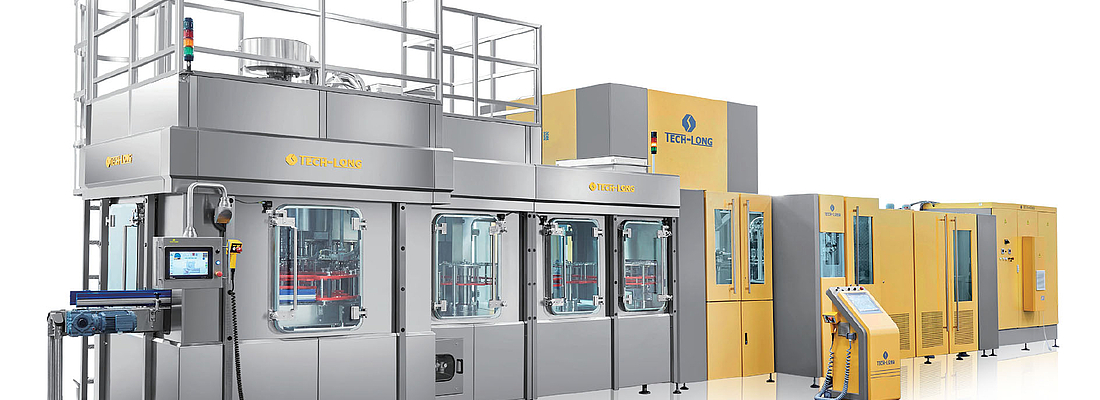
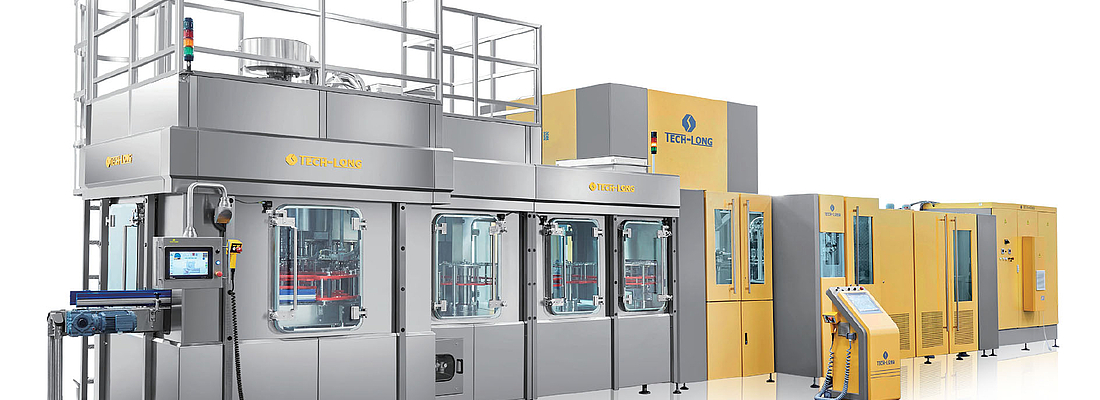
Over the last 20 years the concept of blocking together PET bottle blowing with filling and capping into one machine has proven itself successful and has been adopted by all major beverage equipment manufacturers. Today beverage producers are more and more under an always increasing cost pressure, which forces them to look for reliable and cost-effective solutions for their production means. Tech-Long has developed the widest range of Blow- Fill-Cap Monoblocks (BFCs) to support the bottling manufacturers especially in the long- term cost structure of their investments. Within its portfolio Tech-Long has the most diverse range of BFCs available on the market.
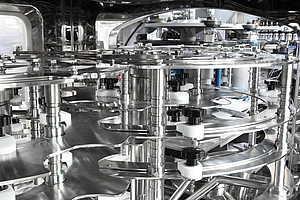
BLOWING PART:
The CPX range of rotary stretch blow molding machines spans from 4 to 26 cavities for standard bottles with blowing speed up to 2.400bph/mould. For large containers (up to 10 L) the portfolio consists of rotary blowers from 4 to 8 cavities. Such complete range combining a wide offering of blowing speeds, and a large span of container size, allows Tech-Long to answer to most of the bottling market requirements and constraints.
FILLING/CAPPING PART:
The Filling-Capping part is linked to the type of product bottled and covers all kind of drinks, liquid foods and non-food products such as: Water, CSD, Vegetable Oil, Vinegar, Juices, Teas, Isotonics, Household products, Car Fluids and Detergents. In that respect the fillers integrate a wide variety of filling technologies such as: flow meter, weight-cell, gravity, Isobaric, Volumetric and Electronic filling valves for cold as well as hot fill applications.
During Drinktec 2017 Tech-Long exhibited its BFC 6/30/10 for large containers up to 10l. It is a monoblock combining its CPXD6 large container blow molder and a 30-valve weight cell Filler running at a Record speed of 8.400bph for 5L water bottles!
THANKS TO IT‘S UNIQUE TECHNICAL FEATURES THE TECH-LONG BFC OFFERS BEST IN CLASS TCO:
Active controlled spindle rotation in the oven for an optimized heat profile of the preform, high pressure air recycling up to 50%, electro servo stretch-cylinders, 3-step blowing, format quick -change system are some of the unique Tech- Long features. The especially low maintenance cost result from the use of easily available standard parts from first class international suppliers. Hygiene is also one of the main points of focus, whereas the BFC range include a full set of hygienic features allowing to guarantee the product integrity by protecting the bottle transfer and filling area from outside contamination.
