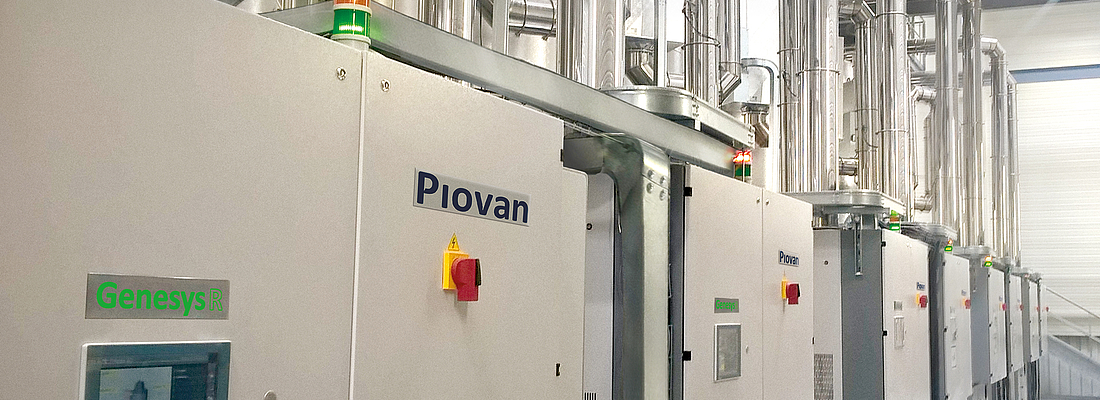
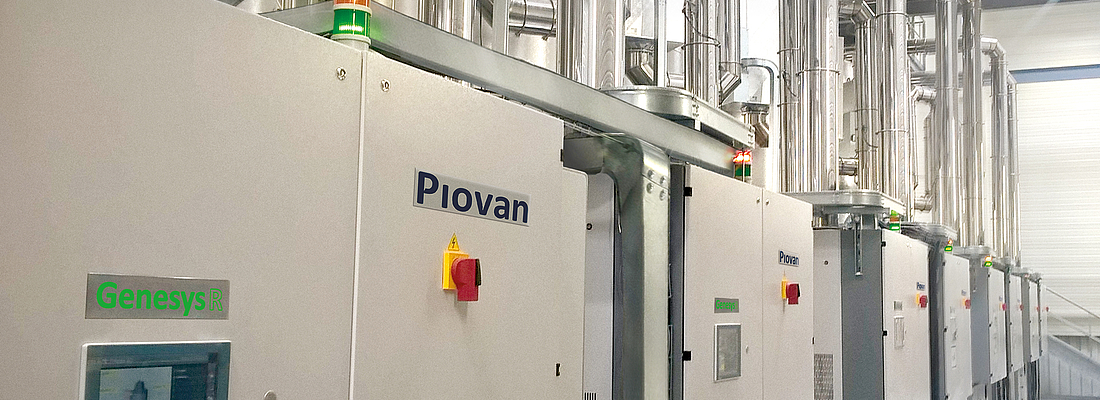
We had the chance to talk to Peter Dal Bo, CCO at Piovan Group, about the new GenesysR drying technology during the Otto Systems presentation at BMB in Brescia.
Piovan’s Genesys system delivers PET-resin drying with an energy consumption 55% lower than today’s conventional resin-drying systems. GenesysR is a new product – how does it build upon this energy-efficient profile?
Dal Bo: The new product we have presented to our customers during the K show and have officially launched at the PETnology Forum in Nuremberg is GenesysR, the new generation of “reactor drying systems”. Reactor drying is a new technology, combining the benefits of rapid heat up of the PET with a new innovative control of the residual moisture of the resin. Piovan was a supplier of small scale vertical tower SSP systems, a range of products that would find use in the late 80’s, early 90’s, that allowed us to learn in depth about the physical phenomenon taking place in the vertical tower (reactor) while rapidly increasing the polymer temperature. SSP takes place at temperatures of 220°C and in absence of oxygen. GenesysR operates at regular drying temperatures (170 to 180°C) in a dried air environment and, differently from what happens in an SSP process, it does not increase IV but can reduce the drying time from 7 hours to 5 hours. The energy efficiency, a very strong point of the Genesys line, is further increased by 10 Wh/kg, meaning any GenesysR will ensure savings in the range of 60% and beyond when compared to a conventional drying system. Piovan holds the only patent ever released for “High efficiency system for dehumidifying and/ or drying plastic materials”, dated 29 May 2013, EP2186613B1, obtained as a consequence of the exceptional results and performance of Genesys.
Is the high productivity of the GenesysR also maintained?
Dal Bo: The GenesysR line is particularly suited for high productivity applications, where the benefits of having a very low energy utilization and a highly stable process are exploited in the highest degree. GenesysR benefits of a very innovative control of the residual moisture in the PET, namely AIPC. AIPC stands for Automatic Injection Pressure Control. Any GenesysR system can be connected to the preform injection moulding machine and by reading the injection pressure in real time has the capability of stabilizing it to the desired value. A new algorithm specifically developed for the AIPC can constantly adjust airflow, temperature and dew-point of the process air, so that the injection pressure be kept at the highest possible level of constancy. This feature is particularly valuable today as the new preform formats require thinner walls and therefore controlled conditions of moisture and injection pressure. AIPC is a patent pending new invention.
