

The newly patented non-invasive method for measuring nitrogen in a closed PET bottle!
1: Purpose of nitrogen in packaged beverages
Nitrogen is currently used in the process of filling non-carbonated beverages into PET or glass bottles. This process, called inertisation, stabilizes the inert condition of the beverage within a closed container. Removing oxygen from the headspace extends the shelf life of the product by improving colour stability, while reducing oxidation and minimizing the loss of aroma and vitamins. This all comes together to create a germ-free atmosphere in a sealed package.
The material strength of PET bottles is constantly being reduced. Nonetheless, products are still expected to arrive undamaged, even if pallets of packaged product are being stacked higher in warehouses and shipping distances are increasing.
During the bottling process, a dosage of liquid nitrogen (Image 1) is added immediately after the filling of the liquid and before closure (fig. 2). The nitrogen evaporates immediately after sealing, creating the necessary internal pressure within the container (fig. 3).
Nitrogen is therefore the perfect medium, as it is available in liquid form and reaches 682 times its liquid volume after evaporating. Increased internal pressure makes PET bottles more durable and stiffer, and therefore more stable and stackable.
For this reason, it is extremely important to be able to measure whether the dosage of nitrogen has induced the necessary internal pressure in a PET bottle. Currently, the customary procedure measures pressure using a manometric device in an invasive procedure, which invariably leads to a significant loss of gas and therefore also pressure. This means it is impossible to assess the “true” pressure value. While various measuring instruments suppliers have endeavoured to provide easy-to-use, makeshift solutions, experience has shown time and again that the greatest impediment to accuracy is human interaction. Regular measuring often leads to erroneous measurements and a flawed interpretation of results. Furthermore, on-site devices are often defective and/or cumbersome to use.
Contact-free measuring instruments determine the bottle diameter before and after filling, and calculate the internal pressure in a PET bottle on the basis of material expansion. This process has not yet proven cost-effective in the laboratory, much less so in testing stations on the production line. Furthermore, it is difficult to calibrate the necessary attributes of the closure.
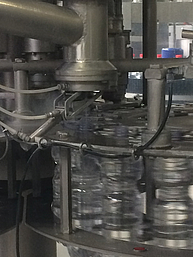
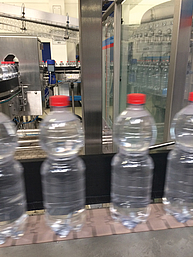
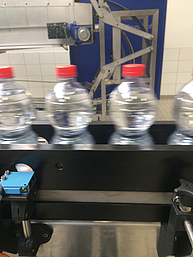
2: The solution: a patented non-invasive recognition of gas in the headspace through the LAB.N2-Process
Modern FT-Laser technology uses spectral detection in the headspace without piercing or damaging the PET bottle. Just as the LAB.CO can measure the CO2 contents in a closed container, the development engineers from ACM have designed a process to measure the nitrogen content in sealed beverage bottles using infrared technology (until now nitrogen (N2) has not been measurably detectable in the infrared spectrum). This newly patented process creates an observable form of N2 in a closed PET bottle with the help of an adjustable laser (FTL), where monochrome light is varied by adjusting the pump timing of the laser diode (fig. 4). The intensity of the irradiated laser probe is precisely analysed and used to calculate the concentration of gases in the headroom. The internal container pressure can then be determined.
Though similar applications have already been identified and applied in the area of FTL technology, various influential factors have led to high degrees of measurement uncertainty. These idiosyncrasies are taken into account in this newly patented process. The sophisticated Peltier effect precisely regulates the laser rays according to the often changing (material) circumstances. The amount of recycled material used in the production of PET is frequently increased, which changes the optical quality for technical measurements. The scratches and other imperfections on returnable PET bottles also affect the accuracy of signal evaluation. Developing an optical approach serves to eliminate the influence of these material imperfections or aberrations. The nitrogen pressure in a sealed beverage container can be precisely measured by combining laser technology, electrical process measuring and control technology, the development of a suitable electronic receptor, as well as the development of an optical axis (fig. 5)
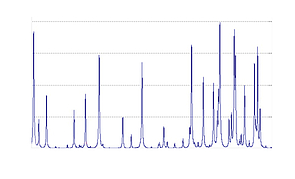
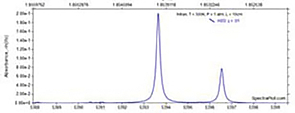
3: Optical Measurement Procedure
The following image illustrates the fundamental structure of the optical axis (fig. 6). Through a mechanical applicator developed specifically, a laser is directed through a bottle and toward a receptor module. As described in fig. 2, monochromatic laser rays are beamed through the headspace of the PET bottle, where a receptor evaluates the intensity of the rays after penetration. A stabilizing device developed by ACM uniformly fixes the PET bottles into position to ensure a consistent evaluation. Taking into account the physical principles of the Beer-Lambert law (or Beer’s law). This results in an optical table with the following fundamental structure.
