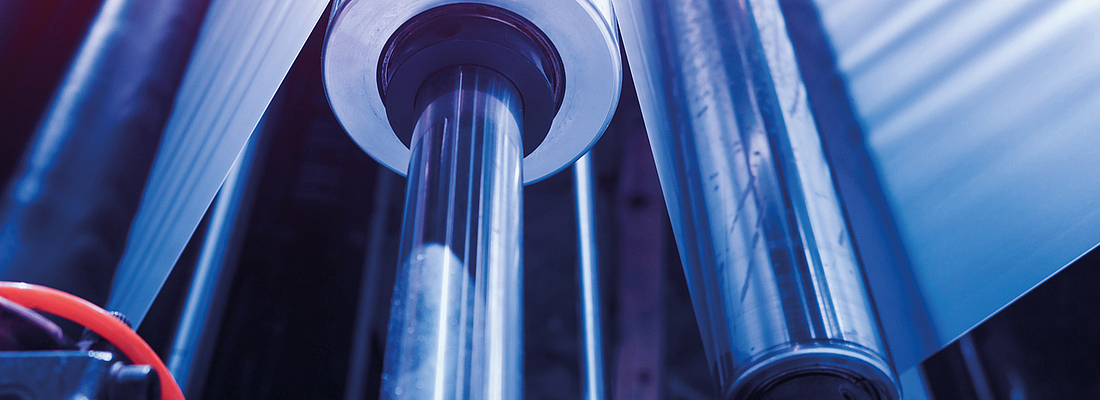
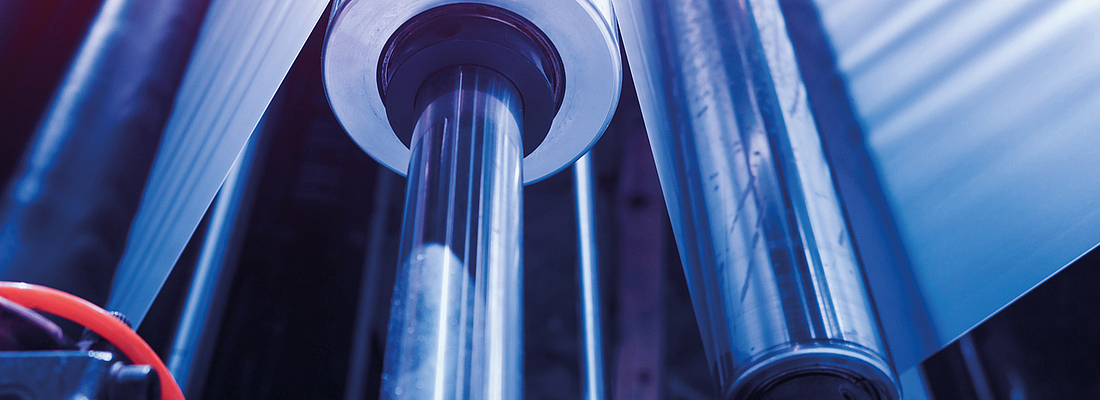
comPETence magazine | ONE:22 | Antiblock masterbatch for oriented PEF films
Partnership between Avantium and Sukano opens door for industrial application of PEF in flexible packaging
- PEF has proven to be a resin of high value and performance in barrier films for packaging applications
- Sukano and Avantium Renewable Polymers join efforts in the development of antiblock masterbatches for oriented PEF-film applications to overcome the winding and unwinding issues
- Combining Sukano’s expertise in slip antiblock masterbatches and Avantium’s knowledge on PEF is a natural step to open the road for industrial film production with PEF and beyond
The potential of the biobased polyester poly(ethylene 2,5-furandicaboxylate) (PEF) in rigid packaging solutions has received considerable attention in the recent years. PEF has a significantly improved gas barrier, while still maintaining the favorable properties such as good processability, transparency and mechanics, of its big brother PET. The combination of these enhanced performance characteristics with PEF’s surface properties, opens the possibility to develop flexible packaging solutions.
Sukano, a reputable expert in masterbatches and compouds, and Avantium, a pioneer in the emerging industry of renewable and sustainable chemistry, join efforts in the development of antiblock masterbatches for oriented PEF-film applications. With Sukano’s application know-how, coex-film-extrusion line and Karo tenter frame and Avantium’s knowledge on the physics and processing of PEF, it was a natural step to work together to innovate further and open the road for industrial film production with PEF.
