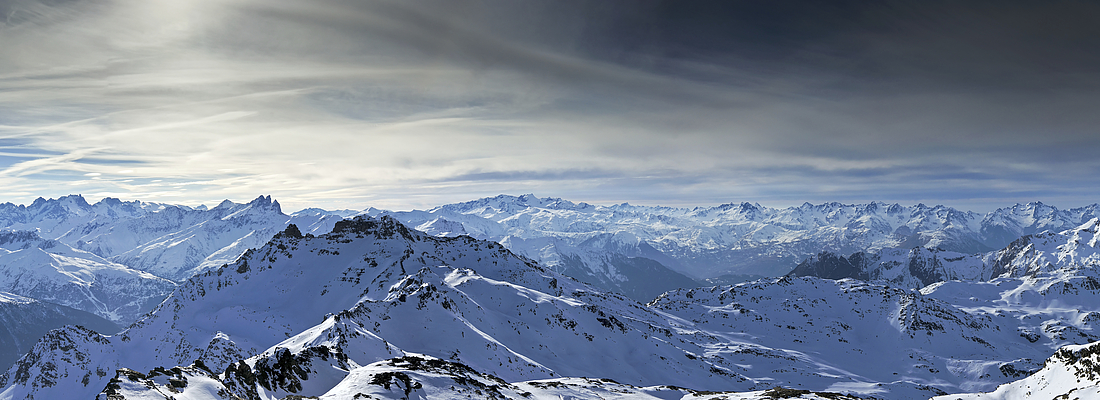
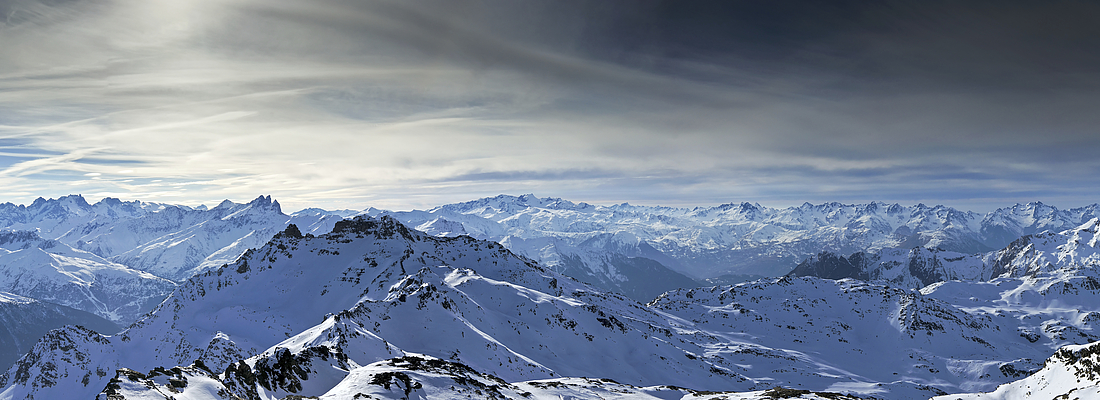
Photo credit: ColdJet
It’s Cold as Ice … - Keeping moulds and cavities clean is a major concern for plastic product manufactures in maintaining today’s high quality standards and ensuring maximum productivity
We, Peter Fahnenbruch and Otto Appel, spoke with Dietmar Juchmes and Steffen Kalisch from Cold Jet about Dry Ice Cleaning.
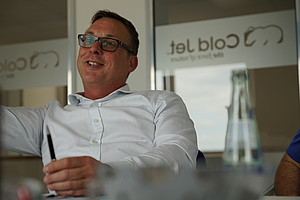
Cold Jet was founded in Loveland, Ohio, USA. Please tell us about the first steps and beginnings.
Juchmes: Yes, Cold Jet officially opened its doors in Loveland, Ohio, USA in 1986 with just a small group of 25 employees, one production facility and the desire to turn a great idea into a truly great product. Support came from the U.S. Air Force awarding Cold Jet 1990 a contract to develop dry ice blast cleaning and paint stripping systems. Since this time, Cold Jet has been pioneering the research and development of dry ice blasting by setting the standard for quality, performance and reliability in this field for more than 30 years. And we are based in Europe already since 2003 and here in Germany since 2004.
This year we will reach more than 260 direct employees in addition to our partners excisting out hundreds of contractors and distributors. The Cold Jet team consists of experts with mechanical engineering degrees coming partly from the aerospace industry and technical sales with a solid know-how in the manufacturing environment. The strength of Cold Jet is our global knowledge and our local presence. At the same time Cold Jet offers 24/7 technical support, local and globally.
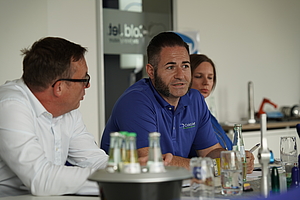
How easy is the Cold Jet principle or technology for cleaning tools? The devil is known to be in the detail.
