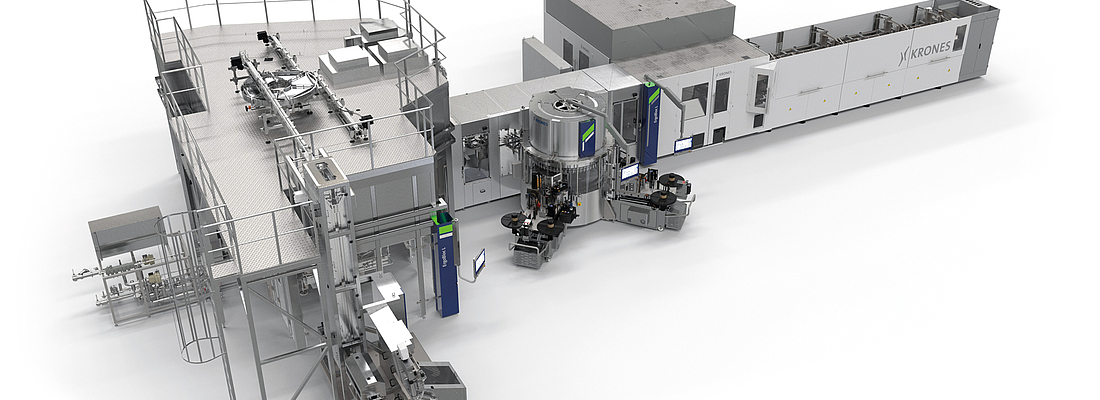
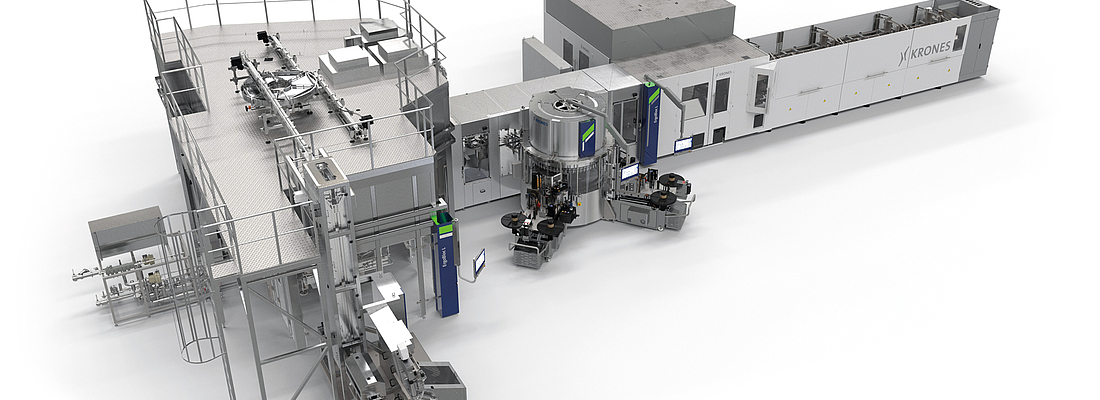
Part 1 of this article provided a brief overview of the factors influencing block technology (see comPETence magazine TWO:2022). It outlined the issues of sustainability, consumer behaviour and population growth. In Part 2, we explore how current challenges are affecting PET as a beverage packaging material and present details of the first Krones ErgoBloc which broke through the magic barrier of 100,000 containers per hour.
Whether it’s climate change, supplying the world’s population with enough food and drink, or responsible stewardship of packaging materials, humankind is currently facing major challenges which are also impacting the food and beverage industries. Meeting these challenges will require a major effort from humankind that can only be successful if everybody pulls together. Starting with each individual and the entire industry right through to governments and organisations, each and every one of us must do their bit – and that includes the beverage industry.
PET is held in low esteem by many consumers as far as sustainability is concerned. In 2019, the media frequently showed pictures of littered beaches or of innumerable plastic bottles floating out at sea.
PET bottles were the subject of critical discussion among the general public, a debate that was often emotionally charged and rarely based on actual facts. That had a major impact not least on German engineering companies, as reflected in declining sales of machines and lines for PET and plastics processing throughout the food and beverage industries, especially in Europe. The cautious stance of European customers, in particular, is easily explained by the uncertainty prevailing at that time in regard to this material.
The plastics discussion reached its peak in 2019. It would seem the situation has calmed somewhat since then. But what is the current status quo? When you look at the worldwide beverage market, you will notice that market acceptance of PET is still very high among beverage producers. Whereas more than 533 billion PET bottles were used for alcoholic and soft drinks plus liquid dairy products in 2021, an output of over 600 billion units is expected for 2025. This corresponds to a growth rate of approximately 2.4 % (source: Global Data, CAGR 21/25). So, despite all criticism, PET continues to rank among the world’s most popular packaging variants.