Alongside this productivity and energy efficiency, Genesys also delivers high quality and constancy of physical characteristics. How will the GenesysR support beverage packaging manufacturers in this respect?
Dal Bo: GenesysR is the only auto-adaptive drying system available in the market that is capable of determining a condition of energy balance in the PET resin between drying and injection processes. The reason why energy balance is key for the production of a preform, and subsequent bottle, resides into the physical and mechanical characteristics of the bottle itself. The best processing condition for the PET resin is obtained when the lowest possible temperature increase, or energy addition, must be performed by the injection unit, or extruder. GenesysR is capable of measuring the quantity of energy released to the PET, so to feed the injection unit with material having the highest possible mass temperature. The energy addition at the injection unit is a very critical parameter, as it determines the IV drop of the PET: the lower is the energy addition the lower is the IV drop. The auto-adaptability feature of GenesysR benefits the bottle characteristics from two main perspectives: highest IV of the PET, obtained by the energy balance capability, and lowest AA level, obtained by the AIPC feature.
How did you develop the new product, and will it ultimately replace Genesys?
Dal Bo: GenesysR is the evolution of Genesys and represents a further step towards optimization and perfection of the bottle manufacturing process. The development of this new category of drying systems, the new “reactor drying systems”, was not performed in a one, two or three year program, it is the outcome of being the all time market leader in PET drying systems, since PET has been introduced to the rigid packaging industry. GenesysR is not available in all the configurations of Genesys. The two product lines will coexist.
How have you tested and certified it?
Dal Bo: Ten GenesysR beta installations have been functioning for the latest 9 months and the first GenesysR systems will be made industrially available in the first quarter of 2017.
Piovan first introduced an auto-adaptive system - able to adjust the functioning mode of the drying system - to the industry in 2009. What makes auto-adaptability so advantageous, and how does the technology work in your new product?
Dal Bo: GenesysR features the highest degree of auto- adaptability. If such function was valuable back in 2009, it has become indispensable today. Auto-adaptability allows the use of multiple grades of PET, from different suppliers and produced in different processes. PET is today available in the so called water grade (0.72 IV) and bottle grade (0.82 IV), however it can be produced by utilizing very new and innovative processes of polymerization and solid state post condensation, along with older production systems.
Many PET from many sources are available today, each requiring different processing or preparation conditions to be adequately and efficiently transformed into a preform/ bottle. GenesysR is the first milestone of Industry 4.0 in the rigid packaging industry, as it is a concrete example of how an Industry 4.0 compliant system, the so called Cyber Physical System, is configured to operate for the objective of achieving:
a. Highest constancy of production,
b. Highest preform/bottle quality,
c. Stables injection moulding and blow moulding machine operation
d. Reduction of scrap rate to zero,
e. Highest energy efficiency of the preform system.
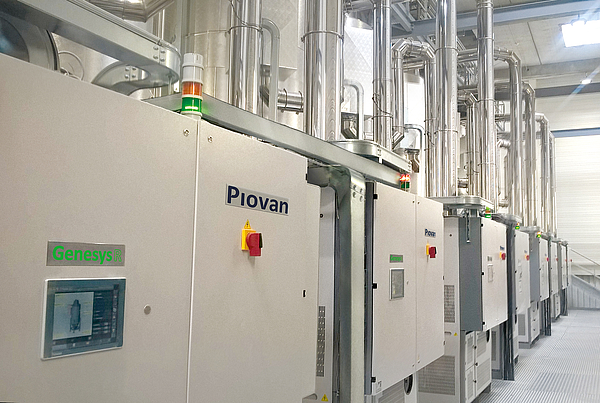
The comPETence center provides your organisation with a dynamic, cost effective way to promote your products and services.
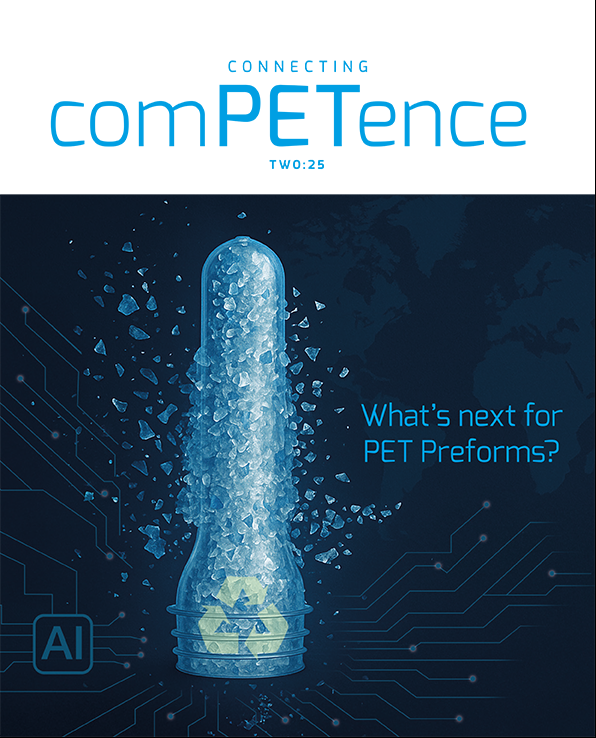
magazine
Find our premium articles, interviews, reports and more
in 3 issues in 2025.