Kalisch: The Cold Jet product range is based on a patented dry ice technology for superior results, which covers our dry ice blasting solutions with solid CO2 Pellets (3mm) or micro particle systems (<0.3mm), Integrated Blast Systems, which is ideal for production integration and our dry ice production solution. The dry ice cleaning process itself is similar to other types of media blasting. It prepares and cleans surfaces using a media accelerated in a pressurized air stream. The Cold Jet principal with dry ice cleaning is using - as mentioned - solid CO2 pellets or microparticles, which are blasted at supersonic speeds and sublimate on impact, lifting dirt and contaminants off the underlying substrate. Moulds must be cleaned properly, regularly and in an environmentally responsible way. Cold Jet dry ice blasting enables fast and better cleaning of multiple mold types and other machine components without using hazardous solvents and without creating additional waste.
Dry ice is a non-conductive, non-toxic, environmentally responsible and safe cleaning media. It is a soft media and non-abrasive on many surfaces so it is ideal to clean delicate surfaces without damage.
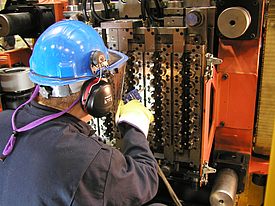
Environmentally friendly cleaning - please explain the Cold Jet applications and product range.
Juchmes: For key industries, Cold Jet developed industry specific ‘Edition’ dry ice cleaning machines. For the plastic industry and specifi cally PET perform mould cleaning, Cold Jet recommends for PET solution the Aero 80FP. This system with its specially designed applicator and nozzles allow non-abrasive cleaning even in the hardto-reach areas of PET preform moulds. This is accomplished without the use of chemicals or scrapers and with no secondary waste to ensure a complete clean every time.
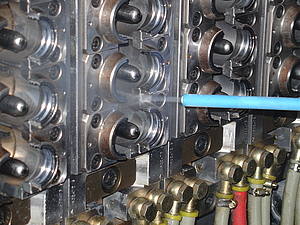
Who are Cold Jets main customers and what kind of special requirements do they have?
Juchmes: Today, Cold Jet is used by more than 7.000 customers worldwide, in more than 35 industries and hundreds of applications. One of our key industry segement is the PET Preform Mould Cleaning application. Cold Jet’s environmental cleaning and surface preparation systems have helped packaging molders meet stringent productivity demands. Our systems help molders clean faster, efficient and more economically, while increasing production capacity and improve product quality. Mold cleaning times are reduced up to 75% with Cold Jet systems. Due to the unique properties of dry ice as a cleaning agents, complete molding parts such as lock rings, neck rings, cavities, take out tube, cores, gate inserts and tapers are cleaned without the disassembly of the stripper plate while the mold remains in the press. In addition the process also cleans air vents and PET gate nubs before start up.
The key requirement our customers have is cost and time saving with their production. With our offer of cost savings and efficiency it is of no surprise Cold Jet has teamed up with industry leaders as diverse as aerospace, automotive and food services. Many of our customers operate globally using Cold Jet dry ice blasting due to the benefits they have realized. Cold Jet main customers today are from plastic & composite industry, rubber, tire & automotive industry. As well as contract cleaning to the food, gas & oil industry.
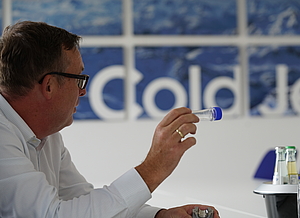
Where are your systems and service parts manufactured?
Kalisch: Cold Jet has production facilities in Milford, Ohio/USA, Oborniki/ Poland and Bramming/Denmark. In several other countries we have one or more test centres for presentations, equipment demonstration and/ or sample testing to validate the effectiveness of dry ice cleaning on parts and specific cleaning applications.
You have built a new Technical Centre in Weinsheim, Germany, why this location?
Juchmes: Cold Jet has had a facility in Weinsheim since 2004. Over the years, numerous people with management, technical, marketing and administrative competence joined the Cold Jet Weinsheim office. So for Cold Jet it made sense to keep this location also for the new technical training centre in Europe. Our second technical centre in Germany is located in Munich.
What is the risk of substitution for this technology?
Juchmes: Dry ice cleaning is a nonabrasive cleaning solution. Switching back to traditional cleaning methods can result in premature wear of the mould shut-offs/parting line and may result in loss of production. Traditional cleaning methods are slower than dry ice cleaning. PET preform moulds have complex geometries, which are not easily cleaned manually. Traditional cleaning times can run up to 3-4 hours, vs. 45 minutes with dry ice cleaning or a loss of 3.25 hours of production. For example, taking a 192 cavity preform mould running a 6 second cycle, you calculate a loss of 374,400 preforms per cleaning cycle! This is an Availability Loss for those tracking OEE scores in their plant.
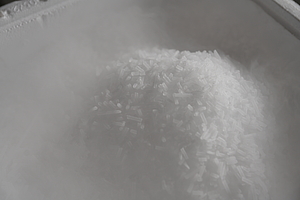
What are the options to reduce downtime?