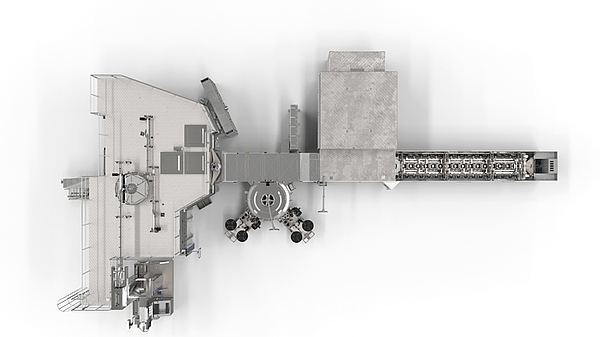
Responsible stewardship of packaging materials
In Krones’ view, PET’s poor image is quite unjustified because this material is indeed able to help solve some of the pressing issues of our era. In the PET debate, people often fail to comprehend that this type of packaging can be sustainable – provided, of course, the process for producing the material is resource-economical and a closed cycle is maintained.
Companies like Krones, for example, already offer suitable options for a sustainable materials cycle, starting with material-saving packaging designs, low-energy container production right through to the recovery of used plastics in the MetaPure recycling plants, for example, which handle polyethylene terephthalate (PET) and polyolefins (PO).
PET offers excellent recyclability, a property that should be taken full advantage of. Re-using existing materials for the original application always makes more sense than downcycling.
A properly functional recycling system and a closed material cycle are conditional on the used beverage bottles being returned to the cycle at the stations set up for this purpose. This helps avoid plastic littering and substantially reduces the impact PET has on our natural environment, because the actual problem is caused not by the PET bottles themselves but by people not handing them in for recycling and thus polluting our natural environment through such careless disposal.
Supplying clean water
Besides recyclability, plastics also have further major advantages compared to other types of packaging. They weigh substantially less, which means PET bottles have a significantly lower environmental impact than other materials over lengthy transport distances. What’s more, plastic bottles don’t break. That is a huge advantage for transport in poorer regions, where the traffic infrastructure, for instance, is substandard and access to clean drinking water is only available on a very limited basis. This advantage can help meet one of humankind’s biggest challenges at present: supplying the world’s population with enough food and drink.
First, the number of people who must be supplied with beverages has to be borne in mind here. According to the German Foundation for World Population, approximately 7.89 billion people were living on our planet in 2021. This number is expected to rise to about 9.74 billion by 2050 and to ten billion by 2100.
Making sure that all of them are reliably supplied with packaged water, for example, is just as important as furnishing them with enough food.
PET can also make a contribution here because it is easy to produce and process large numbers of plastic bottles and transport them to their destination. Returning them to the recycling plant after their contents have been drunk is also simple, by creating an improved infrastructure.
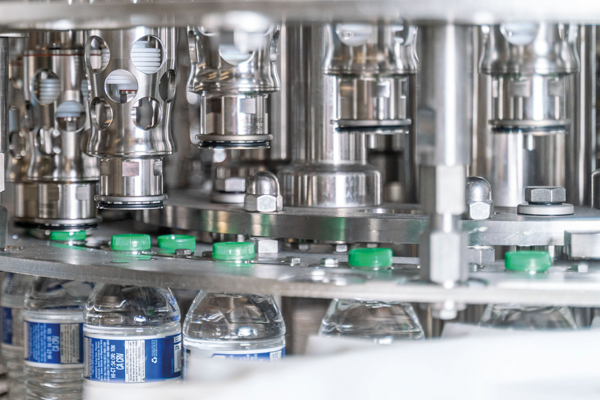
100,000 water bottles in one hour
In order to meet the rising demand for beverages, however, filling companies need appropriate machine speeds. That often leads to the question: several machines in the medium-output range, or rather one high-speed line? As outlined in the preceding edition of comPETence, the energy and media consumption of a big line is lower than that of several smaller ones for the same output.
Krones’ response to this development is the world’s first wet-end block achieving an output of 100,000 0.5-litre water bottles per hour – thus establishing a new benchmark in block technology.
The original order for an ErgoBloc L rated at this high speed was placed by the water bottler Niagara from California. Translating the customer’s stipulations into reality has demanded unparalleled teamwork, as project manager Johannes Bauer explains: “Research and development, four product lines, our service department, sales, production and installation – We’re talking a massive number of departments and people here who have been working hand in hand. This block is a huge collaborative Krones achievement.” Not to mention the technical challenges involved, because to actually achieve this output, the development team at Krones had to think outside the box and take an entirely fresh approach on many different aspects.
