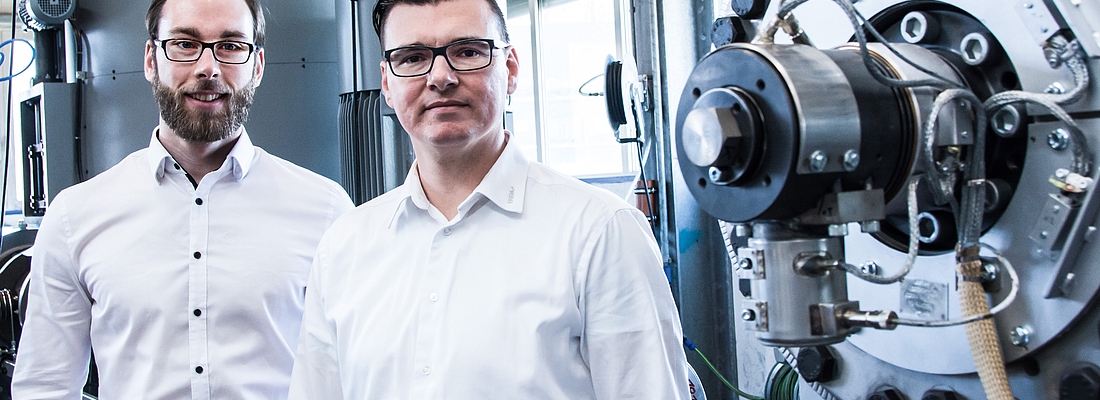
A new demonstration plant for the “bottle to packaging” process will go into operation at the AMUT headquarters in Novara, Italy, at the end of May. It will be used to process washed post-consumer PET bottle flakes directly into food contact grade thermoforming sheet. Interested producers will be able to process their own input material on the demonstration system in the future to make plastic rolls. They can then test the samples later in their own thermoforming production to check the quality.
This new demonstration facility – a direct combination of VACUREMA® technology and the AMUT Inline Sheet plant – can be used immediately to make food contact grade thermoforming sheet in just one process. This shows that the realisation of the desired closed material loop in the PET sector is already happening. Energy saving, maintaining the IV value and lower logistics and process costs in the sense of higher profitability are driving the trend towards direct processing. Thanks to the direct combination of recycling and production technology there is no longer any excess process stage. This is because the melt goes straight from the VACUREMA® without cooling stage to the AMUT plant without the detour of pelletising.
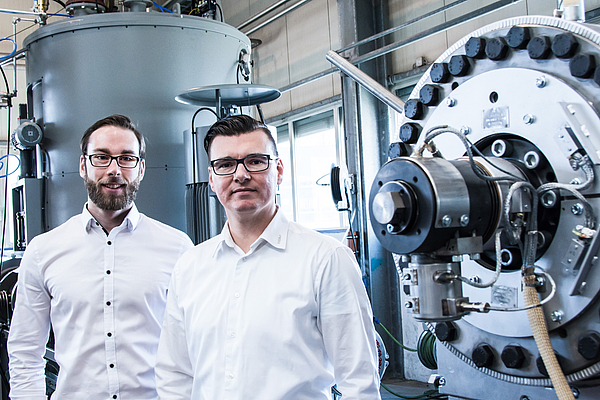
Fig. 1: Michael Buchberger, Sales Manager, and Christoph Wo?ss, Business Development Manager for the Bottle sector at EREMA, in front of the VACUREMA® in the production hall. EREMA‘s VACUREMA® technology is in use on over 60 Inline Sheet facilities around the world.
100 PER CENT PET FLAKES WITH 100 PER CENT FOOD CONTACT APPROVAL
The post-consumer PET material is already decontaminated and pre-dried prior to extrusion in the vacuum reactor of the 1714 VACUREMA® Basic T, with a throughput of up to 1,000 kg per hour. This means that neither additional predrying nor additional extruder degassing is necessary. Thanks to the direct transfer of the pretreated flakes from the reactor into the extruder the VACUREMA® system works with reverse degassing and the melting takes place under vacuum. The clear benefit is the colour-retaining treatment of the material. The omission of degassing enables you to subsequently use a short extruder (on average 40 per cent shorter than models from other suppliers). This means a shorter melt phase which in turn counteracts material loss.
The melt is then transferred immediately to the newly developed EREMA PET Laser lter. It is here that input material with a degree of contamination of over one per cent is processed without any difficulty and the filtered particles are discharged continuously. Thanks to its unique pressure consistency this filter system is particularly suitable for inline production. Despite varying moisture, IV values and bulk densities in the input material, the melt has a constantly stable IV value and colour. Additionally, the process stands out through what is only a marginal IV drop. The melt then goes directly into the AMUT Inline Sheet plant where it is processed into thermoforming sheet.
The integrated online viscometer shows the user the actual viscosity of the melt. The high-hardness cooling rolls with a net width of 1,200 mm guarantee exact material guidance with a cooling capacity of up to 1,200 kg/h. Another boost in sheet quality comes from the fully integrated inline thickness gauge control. The hot lamination system represents an additional production benefit and is particularly suitable for sensitive barrier lm thanks to the adjustable contact point. The wet coating at the end makes for an antistatic and antiblocking solution. At the end of the production process the sheet is put on rolls at a single/double winding station.
