It is often a combination of small things that have a big impact, as is the case when filling sensitive beverages into PET and HDPE bottles. Here, with a whole range of innovations for its system solutions KHS provides greater efficiency, more flexibility, increased ease of operation and optimum product safety.
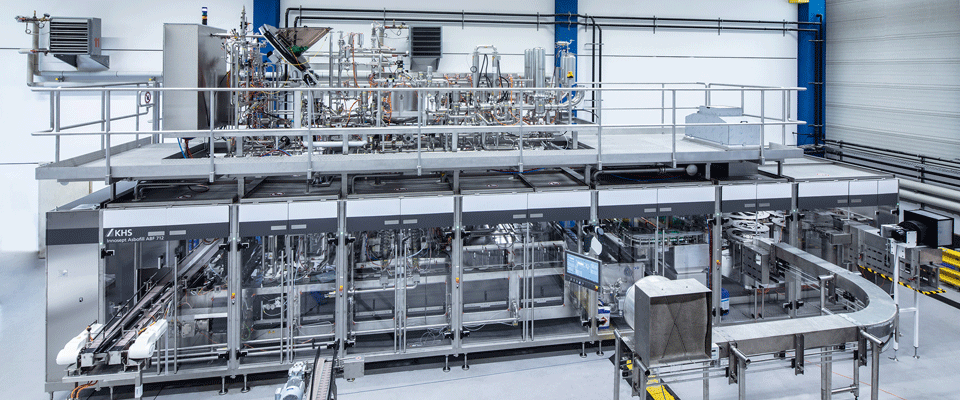
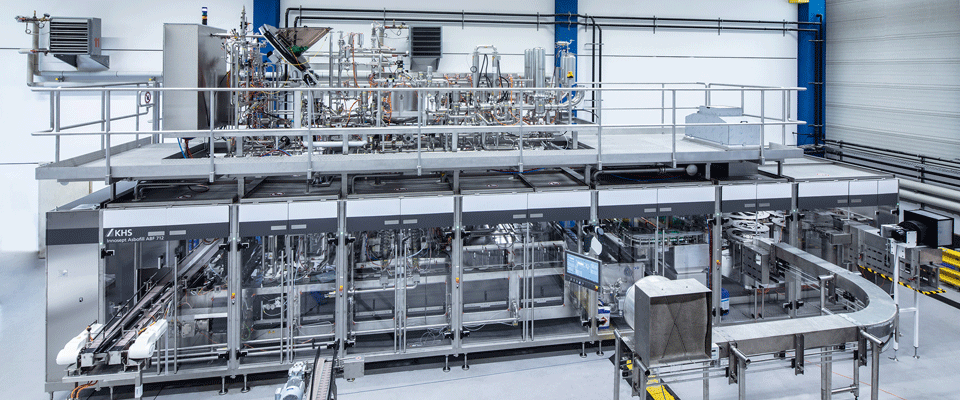
Proven technology, further developed to include numerous innovations: the KHS Innofill PET ACF-L linear aseptic filler in the assembly shop. (Photo credit: KHS)
Aseptic Filling
Growth market for sensitive products: KHS provides numerous innovations for system solutions
- Further developments provide greater efficiency and flexibility
- Bottlers benefit from improved product safety
- KHS offers extensive portfolio for various requirements in aseptic filling

Mixed milk beverages, juices, smoothies, iced teas and near-water products are in – and the list of sensitive beverages continues to grow. They make high demands of hygienic filling so that the consumer can enjoy them fresh. “When filling and capping beverages so as to prevent recontamination, filling under aseptic conditions especially is a gentle process,” explains Manfred Härtel, filling product manager at KHS. There are hardly any alternatives to this technology. “With over 25 years of experience KHS is a real pioneer and specialist when it comes to hygiene and freshness. This is also demonstrated by the fact that we offer our customers a full range of systems tailored to suit very different requirements.”
KHS technology is always state of the art regarding the task on hand, namely the sterile beverage filling of sensitive products, and continuously ensures the best possible hygienic conditions, as Härtel explains. Nevertheless, KHS is constantly striving to further improve its lines and machines. At the moment, a total of seven optimizations for the modular KHS linear aseptic filler are helping to further boost its efficiency and flexibility in particular. Most machines can be retrofitted with the further developed components.
Variable aseptic block
KHS’ linear aseptic fillers can be blocked with a rotary stretch blow molder – in this case, an InnoPET Blomax V – to form an extremely compact unit. For this purpose, KHS has developed a transfer module that harmonizes the continuous PET bottle flow with the stepped filling process. This is done with the help of a transfer carousel that separates the containers into units of ten. During a brief stop phase these are removed by grippers and placed in the filler’s carrier plates. There are three variants of the module: one for blocking with a stretch blow molder, a second with an additional discharge to a Plasmax coating machine and a third with an extra bottle infeed that enables the filler to process both PET and HDPE bottles.
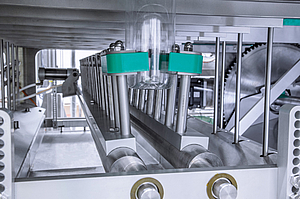
Optimized bottle infeed
With the number of bottle formats and designs rapidly increasing, systems have to be more and more flexible. Unlike in the past, following a format changeover the bottle infeed is now no longer set up in a repetitive process that involves loosening and fastening screws, running tests and making fine adjustments. Instead, handwheels marked with scales permit the exact height and diameter of a container to be easily configured and ensure that these settings can be reproduced at all times. This reduces the time for format changeovers by up to 40%.