The basic production sequence is just the same as in a conventional ErgoBloc L. But when you take a look at the various individual machines, it soon becomes apparent that this block has some key differences to its little brothers.
Stretch blow-moulder as reference machine
The PET preforms are fed into the Contiform 3 Speed stretch blow-moulding machine via the preform feeder. This machine, which was further developed in 2018, already eliminated the pressure pad that had been common until then and, with 2,750 containers per blow-moulding station, set new standards in terms of output and compressed air consumption. But in order to increase the total output to 100,000 containers per hour and at the same time significantly reduce the CO2 footprint, further innovations were to be incorporated into the machine.
And so it came about that some components from the fourth Contiform generation, which will actually only be launched on the market at drinktec 2022, were already used for this high-performance monobloc.
“Development work on the machine has been underway for about three years now,” explains Konrad Senn, CRD Line Solutions and Plastics Technology at Krones. “Besides a number of performance optimisations, the machine mainly features innovations in the heater module and the blow module, yielding significantly upgraded process capability but also a further reduction in energy and compressed-air consumption down to an unprecedentedly low level.”
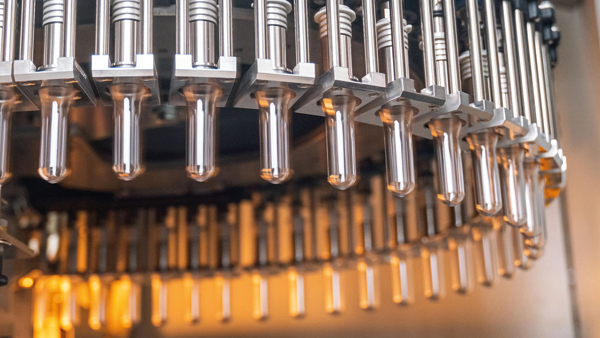
The link between stretch blow-moulder and filler: the Ergomodul
During project implementation, the labeller turned out to be the ideal link between stretch blowmoulding machine and filler. In order to cope with the very high output of these machines, some additional, optimised components, functionalities and assemblies were incorporated in the Ergomodul, which has been the standard labeller for the ErgoBloc L since 2021. For example, the two Contiroll stations and the Multireel magazines for label reels feature a new buffer system which keeps the label tension at a constant maximum level, thus offering ideal preconditions for thin label films, a boon for sustainability. “What was crucial in this context was that the system had already been simulated in detail in the concept phase,” says Christian Holzer, CRD Line Solutions Product Development. “The resulting concept was then progressively finetuned on specifically built test rigs until it yielded consistently stable performance.”
Another of the machine’s key features is the “no bottle – no label” function. If a service rejection in the blow-moulder causes a gap in the bottle flow entering the labeller, no label is transferred to the vacuum cylinder. Simultaneously, the corresponding vacuum cylinder suction bars are retracted upon reaching the gluing unit. The advantages are obvious: Firstly, no label or glue is wasted, and secondly any gaps in the container flow no longer affect the efficiency of the machine, i.e. of the entire line.
Two filling units, two closing units – but only one machine
The filler posed the biggest challenge for the development team because there are physical limits to the standard approach of “bigger carousel equals higher output”. At some point, the masses to be moved and the forces acting on them simply get too big to reliably maintain a stable process. Even though these forces might not be sufficient to set the filler itself shaking, they would certainly cause the product to slop over.
In order to prevent this, the block features two modularised filling units and two modularised closing units. That may sound simple, but was in fact difficult to implement because although the filling/closing of 100,000 bottles per hour is evenly distributed among two units each, these units are still constituent parts of a single integrated block with just one valve rack and one sorting system for closures. “We only provided two of each of the components that are absolutely essential for achieving the stipulated output,” explains Franz Lautenschlager from the CRD Control Technology Department. “Otherwise, we’ve kept everything as lean and small as possible. That is why we’ve incorporated only one central automation system, one touch screen and one control system for the entire block.”
Since stretch blow-moulding and labelling are each handled by one machine, the units to be newly developed included a distribution system for the infeed, which assigns the bottles evenly to each of the filling units downstream of the Ergomodul. Moreover, the machines’ automation system has been programmed to ensure that the block continues in operation even if one of the two fillers fails, and that the blow-moulder is emptied, thus preventing an immediate standstill in the block and minimising the scrap rate.
The Modulfill Dual features around 60 filling valves fewer than a one-filler solution would need for the same output. Thanks to its compact size, the filler takes up less space, but its output is still almost 20 per cent higher.
