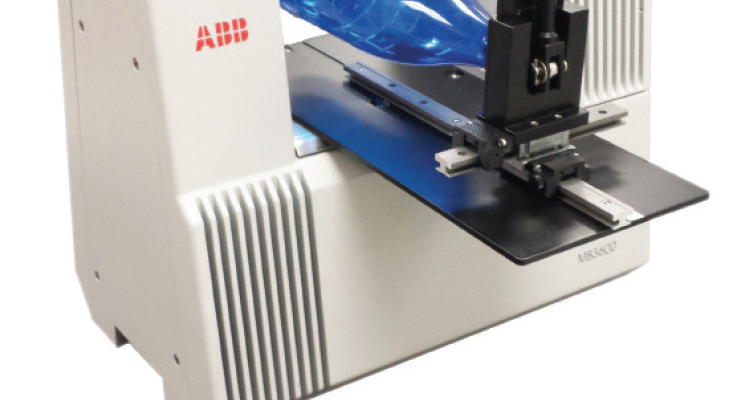
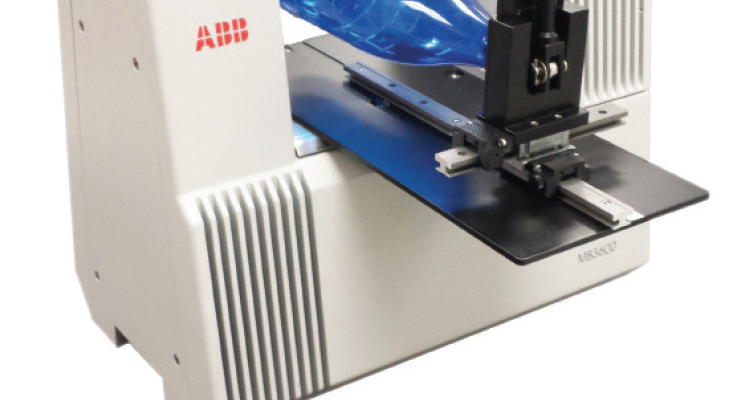
Today’s fast-paced and highly flexible packaging systems demand attention to detail: Much is to be gained or lost in a matter of minutes. At current output speeds in stretch-blow molding each minute may equal to well over 1,000 bottles, all of which need to be up to standards.
Data acquisition and monitoring play an ever more important role in the effort to keep control and improve efficiency. What gets measured may get done – but first the relevant quality attributes need to be identified and the implementation of their measurement has to be made feasible.
With fast, accurate, and non-destructive measurement, Fourier-Transform Near-Infrared spectroscopy (FT-NIR) offers the prospect of matching the testing of important quality attributes of PET packaging material to the production speeds we’re used to.
A part of the puzzle that is often almost taken for granted is the raw material. Several of its quality attributes are crucial in the further performance of a package along all stages of manufacturing, transport, storage, and consumption.
Whilst several laboratory methods exist for determination of important PET parameters such as crystallinity, moisture, intrinsic viscosity (IV) or composition, most of those methods require specialized equipment, time, operator expertise and solvents or reagents for some analyses.
This often leads to infrequent measurement, thus reducing the full potential of a thorough quality check and limiting the understanding of the process. And this is where FT-NIR analysis comes into play.
FT-NIR ANALYSIS BASICS
Near-Infrared (NIR) spectroscopy is a fast and non-destructive analysis technique based on the absorption by a sample of an incident beam at different wavelengths in the NIR region of the electromagnetic spectrum (0.7-2.5 µm or 4,000-14,285 cm-1). The NIR absorptions are caused by vibrations of chemical bonds.
Because of this, NIR provides information on chemical composition of samples, usually liquid or solid. In addition the technique can also provide information on some physical attributes of the sample. It therefore enables multi-property determination on a complex sample or mixture through a single measurement – the NIR spectrum (Figure 1).