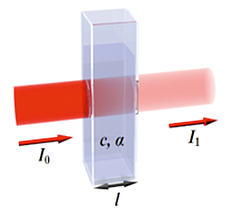
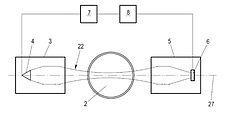
4. Construction of the LAB.N2 measuring device
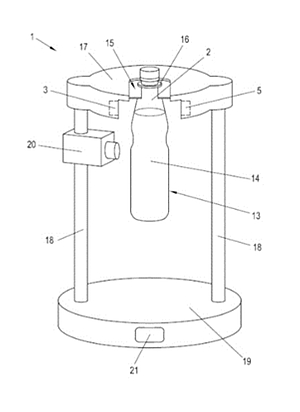
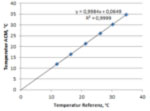
Installation location within the beverage industry, positive experience in recent years, as well as process observation and experience all play a significant role in assembling the measurement device. We began with the capabilities of the bottling employees and the requirement for a quick, simple, and accurate measuring procedure. A filled and sealed PET bottle is taken from the bottling line and “hung” in the LAB.N2 measuring device. After only a few seconds, a digital panel displays a measurement value, which is then confirmed after 8 to 10 seconds once the required internal measuring procedure has finished running. After this, bottles can be selected from the production line and measured as often as desired, taking just 10 seconds! This eliminates operator errors and reduces the number of employees assigned to the bottling line. For the first time, it is now possible to measure the same bottle multiple times in succession to confirm the consistency and reliability of measurement results. A diagram of the LAB.N2 device:
As the beverage bottle is not pierced, the temperature also has to be measured without compromising the bottle. An infrared pyrometer developed by ACM determines the external temperature of the bottle. This is then analysed with regard to the ambient air temperature using a comparison model, and the temperature of the bottle’s contents can subsequently be calculated. A thorough study between the temperatures of 0 and 30°C and various bottle materials guaranteed an accuracy of +/- 0.2°C. This temperature value is then used to determine a P20 compensation calculation of the nitrogen pressure. A positioning mechanism ensures that the temperature sensor is always pointed at the PET bottle and not optically obstructed by paper or other labels.
Fig. 9 shows a measurement procedure to determine the internal and detectable external temperature. This evaluation was conducted by an independent testing laboratory in an extremely thorough examination.
The base LAB.N2 device uses the most modern electronic data interfaces and is TCP/IP compliant. This ensures a direct connection to PC. Additional modules enable data to be transferred to iPads, mobile phones, etc. A built-in data display shows the results and all data in a clear, easy-to-read format. The complete measuring device operates from an independent power source or PC.
5: Measurement results of various PET bottles (all pressure specifications are in bar)
To illustrate the high reliability and reproducibility of results of the patented LAB.N2 measuring process, the repeatability of the measurement results must first be confirmed. To do this, PET bottles were purchased at retail and evaluated. Each bottle was repeatedly measured 5 to 10 times. It must be noted that to date, no other measuring process is able to reproduce the measurement procedure, as a bottle can only be pierced once to measure its internal pressure. This makes the LAB.N2 measuring procedure truly unique, as the bottle is neither pierced nor otherwise damaged, so the measurement procedure can be performed twice on the same bottle. To prove the reliability of repeatable results, a bottle was placed in the LAB.N2 measuring device (fig. 10) and the measurement noted. The bottle was then removed from the measuring device, and the procedure repeated after a few seconds. The measurement results from multiple repetitions confirm the accuracy of the values attained.
The table below shows 5 measurements from one bottle of a commercially marketed non-carbonated multi-fruit juice. As noted above in the bottling procedure, N2 was added in the sealing process when applying the closure. After this procedure was completed, an analysis using the LAB.N2 device determined the N2 pressure in the bottle to be 0.83 bar. It should also be noted that a period of around 5 weeks expired from the filling date until the product was sold to the consumer. Due to permeation, we were able to determine that the loss of nitrogen pressure was approximately 0.1 bar, as the bottle presumably had a pressure of just under 1 bar on the date it was filled. Comparable measurements of the filling installation later confirmed this assumption. The table below shows the measured results of the earlier bottled fruit juice.
