This work has been carried out under the PEFerence framework. The PEFerence project has received funding under Bio Based Industries Joint Undertaking under the European Union’s Horizon 2020 research and innovation programme under grant agreement No 744409.
_______________
/1/ Acquasanta et al., comPETence magazine, TWO:20, “PEF as a multilayer barrier technology: a sustainable way to enable long shelf life in PET bottles”
/2/ Yan et al., Mechanics of Materials (2017), 104, p. 93-106
/3/ De Jong et al., Polymers (2022), 14(5), 943
/4/ Vannini et al., J. Plastic Film & Sheeting (2020), 36 (1), p. 16-37
/5/ Van Berkel et al., Macromol. Mater. Eng. (2018), 303 (3), 1700507
_______________
Photos/Graphics: Avantium; Header: Shutterstock
The comPETence center provides your organisation with a dynamic, cost effective way to promote your products and services.
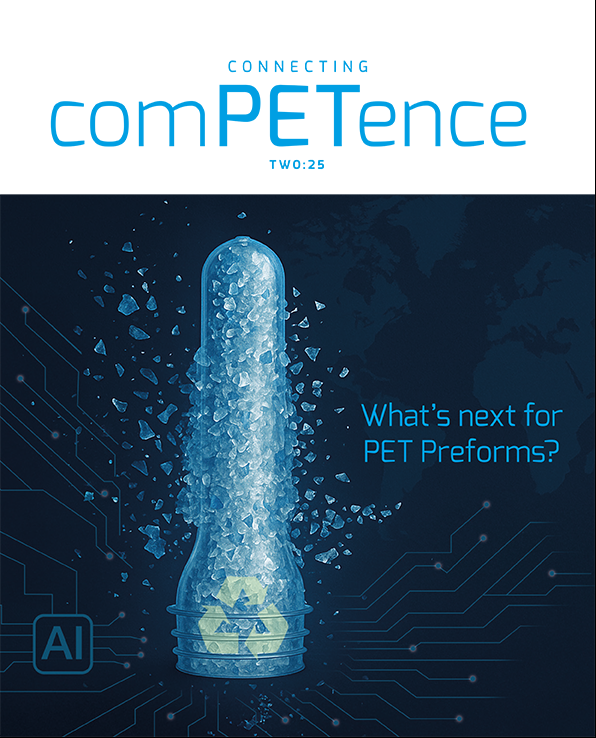
magazine
Find our premium articles, interviews, reports and more
in 3 issues in 2025.