The clear advantage of the VACUREMA® and AMUT system: the monolayer thermoforming sheet produced from pure rPET is not only 100 per cent food contact compliant, it also ful ls FDA regulations and EFSA guidelines.
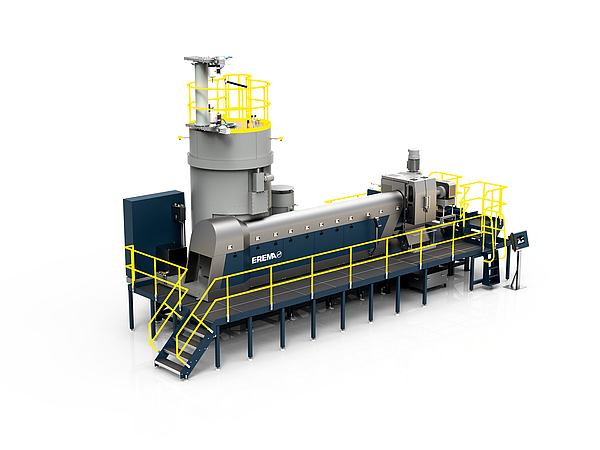
DECISIVE ARGUMENTS IN DIRECT FOOD CONTACT
rPET sheet produced using VACUREMA® technology has a decisive advantage over conventional ABA multilayer sheet: it is 100 per cent food contact compliant and can thus be produced as a pure monolayer sheet. A costly A level with virgin material is not necessary. There are, however, cases where ABA multilayer sheet is chosen deliberately instead of monolayer sheet – for example because the application requires the use of colour/antiblock additives and the ABA structure of the sheet helps to save production costs.
Additives are typically usually used only in the two A layers and the middle layer (B) remains free from these very often costly additives. With regard to food contact compliance, however, this ABA structure is problematical if the middle layer (B) does not consist of food contact grade rPET. The reason, according to a study published by the Fraunhofer Institute : this structure has no effective barrier layer.
In order to achieve thorough food contact compliance, the middle layer (B) also has to be food contact compliant in this case.
NEXT STEP: RECYCLING THERMOFORMING PRODUCTS
The end of China as an international customer for post-consumer plastic waste, the strategy for plastics presented by the EU Commission and initiatives such as the Ellen MacArthur Foundation are just some examples of the rapid rise of the circular economy. This new approach of recycling rather than incineration is becoming more and more apparent in the inline sector: the Netherlands has set an example and other European countries plan to establish their own collection systems for post-consumer thermoforming products. The brittle structure, increased nes, lower IV value and the coming together of different multilayers are just some of the challenges facing the recycling process. Providing there is special treatment in the sorting and washing process, the most important recycling requirement is without doubt increasing the IV value in the course of extrusion. With the VACUREMA®
Advanced/Prime design the IV increase of the very dusty input material does not represent a problem. The IV value is raised to the point where the mechanical properties of the end product in terms of tensile strength or stiffness, for example, are ensured. These play a key role in the rPET sheet thermoforming process. As it is possible to upgrade VACUREMA® systems, existing EREMA customers will also be able to switch to thermoforming recycling in the future.
The comPETence center provides your organisation with a dynamic, cost effective way to promote your products and services.
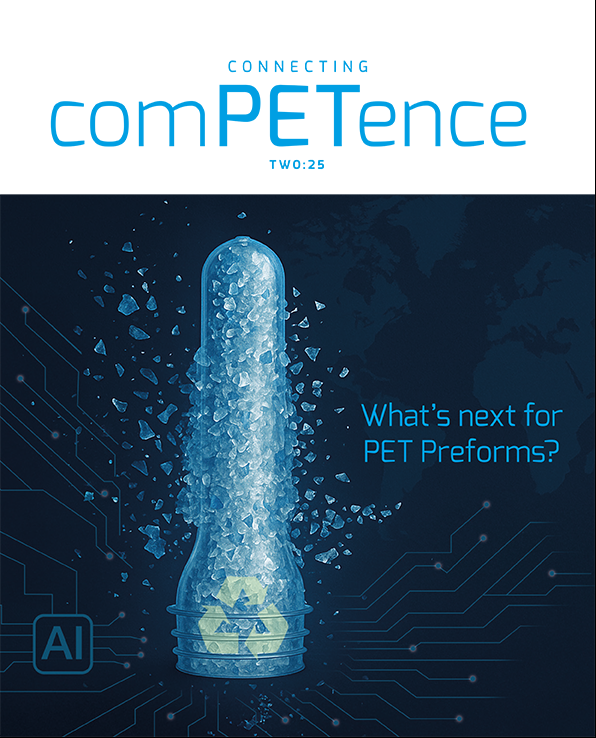
magazine
Find our premium articles, interviews, reports and more
in 3 issues in 2025.