Optional flexible servo capper
Instead of one drive for all ten capping heads, each capping head is equipped with two servodrives apiece. While the first drive lifts and lowers the capper cone, the second drive controls the capping rotation. The servodrives are programmed on the HMI. Automated conversion and the reproducibility associated with this allow different caps to be used, thus increasing flexibility without the operator having to make any manual adjustments. The parameters needed for correct capping of the PET bottles are stored in what are known as cap recipes; each cap used can be individually configured.
Improved bottle fixing
Bottle grippers act as an anti-twist lock that holds the container in place just above its base while the screw capper screws the bottle cap closed. KHS has now replaced the previous circular rubber bumpers held by one arm respectively by much larger half-shells that are attached to two arms each. The effect is similar to holding a bottle with two hands instead of with four fingers: the larger contact surface reliably prevents unwanted rotation of the container. The bottles are correctly capped; the number of leaky containers channeled out and thus the reject rate are reduced.
Switching valves for optimum filling behavior
Increasing product diversity in the beverage industry means that some products are more challenging to fill than others because of their foaming properties. Flexibility is called for here. A new switching valve controls the volume of the inflow to the actual filling valve and thus permits a total of four different infeed speeds. If the infeed is slower or at a lower volume, the amount of foaming is reduced. The infeed speed is stored in the product recipes; there is no need for manual conversion. This improves filling accuracy and means that the filling volume can be more easily reproduced. Foaming in the bottle during filling is also minimized. This results in a stable output of beverages with different properties, in turn boosting efficiency and the flexibility required to fill a wide assortment of products.
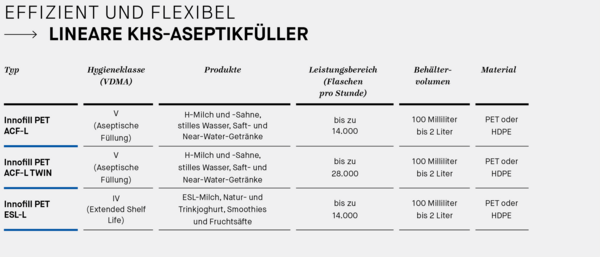
New ring gap filling valve for pulp and fibers
If the portfolio requires it, beverages with pulp and fibers can be processed by the new ring gap filling valve without any loss of performance. Products with fibers 15–20 millimeters long and a high pulp content can even be filled without the machine becoming blocked or clogged. As opposed to the usual filling valves with a gas lock, on the new valves the valve cone is placed directly at the discharge so that nothing sprays or drips. What’s more, the filling jet is so homogenous and streamlined that a lot less foam forms in the bottle.
Longer maintenance intervals
Whereas in the past maintenance was required at relatively short intervals for microbiological reasons, with each session lasting five to eight hours, maintenance intervals have now been lengthened so that machines only need to be serviced once or twice a year. Thanks to improved hygiene, increasing experience in the operation of machines and modern materials such as PTFE (polytetrafluorethylene or Teflon), KHS has been able to reduce its safety buffer down to a reasonable level. Now four times longer, these intervals follow on from one another and include all tests previously performed during maintenance. This gives beverage producers much higher machine availability. Operators also profit from cost savings for maintenance and overhauls of up to 20% within five years.
Aseptic filling technology from KHS is complemented by an extensive portfolio of proven process engineering machines. “We provide systems and solutions from a single source,” Härtel emphasizes. “These range from the blending of components in the syrup room through deaeration and aseptic flash pasteurization just before filling to chunk dosing in a dual-flow process.” The Dortmund company thus provides the full bandwidth of technologies and services needed to make the increasingly popular beverages in the sensitive product segment – from acceptance of the raw material concentrate through design of the bottles and their components to filling and packaging of the product.
The comPETence center provides your organisation with a dynamic, cost effective way to promote your products and services.
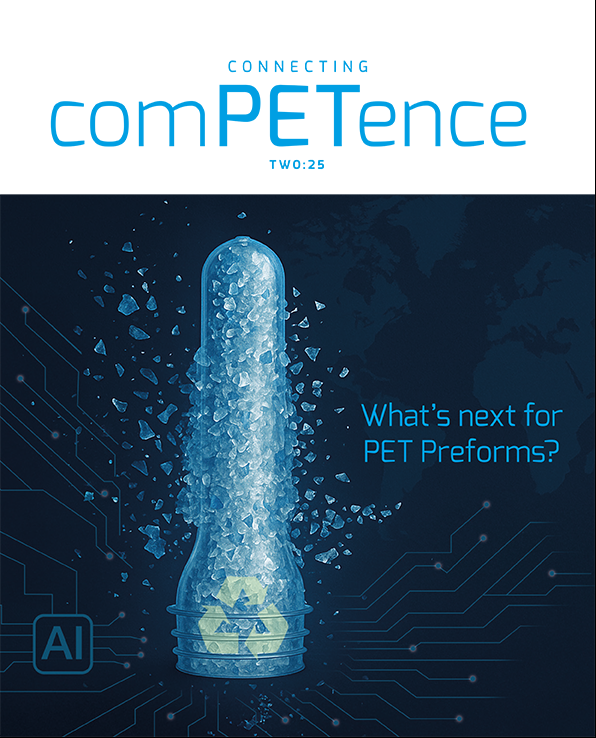
magazine
Find our premium articles, interviews, reports and more
in 3 issues in 2025.