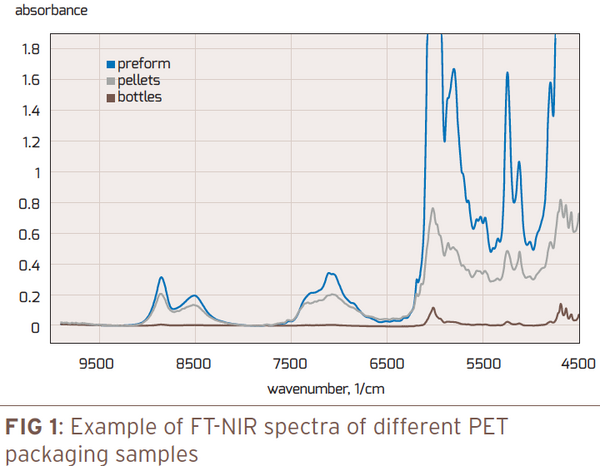
First, an interferogram of the sample is generated using the Michelson interferometer principle [1]. The spectral information is then retrieved by applying a mathematical transformation, the Fourier Transform, to the interferogram.
NIR is a correlative technique that requires preliminary calibration of the analyzer (Figure 2). The calibration step consists in establishing a numerical relationship between the NIR spectrum of a sample and its assay value as measured by a reference method. Once calibrated, the NIR analyzer can be used for routine analysis in place of the more time-consuming reference methods. The analyzer will exhibit similar accuracy (i.e. reproducibility) as the method against which it was calibrated, and will typically provide superior precision (i.e. repeatability) as the technique is free of any operator-related error.
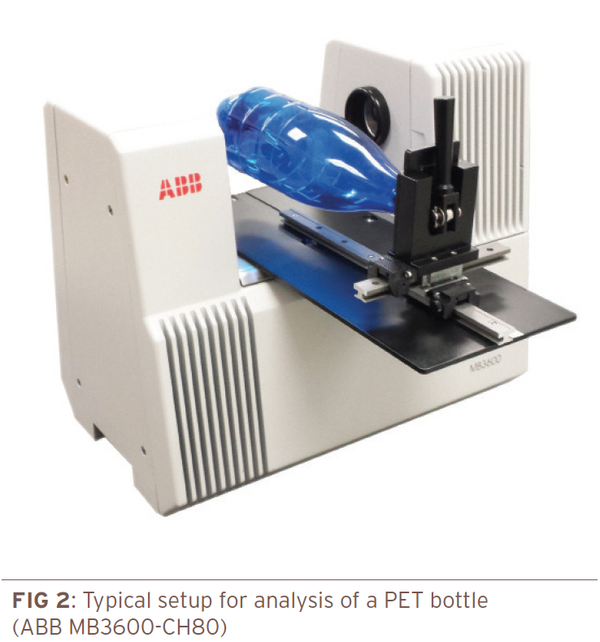
NIR measurements are performed within a few seconds and do not require sample dilution or complex handling. Laboratory NIR measurements can be performed on intact samples by operators with no analytical background. Remote real-time NIR process measurements can also be performed in-situ thanks to the use of insertion probes or cells connected to the analyzer via fiber optics [2].
The first applications of NIR technology a few decades ago were in the field of agronomy. Nowadays, it is widely used in food, chemical, refining, pharmaceutical and semiconductor industries. Its combination of speed, versatility, ease of use, analytical performance and stability has contributed to its success in different industries. The latest generations of FT-NIR analyzers are extremely robust and virtually maintenance-free as they do not require any consumable or preventive maintenance.
REQUIREMENTS ON THE BOTTLE
The requirements for a stretch-blow molded container (Figure 3)
and in consequence also for the PET resin of which it is made derive largely from its contents and the method of filling.
Carbonated beverages build up pressure within the container and thus stress its walls which accordingly need to be stiff and creep resistant.
Microbiologically sensitive beverages are sometimes hot-filled to sterilize the container and closure, these containers need to exhibit enhanced crystallization to yield the necessary thermal stability.
Other microbiologically sensitive products are filled under aseptic conditions. In those cases the container is sterilized either at moderate temperatures before being introduced into the aseptic filling environment or even already stretch-blow molded under aseptic conditions. Those and other containers with non-carbonated contents do not need to withstand high pressures and temperatures and can be very light weight. Yet limitations in injection molding can restrict the preform geometry for those light weight applications which causes high stretching ratios and demands the use of a resin with adequate properties.
For almost all applications, good barrier properties are sought after to meet the desired shelf life of the packaged goods.
