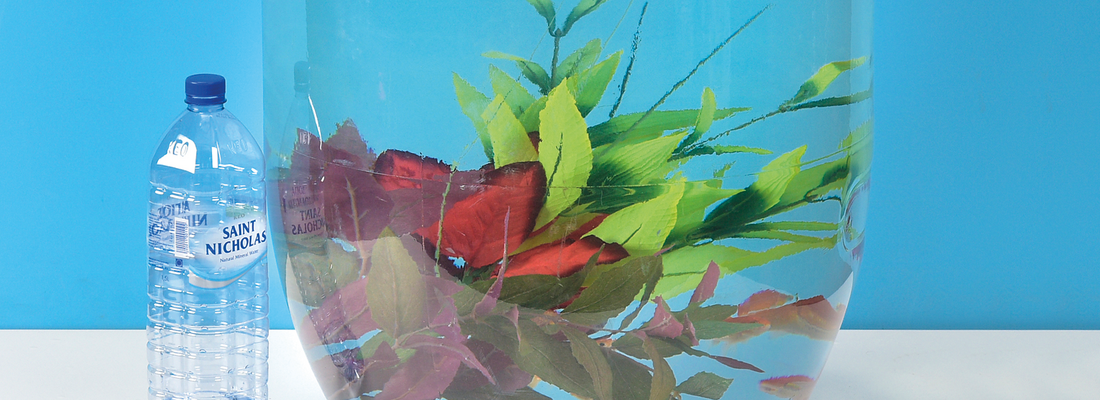
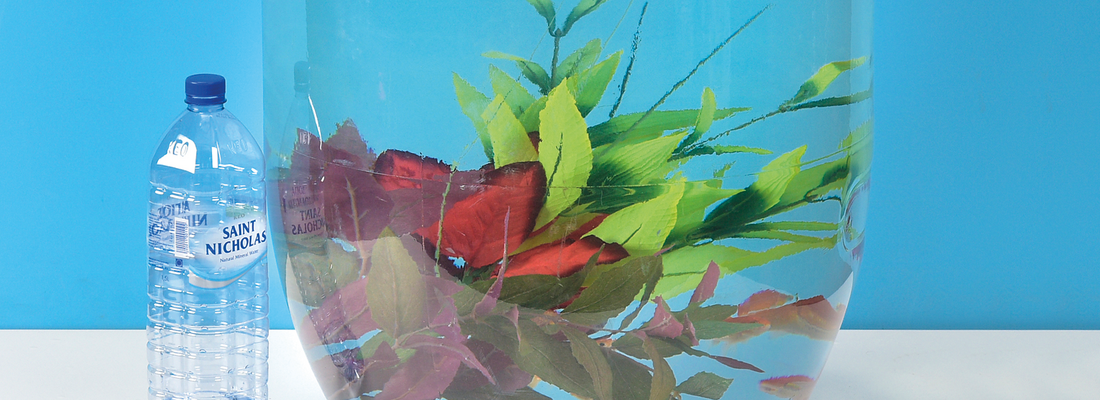
(Source: CYPET Technologies)
LARGE PET CONTAINERS
Large PET Containers - CYPET TECHNOLOGIES new production system for very large PET containers (1,000 Litres)
CYPET Technologies LTD is a European manufacturer of innovative single-stage Injection Stretch Blow-Moulding (ISBM) systems, that transform PET resin directly into finished containers such as bottles, jars, jerrycans, drums and pressurized containers. CYPET serves its global customer base on all five continents from its headquarters based in Nicosia, Cyprus, with additional offices and manufacturing facilities in Ahmedabad, India.
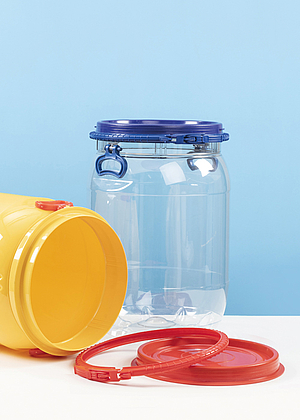
Stretching the limits - LARGER CYPET MACHINE MODEL
CYPET has pushed the boundaries of PET processing from 30 litres (previously the maximum available) to 120 litres. This has been achieved using one of CYPET’s standard machine models.
The next natural step in extending the size of container that CYPET machines can produce was the popular 200 litre drum size. Using its unique technology and expertise in the production of large PET containers, CYPET has developed a new larger machine model to extend its range of machines for the production of 200 litre drums in 2 cavities (2 drums per production cycle).