PEF will come to market in 2024
Recently, Avantium Renewable Polymers has announced their decision to construct what is expected to become the worlds’ first purified FDCA plant at kilo ton scale /1/. This flagship plant should be mechanically complete by the end of 2023 and has a nameplate capacity of 5 kt/a. The purified FDCA will be supplied as is or converted into PEF with the addition of biobased mono-ethylene glycol (MEG) at Avantium’s polymerization tolling partner. Currently, already 50% of the plant capacity is granted with conditional off-take agreements, varying in both geography (EU, US and Japan) and applications. Next to rigid packaging applications, PEF will be applied in flexible applications by specialty polyester film producer Terphane, who has signed off for a part of the capacity of the flagship plant. Furthermore, Avantium has developed biaxially oriented PEF film prototypes together with Toyobo in Japan /2/, /3/.
PEF’s value proposition in film
For packaging in general, the outstanding barrier performance of PEF has attracted quite some interest. With a ~10x higher oxygen barrier, ~15x higher CO2 and ~2.5x higher water vapor barrier, PEF can replace incompatible raw materials typically used today for the above-mentioned barrier properties, offering a monomaterial packaging solution, including barriers for several multilayer packaging applications. The fact that the barrier performance of PEF is unaffected by humidity is a distinct advantage over incumbent barrier materials such as EVOH and polyamide barrier resins.
The fact that the barrier performance of PEF is unaffected by humidity is a distinct advantage over incumbent barrier materials such as EVOH and polyamide barrier resins.
For flexible film applications, the optical, thermal, mechanical and surface properties of PEF are on par with, or even an improvement upon, PET. This offers potential advantages in downstream processing, like improved printability and improvement of final performance in the end product.
With the need to move toward circularity and sustainability, there is a strong market demand for food grade recycled PET (rPET) resins, and this is causing challenges on the supply side. Whereas PET bottles are commonly used as feedstock for food grade rPET granules, the second largest potential feedstock, PET trays, currently face technological challenges to be applied as feedstock for additional rPET offers. As a result, there has been a drive to create monomaterial polyester packaging, reducing the contamination of the PET recycling stream by non-polyesters compatible materials, which are typically used in up to 2/3 of the PET trays available in the market. By technically enabling the replacement of such contaminants with materials from within the polyester family, such as PEF, the market can potentially increase PET recycling yields and final rPET quality available in the market for further material loops.
Although fully polyester packaging solutions do exist, these have limitations with respect to barrier performance. Here PEF can play a decisive role: its barrier allows the creation of a monomaterial polyester, a high barrier packaging solution which can either be recycled on its own (in case of a mono PEF solution) or will keep the quality of the resulting rPET high by significantly reducing the contamination of the PET tray stream with polymers from a different family that are commonly used for barrier or sealing. For example: in the case where a multilayer PET/PEF high barrier lidding film is connected to a PET tray, any remnants of the lidding film on the tray entering the recycling stream will not affect the rPET quality to the same extend, as lidding films containing barrier materials such as EVOH and PVDC will do. Additionally, the ability to produce PEF resin grades compliant with food contact application regulations opens the road to develop a closed loop tray to tray recycling stream.
Replicating the success of modifying PET for roll-to-roll production
In the production process of flexible films, the semi-finished products are typically stored on rolls. Without any surface modification, this can lead to challenges in winding/unwinding, due to welding of layers. A common approach to resolve this issue is to include inert additives in the surface layer that modify the friction in between layers. There are multiple ways of adding these fillers to the film: in the polymerization step, via a concentrated masterbatch or via compounding. The masterbatch approach offers the most flexibility, while also providing the option to tailor the performance and functionality to specific applications or customers’ demands, with respect to varying the concentration and combination of different types of fillers. At the same time, the masterbatch will reduce the amount of resin that has undergone two melt processing steps.
For this specific project, Sukano developed a masterbatch with the aim of offering a coarse surface roughness that facilitates fast winding operations. Additionally, Sukano R&D specialists also designed another masterbatch grade with the focus of offering low haze levels for optically sensitive applications.
Sukano’s expertise in slip-antiblock masterbatches
PET penetration in the market has only been highly increased with the availability of tailored masterbatches, which help solve winding and unwinding issues faced by biaxially oriented PET films in commercial lines and several other applications such as extrusion sheets of all sorts of thicknesses. Sukano was at the forefront of this story as the PET additive specialist pioneered the market reference highly concentrated PET based slip antiblock masterbatches.
