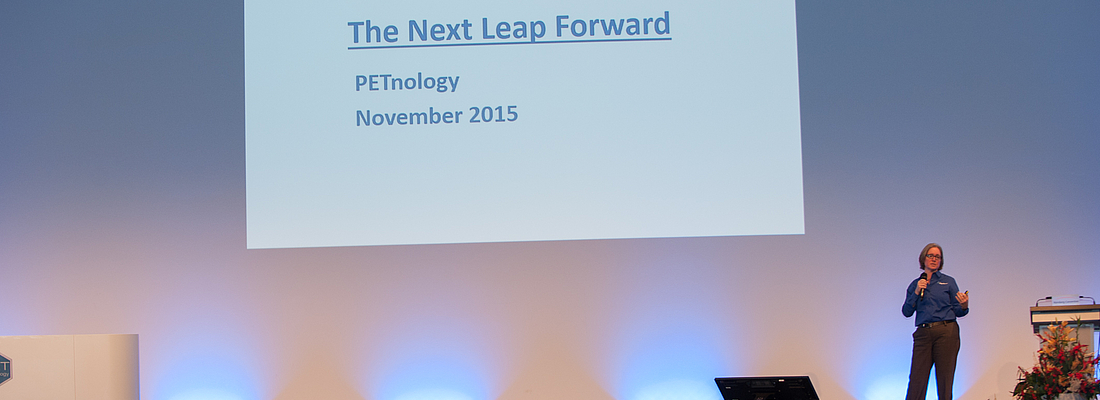
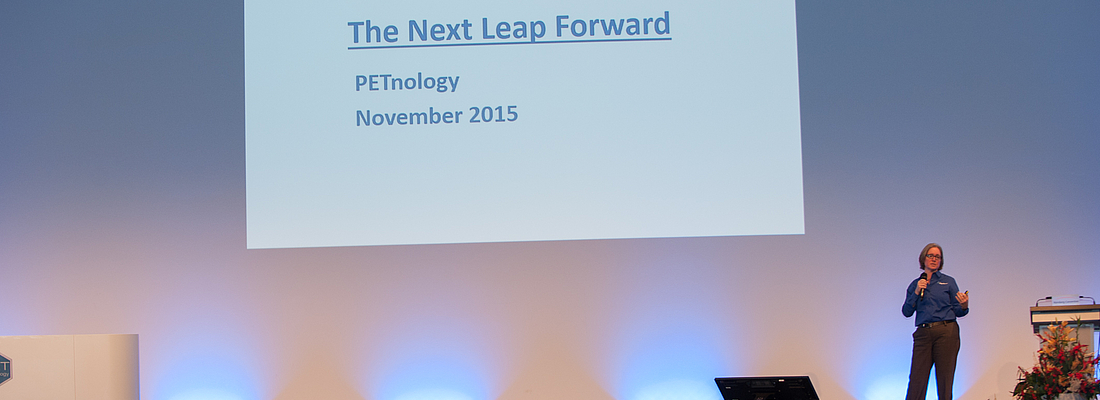
One step, one machine, one operation – this is how Ann O’Hara, President of the LiquiForm Group, Saline, MI, USA, describes the novel, one-step production process which forms preforms into containers with the liquid consumable product instead of with compressed air.
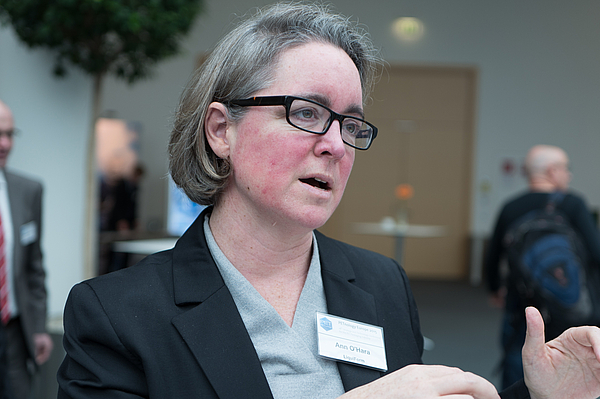
“We are seeing broad interest in the LiquiFormTM process which we first presented in detail at last year’s PETnology,” beams Ann O‘Hara. And she is expecting the first commercial machine to be installed in another year’s time. The main advantages of the new process is the simplicity and the associated reduced footprint, thanks to the fact that just one machine is needed instead of three (air compressor, stretch-blow moulding machine and filling line), and importantly, the resulting energy consumption and other elements of cost savings also associated with the simplicity of one machine not three.