This larger machine model has been designed to be able to produce much larger containers with a capacity of up to 1,000 litres in a single cavity (1 container per production cycle). This revolutionary development, which started with 200-litre drums, paves the way for the production of several types of even larger PET containers, allowing PET to enter new market segments. Examples of such containers are
- Water storage tanks of up to 1,000 litres, replacing rotomoulded or blow-moulded polyethylene tanks.
- 1,000 litre IBCs, replacing blow-moulded HDPE IBCs for both new IBCs and reconditioned used IBCs.
- PET liners for returnable (foldable/nestable) rigid packaging up to 1,000 litres, suitable for liquid packaging.
For all of the above applications, there are significant weight savings when using PET, resulting in major cost benefits as well as very significant sustainability benefits.
Water storage tanks
In countries where the water supply to homes is intermittent, there is a need for water storage to provide water when the water supply is interrupted. This creates a very large market for such water tanks in countries such as India, Mexico, many Latin American countries and countries in Asia and Africa. Typical sizes are 500, 750 and 1000 litres.
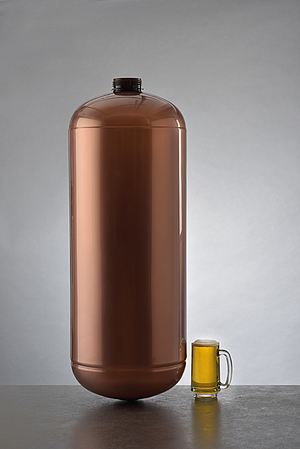
Historically, water storage tanks were made from fibreglass. Several decades ago, fibreglass tanks were replaced by polyethylene plastic tanks produced by rotational moulding. In recent years, blow-moulded polyethylene tanks have partially replaced rotomoulded tanks due to weight and energy savings as well as higher production output.
Water storage tanks are usually located on the roof of a house and are therefore exposed to the sun for many years. This exposure results in two important characteristics that water tanks must have in order to function properly:
- Block light: If even a small amount of light enters through the walls of the tank, algae will grow in the water, which is unacceptable. Therefore, the water tank must completely block out light. Rotomoulded and blow-moulded water tanks achieve this either by using a black coloured tank or by using two or more layers of material so that one layer is black and blocks the light and another layer is a different colour on the outside. For PET water storage tanks, light blocking must be achieved through the colour of the tank. For countries where black is not an acceptable colour, CYPET has developed a special off-white colour masterbatch that can be used with PET to achieve a complete light block and is also suitable for food contact. This is shown by the light transmission measurement below:
- UV stability: The special masterbatch that imparts light-blocking properties to PET tanks also contains UV stabiliser to ensure that the PET tank is UV stable for at least 15 years of continuous exposure to equatorial sunlight. Rotomoulded and blow-moulded polyethylene water tanks also achieve UV stability through the use of UV stabiliser additives.
In addition to the two key requirements above, water storage tanks must have the following additional characteristics:
- Sufficient mechanical strength to withstand the logistics of transport and installation and to support the weight of water when full. ¡ A wide top opening to allow access for future maintenance.
- A way for connecting pipes for water inlet and outlet.
- A way of preventing the installed water tank from moving in strong winds when empty.
- In some countries, nestable tanks with a conical shape are used to save transport costs.
CYPET’s PET water tanks meet all these requirements, despite the significantly lower weight of PET tanks compared to polyethylene tanks.
Typical weights for 1,000 litre water tanks:
- Rotomoulded tank 25 kg
- Blow moulded tank 17 kg
- ISBM CYPET tank 9.5 kg
The much lighter weight of PET water tanks has many advantages:
- Much lower raw material costs
- Much less energy required for raw material production
- Much less energy to produce the tank
- Much smaller carbon footprint - much more sustainable
- Lower transportation costs
With all of the above benefits, PET water tanks can disrupt the water tank market by offering a new, more economical and sustainable solution to the market.
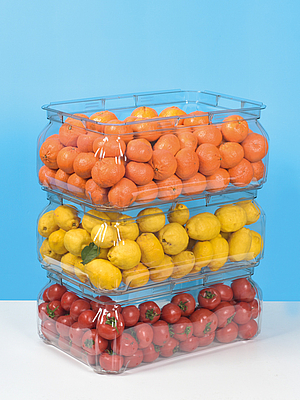
PET IBC bottles (1,000 L)
IBC bottles are currently made from HDPE by blow moulding. There was no technology available to produce the 1,000 litre IBC bottles from a different plastic material until CYPET Technologies developed its larger machine model.