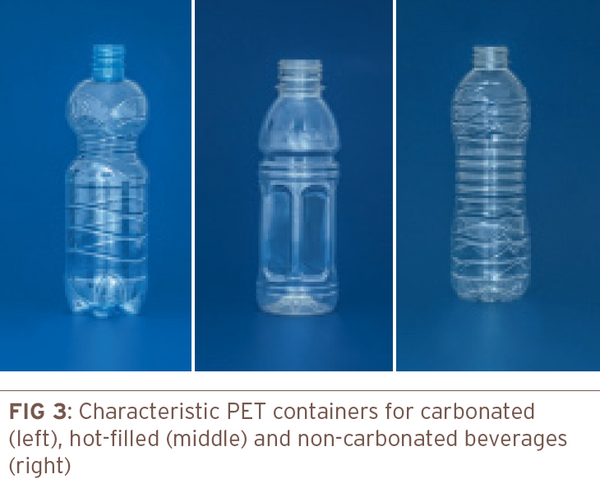
INTRINSIC VISCOSITY
One important characteristic of PET resins is the IV which is a measure for the chain length or molecular weight in polyesters. With higher IV the stiffness and creep resistance of the resin increase which improves for example stability, burst pressure and thermal expansion behavior [3]. At the same time high IV resins will require more energy in processing – both in the form of blowing pressure and heat input. Consequently, high IV resins are typically only used for packaging carbonated beverages.
In contrast, for highly stretched light weight containers intended for non-carbonated contents where mechanical requirements are reduced a low IV resin is utilized. The lower IV can be used because of the lack of container pressurization.
It is important to use the right resin IV for the application to begin with.
The susceptibility of PET to degradation in injection molding affects IV. A minor drop in IV is associated with melt processing, mainly through hydrolysis and thermal degradation [3]. In both cases the result includes shortened polymer chains. Incorrect processing such as improper drying or exposure to high temperatures for prolonged time will subsequently show in an exceptional drop in IV and can be detected this way.
MOISTURE SENSITIVITY
The hygroscopic nature of PET not only entails the risk of hydrolytic degradation in injection molding but also impacts other resin properties directly.
Moisture is readily absorbed from the environment into the preforms. And as a result of increasing water content in the resin, glass transition and cold crystallization both will shift towards lower temperatures. Besides these thermal properties, moisture will also affect the physical properties of PET by reducing orientation and crystallization during stretching, especially when stretching at higher temperatures [4].
CRYSTALLINITY
Crystallinity is another important property of PET and is commonly expressed as the percentage of crystalline phase in the polymer by volume. Its main effects are to enhance mechanical properties and improve thermal stability which also manifests in an increased glass transition temperature. Further, the crystalline structures reduce the solubility of permeants within them and create a tortuous diffusion path around them. This improves the barrier properties of the material [5] [6].
Crystallinity essentially can be obtained in two ways. One is orientation of the resin by stretching where the obtained level of crystallinity for a given stretching ratio is largely dependent on IV, processing temperature, and stretching rate. This is called strain-induced crystallinity. Another option to create crystallinity is by utilizing the cold crystallization of PET [5]. The crystallinity obtained this way is called thermally-induced crystallinity. While sharing many of the same effects as crystallinity obtained by stretching, thermally-induced crystallinity will not generally improve barrier properties [6]. In practice, this second process is able to deliver crystalline fractions above those which can be obtained by stretching alone [7].
COMPOSITION: CO-MONOMER CONTENT
The crystallization of PET and the subsequent crystallinity level in a container is in fact not only determined by its processing and resin IV. The resin formulation contains components which are by-products from the synthesis process or intentionally added during the same: co-monomers, which are another decisive factor in making a PET resin grade suitable for use in a certain application.
Mainly these co-monomers are diethylene glycol (DEG) and isophthalic acid (IPA). Both of those raise the cold crystallization temperature of the polymer and limit both the crystallization speed and the regularity of crystals. Also both DEG and IPA will lower the glass transition temperature. IPA also has the additional effect of improving the barrier properties [3].
Another effect of an increase in co-monomer concentration is a lowered melting temperature which results in a wider processing window as well as energy savings and increased productivity in injection molding.