Kalisch: In the case of PET preform moulds, Cold Jet dry ice cleaning can reduce the cleaning time by 2/3. Moulds can be cleaned during the production process without dismantling the mould or cooling down the hotrunner. The cleaning is safer and the production can restart 70% faster than before. Moulders have less mould wear, no secondary waste and chemicals are no longer needed. In addition the (recycled) CO2 is food grade certified. Which development topics are on your agenda?
What can the industry expect in terms of Cold Jet innovations in the near future?
Juchmes: Cold Jet is globally known for its environmentally sustainable cleaning, surface preparation and transport cooling solutions. Our Engineering, R&D, production and assembly operations are continuously working to find new and improved solutions for our equipment and customer applications world wide with state-of-the-art equipment and cutting-edge processes (including Electrical Discharge Machining within tolerances of only +/- 0.0001”).
Cold Jet now offers equipment that is Industry 4.0 compliant via our Cold Jet Connect™. Equipment can communicate remotely production parameters back to a customer’s plant monitoring systems provide predictive maintenance schedules and most efficient, process adaptive solutions to the market.
Where do you see significant growth opportunities?
Juchmes: All over the world were CO2 is available, dry ice cleaning has great growth potential. Less production downtime and higher production is key in every production facility. Also the co-worker safety is critical. Chemical cleaning agents are often no longer allowed, and more and more companies strive to be lean (reduction of waste & costs), clean (improved finished goods), and green (environmentally responsible).
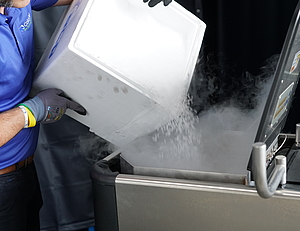
Which challenges from the market will be reflected in the development and possibly also in sales?
Juchmes: Moulders are always looking for more effective and efficient ways to produce their products looking to pursue the use of automated solutions. Cold Jet now offers semi-automatic, as well as fully automated and integrated blasting solutions. Cold Jet is the leader in listening to market demands by remaining one step ahead of such market demands.
What is the competition for Cold Jet? Is there a serious competitor?
Kalisch: There are other local companies that manufacture dry ice blasting equipment, which are not developed for industrial applications and are not specialized for cleaning PET moulds. Cold Jet machines are specifically designed to clean a PET production moulds and areas such as difficult accessible neck and lock rings.
With PETnology, we are primarily in the packaging industry with a focus on PET / closures / recycling. How do you see Cold Jet being positioned?
Juchmes: Cold Jet’s environmental cleaning and surface preparation systems have helped packaging molders meet stringent productivity demands. The systems help moulders clean faster and more economically, while increasing production capacity and improved product quality. Mold cleaning times are reduced up to 75% with Cold Jet.
Being very versatile, Cold Jet has a solid position in the equipment cleaning industry cleaning mould, machines, automotive applications and many more.
How big is your business share in the packaging sector?
Juchmes: About 50% of our business is in the cleaning of packaging mould applications.
The packaging sector is due to our 3 mm Pellets to 0.3 mm unique microparticles for precise and sensitive cleaning the perfect solution and more and more interesting to the market. Here we see potential growth long term.
Political issues are increasingly gaining influence. How will Cold Jet position itself on the still new but expanding foreclosure policy? Are there any particular concerns regarding business between the US, Germany or Europe?
Juchmes: As a company with a global customer base, we see it as a requirement to have production sides and service support in Europe, USA and Asia. This will reduce risks on our side and help fulfill the required expectations from our customers locally.
Thank you.
The comPETence center provides your organisation with a dynamic, cost effective way to promote your products and services.
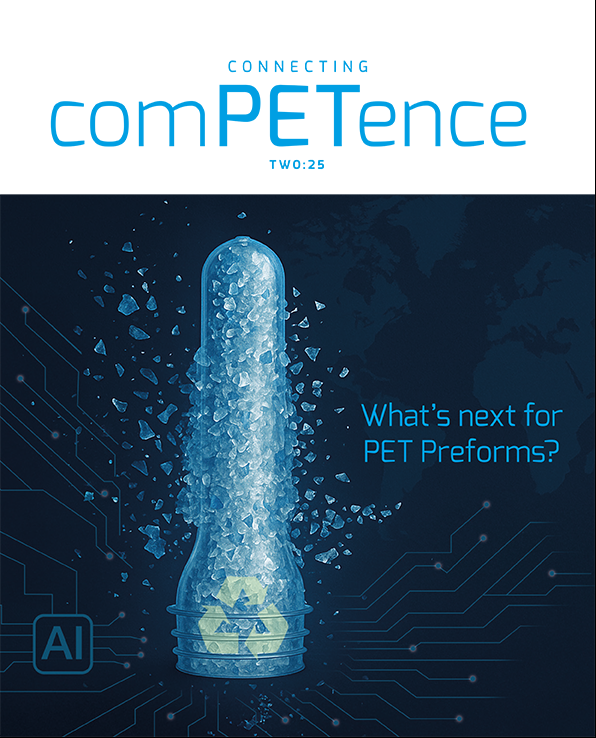
magazine
Find our premium articles, interviews, reports and more
in 3 issues in 2025.