An Intermediate Bulk Container (IBC) consists of a plastic container (inner bottle) surrounded by a protective metal cage and mounted on a pallet. The container has a lid for filling and a valve nozzle for dispensing material, while the pallet allows convenient handling with a forklift. IBCs can be securely stacked for storage and transport. Since their introduction in the mid-1990s, IBCs have dominated the industrial packaging sector and continue to take market share from 200 litre drums for handling liquids and syrups in the chemical, food, pharmaceutical, paint, adhesive and waste water industries.
This is a result of the advantages that IBCs offer for industrial packaging:
- 25% more material can be stored per unit area than with cylindrical 200 litre drums, resulting in reduced storage and transport resources and costs.
- More efficient logistics due to faster handling times and efficiencies by filling, moving, loading, transporting and dispensing a single container compared to 5 drums.
- IBCs are a more sustainable form of packaging because their durable construction makes them refurbishable, reusable and recyclable. They make a significant contribution to the move towards sustainability
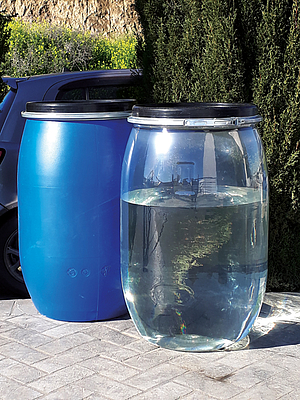
Converting an IBC bottle from the HDPE bottles currently used to PET bottles will result in a 5kg weight reduction, from around 14kg for HDPE bottles to just 9kg for PET bottles. This has significant sustainability and economic benefits that are expected to disrupt the IBC market.
- LESS PLASTIC: The 35% lighter PET bottle has the potential to reduce the amount of plastic used in IBCs by 150,000 tonnes per year.
- LESS ENERGY (& CO2): Less energy is required to produce and transport the bottles, reducing carbon emissions.
- LESS WATER & CHEMICALS: Low-cost PET bottles would make re-bottling used IBCs more attractive than washing them, eliminating the use of water and cleaning chemicals.
- CIRCULAR ECONOMY: PET bottles can be 100% recycled and reused to make new bottles or other PET containers.
- TRANSPARENCY: Unlike HDPE bottles, PET bottles can be produced with glass transparency, allowing the contents of the IBC to be visually inspected.
PET Liners for returnable (foldable/ nestable) rigid packaging to 1,000 L
CYPET’s new production system for very large PET containers is capable of producing lightweight rigid PET liners suitable for both foldable and nestable returnable bulk liquid packaging for sizes up to 1,000 L. Such rigid PET liners address all the weaknesses of flexible liners and offer a unique solution to the returnable bulk liquid packaging market. The weight of a 1000 litre PET liner for such applications can be as low as 3kg.
Foldable containers are inherently unsuitable for liquid packaging. However, when used in combination with a liner, they can be made suitable for liquids. There are flexible liners (bags) on the market, but they have several weaknesses:
- They have a multi-layer structure, which makes these bag liners non-recyclable, reducing the sustainability of foldable returnable packaging.
- They are very flexible, forming folds when the contents are emptied, which tends to retain some of the liquid contents, preventing complete emptying.
- They have very limited mechanical strength, with a high risk of being punctured through the openings of foldable packaging.
Nestable containers are usually designed without openings, making them suitable for liquids. However, because they are reusable, they would need to be thoroughly washed after each use or used with a liner. The first two weaknesses of liners listed above for foldable containers also apply to nestable containers.
The use of flexible liners (bags) is clearly undesirable in many returnable bulk liquid packaging applications without a viable liner alternative. This precludes the use of returnable packaging for many liquid packaging applications, forcing fillers to use non-returnable packaging (drums or IBCs). This denies these fillers the opportunity to use the more environmentally friendly returnable packaging solution.
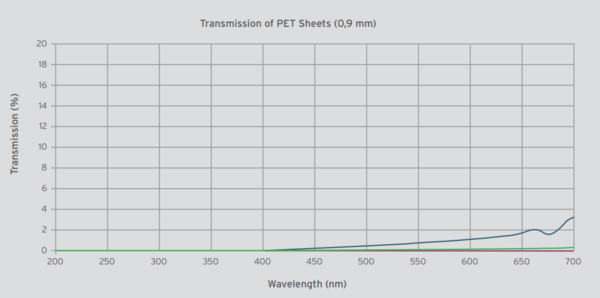
The first system is under construction
CYPET’s new production system is a single stage system using CYPET’s patented process where both the injection mould and the blow mould are mounted on the same clamping unit and open and close together. Both preform injection moulding and container stretch blow moulding are performed on the same machine, resulting in a system that starts with PET resin and ends with the finished container.