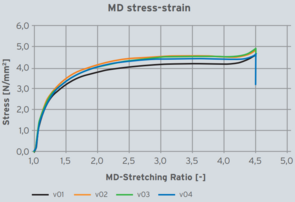
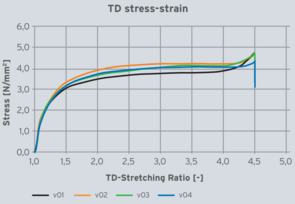
Sukano was at the forefront of this story as the PET additive specialist pioneered the market reference highly concentrated PET based slip antiblock masterbatches.
With the change in the past 30 years of the historical production process technology of oriented PET-films (OPET) to a process allowing dosing of concentrated masterbatches to twin screw extrusion technology without the need to pre-dry the polymer, Sukano developed antiblock masterbatches to be dosed at typically 0.5% to 1.5% levels to external coex-layers offering a highly efficient production of OPET films. These antiblock masterbatches were tuned over the years, offering the desired surface roughness for fast winding operations or transparency for applications requiring low haze levels for best optical performance.
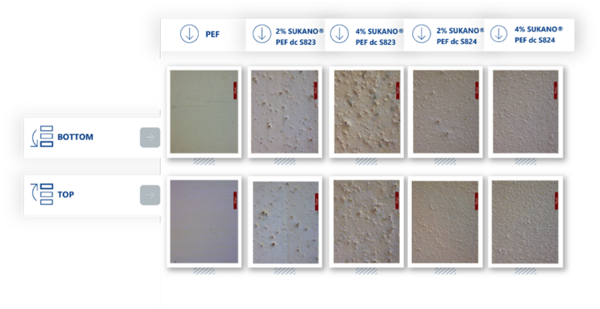
Test conditions for film casting
Sukano and Avantium conducted comprehensive lab trials in Sukano’s in-house R&D laboratory with the availability of a coex-filmextrusion line and a Karo tenter, producing biaxially oriented PEF films for packaging applications.
For this specific project, Sukano developed a masterbatch with the aim of offering a coarse surface roughness that facilitates fast winding operations.
The PEF used both as the carrier of the masterbatch and base resin of the film production has an IV of 0.89 dL/g. The films were cast on a co-extrusion film line in an ABC setup with A and C being 15 wt% layers where the masterbatch was added and the B middle PEF layer of 70 wt% without any fillers. The film was cast at a width of 300 mm on a chill roll, trimmed to a width of 210 mm and targeted at a thickness of 450 µm. Both type of masterbatches were added at two dosing levels: 2 and 4 wt% and a reference film without any additives was produced, adding up to a total of 5 cast film samples.
Biaxial film stretching
Each cast film sample was subjected to biaxial stretching in a Brückner Karo VI batch tenter stretching device. The stretching was conducted on a film sample preheated to 110 °C in 60 seconds, stretched at a rate of 150 %/s in equibiaxial stretching mode and subsequently annealed for 10 seconds at 200 °C. The stretching curves indicate the onset of strain hardening to occur just after reaching a biaxial stretch ratio of 4.5x4.5.
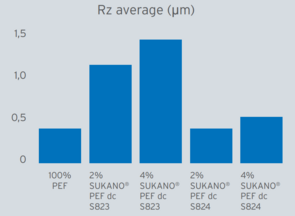
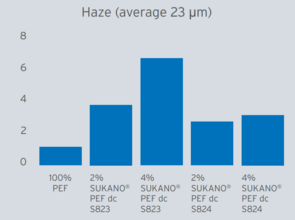
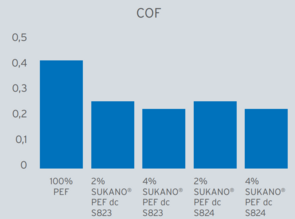
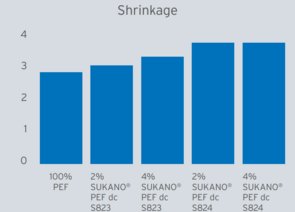
Resulting film properties
The resulting films were analyzed on haze, coefficient of friction and shrinkage values. Figure 2 shows images of the surface with an optical microscope. The differences between the two types of filler applied as well as the influence of the let down ratio can be clearly observed.