And if all of this weren’t impressive enough, the high-speed block is also the first ErgoBloc L to incorporate the Connected HMI with a new visual display system. “Last but not least, there’s a big package of digitalisation features, which is linked to Syskron’s cloud solutions,” says product manager Michael Kobel. “These range from extended analytical functions for condition monitoring and predictive maintenance right through to automatic process control.”
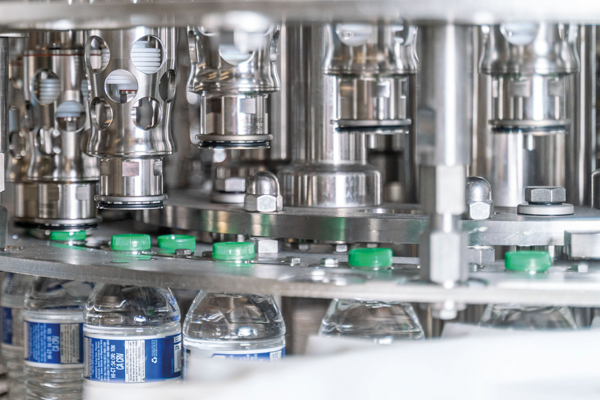
Maximised performance and sustainability – a contradiction?
In 2021, the European Union set a legally binding target for eliminating net emissions – i.e. becoming climate-neutral, by 2050. 2030 was set as a milestone because the intention is to have cut emissions by 55 per cent by then. The specifications are called the “New Green Deal“ and are included in the “Fit for 55” package.
These specifications have an impact on society as a whole – and thus on companies from the beverage industry as well because the framework conditions specified in the package include a closed plastics cycle and of course a reduction in CO2 emissions.
Bearing that in mind, is a block which produces 100,000 PET bottles per hour sustainable at all? Is it compatible with current efforts? That is easily answered because what counts in the end are substantiated figures.
When compared to a 72,000-bph block built in 2015, the high-speed block provides substantial energy savings even though its output is significantly higher. Technical upgrades in the heating tunnel, for example, reduce energy consumption by more than ten per cent. And compressed-air recycling in the stretch blow-moulding process cuts the energy required by 15 per cent. In combination with other improvements, that yields energy savings of over 16 per cent.
As a result, the TCO is up and Scope-2 emissions are down, thereby helping beverage producers to comply with EU specifications.
Lightweighting and the use of rPET save thousands of tons of CO2
Lightweighting optimisations also help to meet the targets. They enabled the Niagara water bottler, for example, to save about four per cent in bottle weight, entirely without reducing production performance. There is a substantiated figure for this, too: Thanks to lightweighting, it was possible to save a total of 720 tons of CO2 per year in the line, which also cut costs since less material was needed.
However, the use of rPET still offers the biggest opportunity to save CO2. If 100 per cent recyclate is used on the 100,000-bph ErgoBloc, up to 3,600 tons of CO2 per year can be saved. This is precisely why it is necessary to establish a closed plastics cycle (as specified by the EU) at the global level.
The comPETence center provides your organisation with a dynamic, cost effective way to promote your products and services.
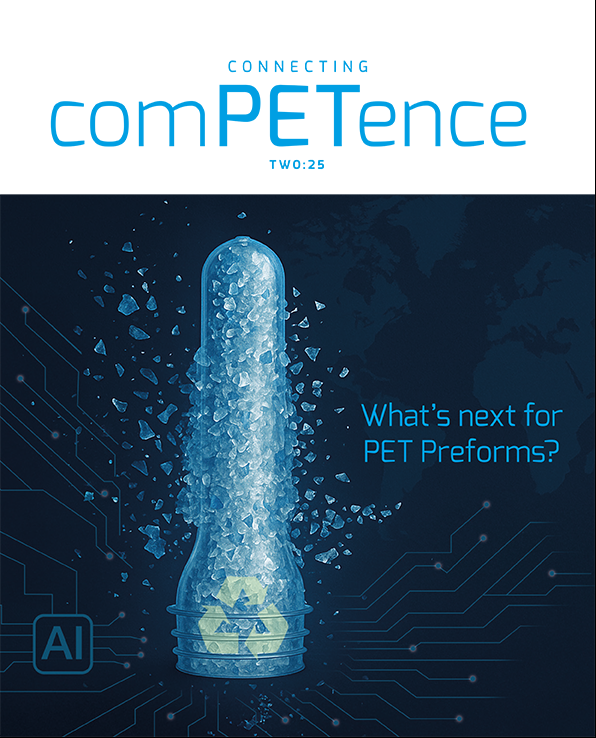
magazine
Find our premium articles, interviews, reports and more
in 3 issues in 2025.