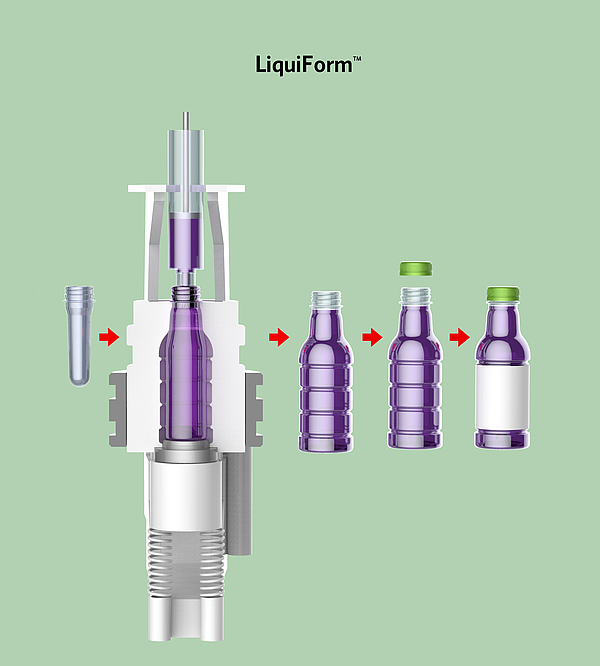
The LiquiForm Group is a joint venture between the packaging specialist Amcor and the blow moulding machinery manufacturer Sidel. The Group has also signed agreements with and IP contributions from Japan’s largest plastic bottle manufacturer, Yoshino Kogyosho, and bottled water brand owner, Nestlé Waters. After representatives of the LiquiForm Group initially presented the new process at last year’s PETnology Conference, this year they reported on the latest practical tests and results. “We spent last year extensively testing bottles produced in this single step process and are thrilled with the excellent results,” says O’Hara. On top of the simplicity advantages that a single step machine entails, LiquiFormTM also boasts superior “bottle engraved elements”. The company’s president explains: “Liquid is a more efficient pressure source and delivers more consistent pressure than air pressure because liquid flows down and then out versus air which seeks the least resistance in the preform by finding minor temperature or resin quality variations, and in particularly hot spots, in the heated preform which changes dynamically as the preform is stretched into a container.” As a result, the wall thickness distribution of LiquiFormTM bottles is much more even than that of conventionally produced bottles. Also, the new process can be used to make even thinner walls. Ann O’Hara cited weight reduction of between 13 and 21% in their current trials, emphasizing: “The results so far are examples of what can be achieved, but they are not the limit or the end of the line. We are sure that further optimization is possible.” One of the key parameters tested was top load, which came out around 20% superior to a bottle formed using compressed air and filled an capped separately. Another advantage, according to Ann O’Hara, is the shorter process cycle time and the resulting cost advantage offered by the LiquiFormTM process. “Actual LiquiForm fill/form tac-time ranges from 0.15 to 0.4 s depending on container size and application, and now, the cycle time will be determined by the machine designs ability to make use of this improvement in speed.” And LiquiFormTM is also able to produce sharper bottle definition and engraved elements.
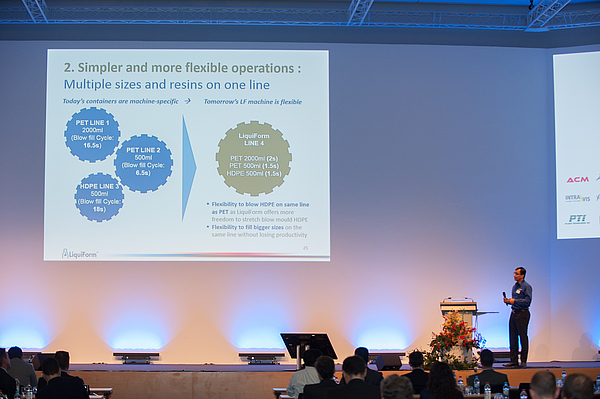
According to O’Hara, all of these benefits make compelling arguments for the new technology. And there’s more: “LiquiFormTM is not just much more flexible with respect to bottle sizes and shapes compared with conventional stretch blow moulding machines, but can also be used for polyolefin containers, as well as PET. This should be attractive to bottle producers and end users, as it means just one machine is needed for a variety of bottle sizes and materials. LiquiFormTM is available under licence, and O’Hara is convinced that it won’t be long until the first bottles produced with this process will be on the market. Her vision for the future: Customers press a button at the supermarket to get the bottle shape of their choice, produced on demand.
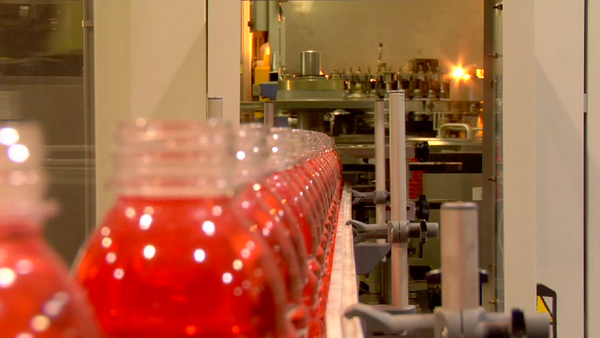
The comPETence center provides your organisation with a dynamic, cost effective way to promote your products and services.
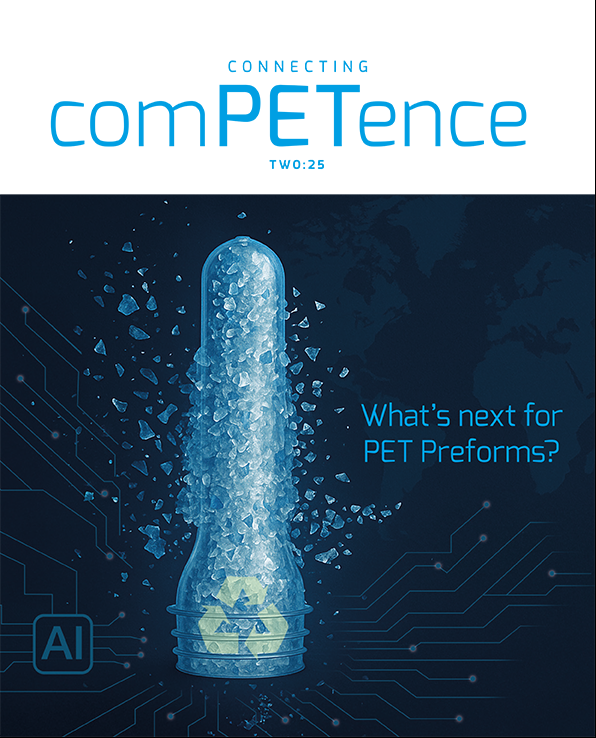
magazine
Find our premium articles, interviews, reports and more
in 3 issues in 2025.