REHEAT PROPERTIES
In much the same way as in injection molding, the processing window, energy efficiency, and of course productivity are also concerns in stretch-blow molding.
Among many factors, as for example the design and setup of the stretch-blow molding equipment and the relative geometries of bottle and preform, another key point is the heating characteristics of the preform.
Commonly, heating is performed by passing the preforms in front of quartz-halogen lamps which emit to a large extent in the near-infrared spectrum. To allow for fast, radially even and targeted temperature distribution in the preform an infrared absorbing agent can be added into the resin [3]. This increases the portion of infrared radiation that is immediately absorbed into the volume of the preform (Figure 4). As a consequence, heating times are reduced, energy efficiency is increased and the processing window – especially for thick-walled preforms – is extended.
The heating process parameters on the stretch-blow molder will be heavily dependent on the preforms absorption characteristics because of the distinct overlap of affected spectral transmission range and emitter radiance (Figure 4). Consequently, changes upon switching to a new batch of preforms or fluctuations within a batch are undesirable.
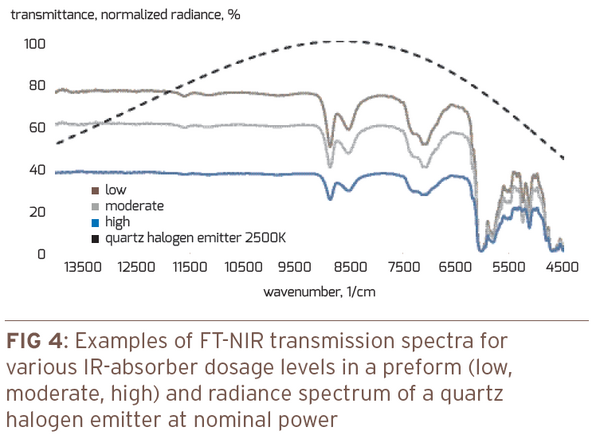
IN A PRODUCTION SETTING
Generally homogeneity and consistency of preforms and environment are key. When looking at the whole production process chain (Figure 5) it becomes clear that any fluctuations could propagate ahead and potentially cause disruptions in production or defects.
From a manufacturing perspective the stretch-blow molding step as the last conversion step, where the PET container first takes shape, plays a central part. It translates between the requirements for further production and functioning of the package and the requirements on the upstream processes of resin and preform production.
Usually both interfaces, namely preform and container, are covered by specifications which define the quality attributes and their respective test methods. Through periodic checks against the specification, production quality is ensured.
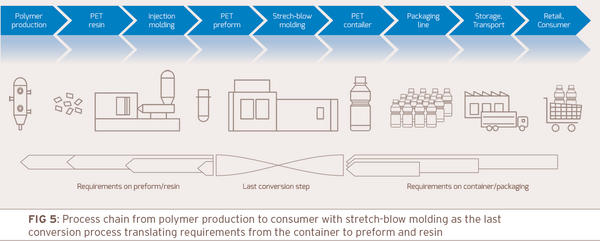
One observation that can be made is that most of the testing relates to the PET containers and only a smaller portion is covering preform and resin quality aspects. Also, while some tests are not connected to significant investments and operator training, others may require specialized equipment, time, repeat measurements to increase accuracy, operator expertise and the availability as well as proper handling and storage of chemicals. As a result, testing frequency is influenced (Figure 6).
Depending on feasibility some tests will be carried out hourly, upon changing formats, once per shift or even less frequently. And with today’s high line output speeds the risk associated with detecting a defect too late is even higher as more and more production volume is handled between measurements.
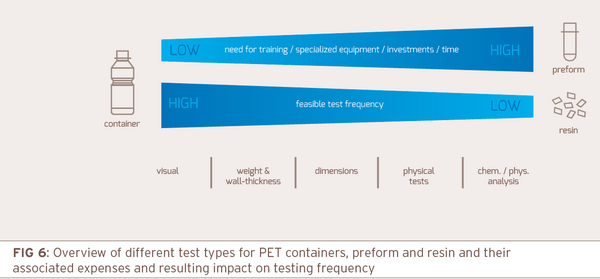
IMPLEMENTATION OF FT-NIR TESTING
A closer look at preform and resin properties has the potential to detect defects that may only become visible after transforming them into a container or further down the production chain. Immediate insight into material properties and processing conditioning on both preform and finished PET containers can enable an improved understanding of the process, providing feedback on the selected process settings or indicating the need to make adjustments.