To cope with the challenging cubic shape of IBC bottles, CYPET has combined its expertise in preform design for large square containers with the incorporation of a special preform temperature profiling station into the large container machine, which is capable of adjusting the preform temperature in a 3-dimensional way. This capability allows the preform temperature to be adjusted in three dimensions:
- Along preform length
- Around the circumference of the preform
- At specific locations on the preform
These are the result of processing experience combined with injection moulding and stretch blow moulding simulations.
The resulting process is fully automatic and consists of
- Injection moulding of a preform
- Opening of the moulds and the following transfers: - Removal of the stretch blow moulded container from the blow mould. - Placement of the preform from the previous cycle into the blowing mould. - Transfer of the injected preform to the temperature profiling station.
- Moulds close for the next preform injection cycle, during which - The previously heated preform is stretch blow moulded into the container. - The previously injected preform is tempered in 3 steps
The first CYPET machine for 1000 litre PET containers is currently in production for a customer in Asia, including moulds for both water tanks and IBC bottles. First production trials are expected in Q3.
Conclusions
CYPET’s new production system for very large PET containers is revolutionary for the PET industry and confirms CYPET’s commitment to its vision of adding value through innovation. It opens up new horizons for PET processing and new ways of using PET for more applications in the packaging, storage and transportation of goods.
PET has been the material of choice for retail rigid packaging for many years, and in the recent past it entered the commercial packaging market. With CYPET’s unique capabilities for the production of PET jerrycans and drums, PET has recently started claiming part of the industrial packaging market by replacing HDPE containers.
The new CYPET production system enables PET to extend its reach even further, for applications of up to 1,000 L capacity, opening new markets for bulk packing and water storage. This revolutionary production method, combined with PET’s unique properties (mechanical strength, easy recyclability, transparency, smooth and glossy surface, etc) provides opportunities for very cost effective and sustainable solutions for very large containers.
The areas of application outlined above (200 L Open Mouth Drums, Water Tanks, IBC Bottles, and Liners for Returnable Liquid Bulk Packaging), illustrate the flexibility of CYPET’s new system, with the capability of producing a variety of containers for various applications on the same machine, by changing moulds. These areas of application are characterized by large volumes and can provide viable projects for this new CYPET system. However, they are not the only possibilities, as other applications can be investigated, to replace large products/containers, which are currently produced by rotational moulding or blow moulding.
The comPETence center provides your organisation with a dynamic, cost effective way to promote your products and services.
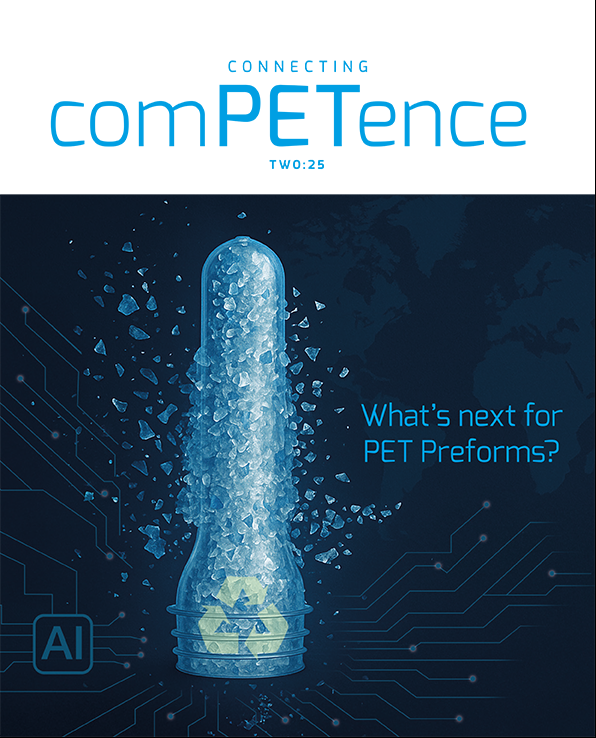
magazine
Find our premium articles, interviews, reports and more
in 3 issues in 2025.