A typical measuring procedure would take a filled and sealed bottle from the bottling line and “hang” it directly in the LAB.N2 device (Image 10). The purpose of the collar is to precisely position and secure the bottle in the optical laser axis. After a few seconds, a valid N2 pressure measurement and the corresponding temperature are shown on the display. Additionally, the device would show an adjusted pressure for a temperature at 20°C. This P20 value is then valid for comparable measurement over a longer period of time.After measuring the bottle, it is placed back into the bottling line without incurring any loss or damage to the bottle or product, and with practically zero potential for operator error. The simplicity and swift generation of the test results enables the employees running the bottling line to perform measurements at increased regularity and therefore ensure improved quality control for the process.
| ||||||||||||||||||||||||||||||||
---|---|---|---|---|---|---|---|---|---|---|---|---|---|---|---|---|---|---|---|---|---|---|---|---|---|---|---|---|---|---|---|---|
It is easy to perform measurements over an extended period of time, with only a small number of filled bottles reserved for quality control. The same bottle is measured over the 6 month warranty period to determine the residual pressure. Using the P-20 pressure analysis (fig. 11), the same bottles can be measured at different temperatures to determine the change in bottle pressure (Gas law). Comparable values are generated by adjusting the measured result to a standardized reading for 20°C, which can be used to determine the rate of pressure loss due to permeation through the PET material. The aging processes attributable to varying temperatures in warehouses and other storage areas are also quickly and easily identified.
Another advantage of this new measuring system is the ability to monitor the quality control of the closure technology. In this application, a small production run is done on the line and each bottle is then examined with the LAB.N2 for the desired internal pressure. Leakage around the closure is quickly identified and the necessary adjustments made to the bottling machinery. This saves considerable time and avoids significant frustration.
Extensive test measurements have proven the reliability and repeatability to +/- 0.03 bar, with the total measurement accuracy of over +/-0.05 bar.
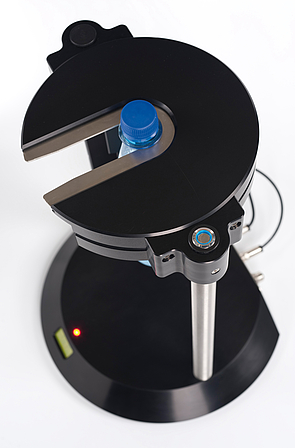
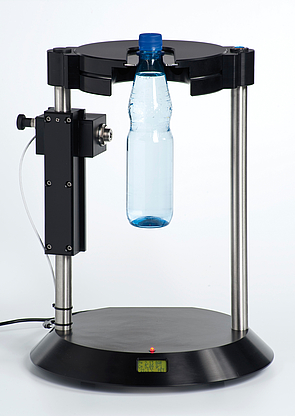
The comPETence center provides your organisation with a dynamic, cost effective way to promote your products and services.
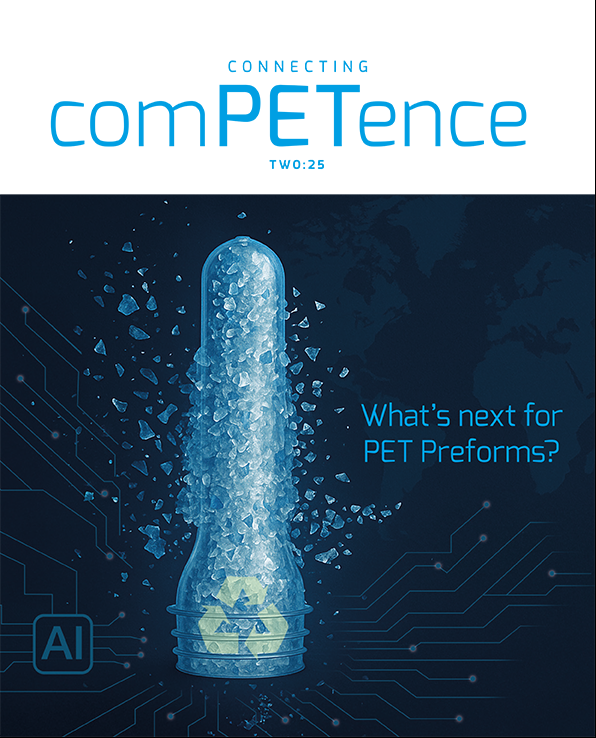
magazine
Find our premium articles, interviews, reports and more
in 3 issues in 2025.