Once the FT-NIR analyzer has been calibrated against the different reference methods for a set of PET properties, the obvious benefit of its implementation is that it can replace all those reference methods for routine analysis of new samples, for instance in a quality control laboratory.
The technology is modular, an FT-NIR analyser can be initially used in a laboratory for single property determination (often %crystallinity or IV) and later upgraded with addition of new calibration models for additional PET properties, e.g. moisture content. This is done by simply uploading new calibration models in the software and does not require any hardware modifications.
FT-NIR offers an attractive alternative for IV determination as the property relates to sample molecular weight, chain length and conformation and all those factors have an impact on the FT-NIR spectrum. It is therefore possible to measure IV quickly and with relatively low effort with a FT-NIR analyzer, making it viable e.g. as a goods-received inspection technique (Figure 7).
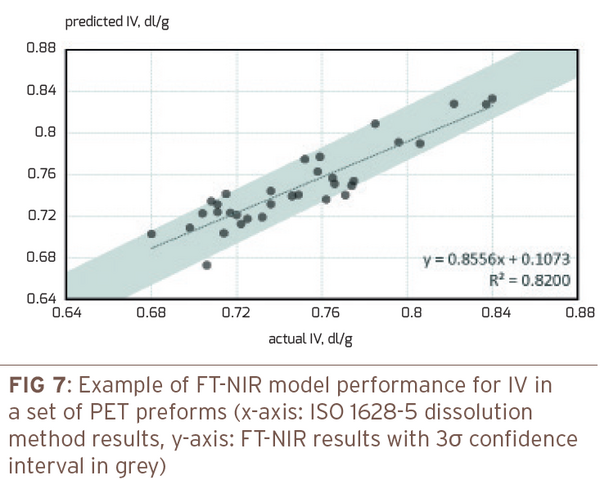
Water in all its forms is a very strong infrared radiation absorber, therefore FT-NIR technology is particularly adapted for the quick, accurate and repeatable determination of small amounts of moisture (from percent levels down to a few hundreds parts per million) in a PET preform sample (Figure 8) or container sidewall.
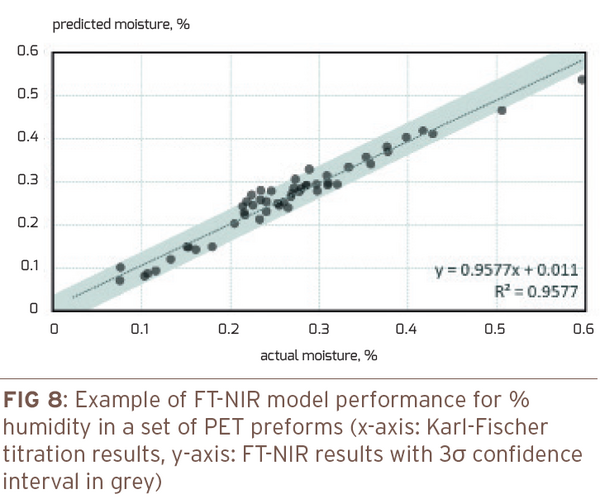
Crystallinity is largely determined by chain length, stereoregularity, presence of polar groups and degree of substitution on the chains. All those effects are present in the FT-NIR spectrum [8]. This enables the fast and simple analysis of crystallinity through FT-NIR spectroscopy, even by an operator without analytical background (Figures 9 and 10).