Tech-Long has also developed partnership agreements in which the BFC is based on a Tech-Long blower and the filler/ capper comes from a reputable partner. Such flexibility allows to offer best in class equipment for each and every application.
With more than 250 BFCs in industrial operation around the world, Tech-Long is one of the leading Blowing/ Filling / Capping Monoblock manufacturer.
Rather than having various in-house experts commenting on final user benefits of the Tech-long BFC, we have asked an experienced bottling customer located in located in Montebello, California to comment himself: UNIX-Packaging UNIX-packaging Inc is one of the most advanced and state of the art contract beverage manufacturing facility on the West coast of the United States. The company has a manufacturing facility of 125.000 square feet hosting 7 highly flexible bottling lines with speeds between 2.500 to 36.000 bph.
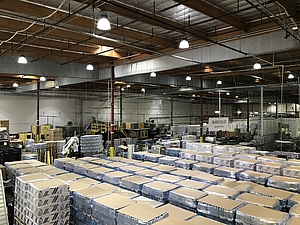
Thanks to its reactivity and the flexibility of its lines, Unix Packaging is able to offer a wide range of products: functional beverages, carbonated soft drinks, purified and enhanced water, kombuchas and teas. All of those can be provided in different SKUs with variable labelling options and packing solutions, to be able to offer its customers a wide choice of custom made products. Unix is proud to serve highly renown brands and big box retailers. I had the chance to chat with Mr. Bobby Melamed, CEO and President of Unix Packaging.
Dominique Lipinski: Hello Bobby, thank you for giving us the opportunity to have this discussion. I see you have a large variety of products and SKUs. How have you prepared for that?
Bobby Melamed: Yes absolutely, flexi- bility is a key success factor in our business, and the whole company is set up around this flexibility philosophy. Not only our organization has to be flexible and reactive as well our bottling equipment, all have been planned and designed for that purpose: from producing glass to PET bottles, different neck finishes, different caps, different products, different labeling options, different packing possibilities. Our lines have the flexibility to offer our customers whatever product they require.
DL: Your latest investment consists of a Tech-Long Blow Fill Cap block BFC 16.70.20, can you tell us why you have chosen Tech-Long?
BM: Our relationship with Tech-Long goes back to the early days of UNIX -Packaging, over the years we have bought several equipment and have been satisfied with the technology, the service, and moreover the special attention Tech-Long has been showing to us.
DL: Can you tell us why you have chosen a BFC Blow/Fill/Cap Block vs a classical solution of blowing / air conveying / Filling?
BM: Well, it was driven by our customer! When discussing the project, they suggested we use a BFC block for his products, especially because of the high hygiene properties of the Tech-Long BFC vs an air conveyor solution. The project was managed very well, and installation happened very smoothly. It was not simple, because we had a smaller Blower and filler actually producing, and the challenge was to replace the existing smaller line by this BFC block without affecting our production plans. That happened seamlessly.
DL: After now some months in operation, are you satisfied with your BFC Blow/Fill/Cap block?
BM: Yes absolutely, aside the hygiene factor, we have also noticed an increase in productivity linked to the higher efficiency of such a block compared to an air conveyor solution - we are really satisfied. Efficiency in production is one of our key drivers, and the Tech-Long BFC Block really brings added value to our production capabilities and results.
DL: Being aware, that Tech-Long machines are manufactured in China, does that lead to any difficulties in dealing with them?
BM: Not at all, the Tech-Long team in US is highly reactive, very close to us. This does not at all impact our relation and dealing with Tech-Long as one of our major suppliers.
DL: What would you say are Tech Long strong points today?
BM: As I mentioned earlier, the service we are getting from Tech-Long, as well as the special attention makes us feel very confident. The reliability of the equipment, ease of operation and maintenance are as well some of their strong points.
The comPETence center provides your organisation with a dynamic, cost effective way to promote your products and services.
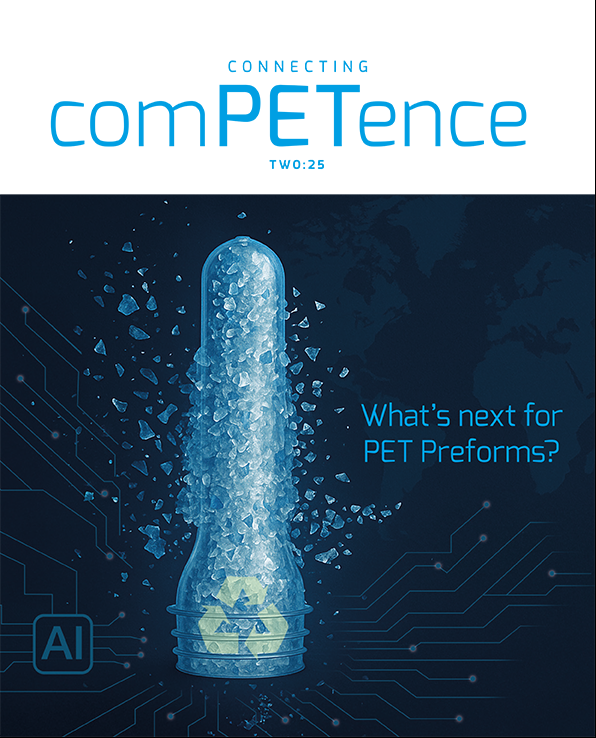
magazine
Find our premium articles, interviews, reports and more
in 3 issues in 2025.