SUKANO® PEF dc S823 results in a rougher surface, which makes it suitable for high-speed film production, whereas SUKANO® PEF dc S824 resulted in films with reduced haze.
This is also demonstrated in the data presented in the graphs above. The haze levels of the SUKANO® PEF dc S824 based films are significantly lower than the films produced with SUKANO® PEF dc S823. The fact that the coefficient of friction of the films that contain the antiblock filler do not significantly differ indicates that there is room to reduce the LDR allowing a further reduction of haze.
The shrinkage at 150 °C was measured on films that were stretched up to 3.5x3.5. Even without optimization of the stretching and annealing conditions a fairly low amount of shrinkage was obtained.
Further, it was noticed that even though the stretching up to 3.5x3.5 did not result in strain hardening, significant melt peak was observed for the annealed films, which is in line with the observation in an earlier study on the stretching behavior of PEF that PEF already forms strain induced crystals before the strain hardening becomes apparent /4/. These crystals are expected to further boost barrier and are responsible for the low shrinkage values observed.
Conclusions
The collaborative development work has resulted in two prototype masterbatches capable of providing antiblock performance of the surface of biaxially oriented PEF film. Both developed antiblock masterbatches offer a significant friction reduction without interfering with the performance of the stretched films. The availability of antiblock masterbatches opens the possibility to further develop PEF and PEF-based films at (pre) industrial scale equipment.
Acknowledgements
This work has partially been carried out under the PEFerence framework. The PEFerence project has received funding under Bio Based Industries Joint Undertaking under the European Union’s Horizon 2020 research and innovation program under grant agreement No 744409.
_______________
/1/ Avantium takes a positive Final Investment Decision on the construction of its FDCA Flagship Plant,” 9 December 2021. [Online]. Available: www.avantium.com.
/2/ Inagaki, J.; Numata, Y.; van Berkel, J.G. “Polyester film” 2017, WO2017169553.
/3/ Inagaki, J.; Ito, K.; Shimizu, T.; Gyobu, S.; Morishige. C.; van Berkel, J.G. “Polyester film containing furandicarboxylic acid”, 2017, WO2017038092.
/4/ E. Forestier, C. Combeaud, N. Guigo, N. Sbirrazzuoli, and N. Billon, “Understanding of strain-induced crystallization developments scenarios for polyesters: Comparison of poly(ethylene furanoate), PEF, and poly(ethylene terephthalate), PET,” Polymer, vol. 203, p. 122755, Aug. 2020, doi: 10.1016/j.polymer.2020.122755.
_______________
Photos, graphics: Avantium/Sukano
The comPETence center provides your organisation with a dynamic, cost effective way to promote your products and services.
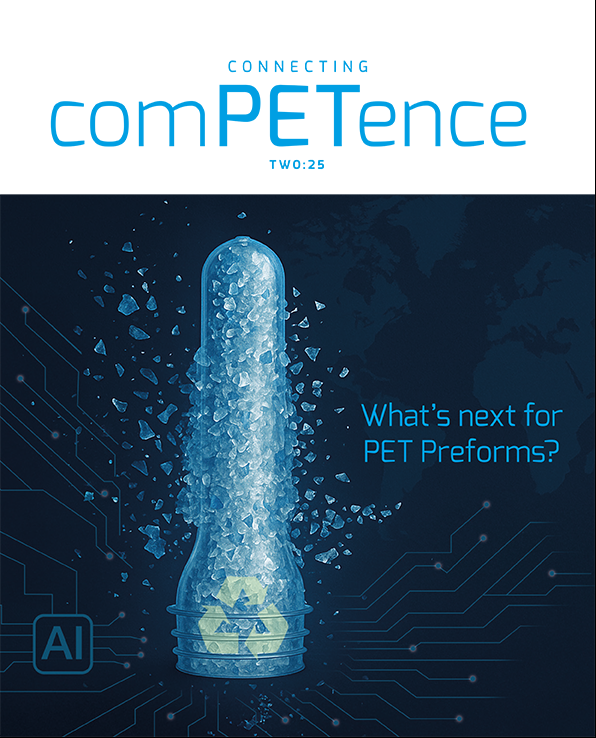
magazine
Find our premium articles, interviews, reports and more
in 3 issues in 2025.