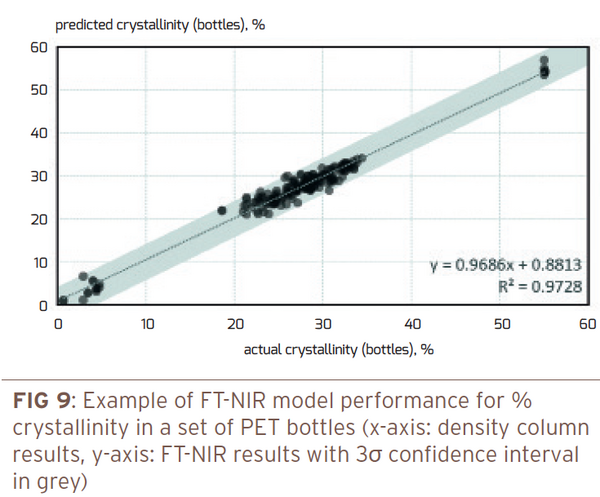
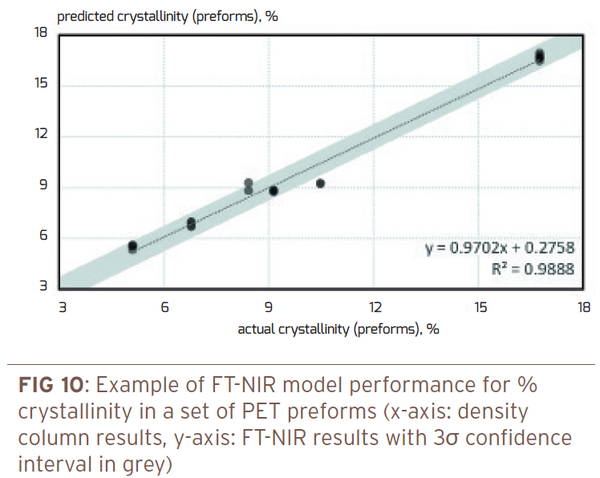
And as an alternative, FT-NIR composition assay on PET samples is straightforward. The FT-NIR spectrum carries qualitative information (the frequency of different absorption bands) and quantitative information (the height of these bands) which can enable precise analysis of the percentage of co-monomers present in a PET sample.
In addition to the multiple PET packaging material properties that can be analyzed with an FT-NIR instrument, the technology also allows for instance to monitor carbonation loss from a container through acquisition of NIR spectra at regular intervals through the headspace of filled bottles [9].
CONCLUSION
The main benefits of FT-NIR technology for PET packaging analysis lie in its unique combination of versatility, precision, and ease of use. Performing routine FT-NIR measurements on a set of PET samples is a simple operation that does not require any analytical background and allows to rapidly determine several key properties and quality attributes of each sample.
Overall, FT-NIR analysis is an environmentally-friendly approach which enables to significantly increase the throughput of industrial analytical laboratories, both in terms of sample volume and also number of property determinations per sample. Thus enabling an enhanced view on the state of the process chain and allowing for its stabilization and further optimization.
The comPETence center provides your organisation with a dynamic, cost effective way to promote your products and services.
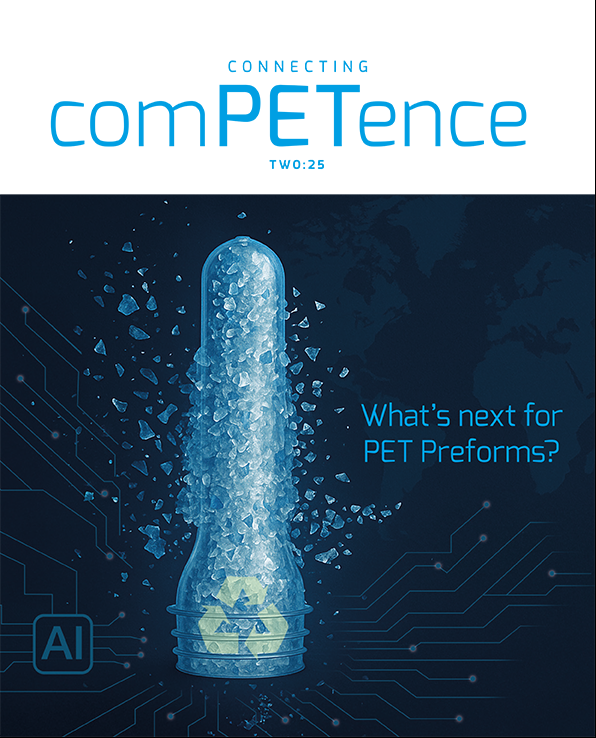
magazine
Find our premium articles, interviews, reports and more
in 3 issues in 2025.