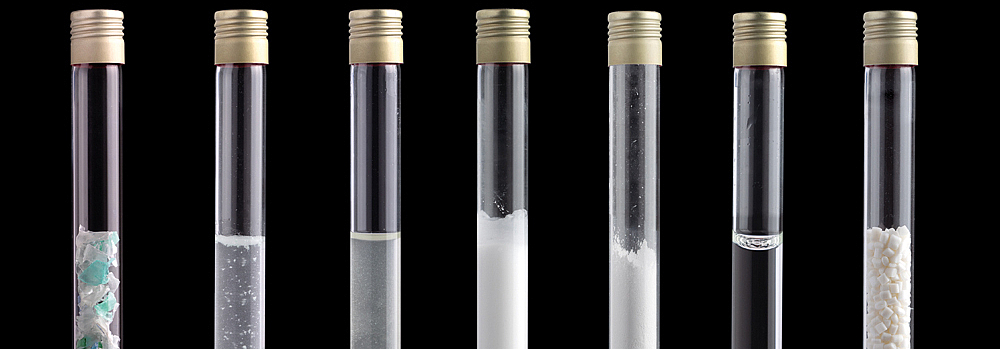
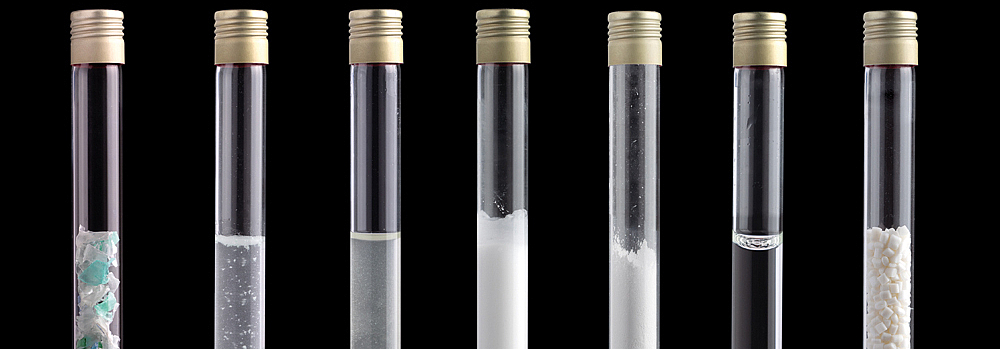
(Photo credit: Jérôme Pallé)
Recycling
Enzymatic recycling: CARBIOS inaugurates industrial demonstration plant - Scalability • License concept • Unlimited recycling
On September 29, 2021, we were invited to attend the opening event of the industrial demonstration plant in Clermont-Ferrand / France. Carbios pursues two goals on the installed system: validating the efficiency of its enzymatic recycling process and developing the specifications for future plants on a large industrial scale.
More than ten years of development work have gone into the C-ZYME® technology*. With the formation of a consortium around Carbios in April 2019, consisting of L’Oréal, Nestlé Waters, PepsiCo and Suntory Beverage & Food Europe, Carbios received support from the industry. In the same year, L’Oréal and Michelin acquired shares in the company and, more recently, L’Occitane, which now hold 5.91%, 4.36% and 2.36% of Carbios’ capital, respectively.
The commissioning of the demonstration system marks the cumulation of the C-ZYME development. It represents the last step before commercialization.
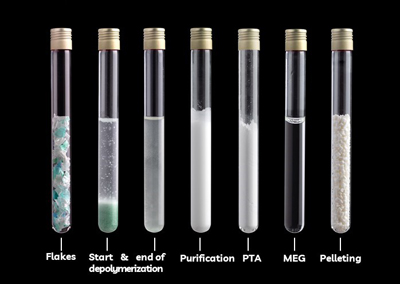
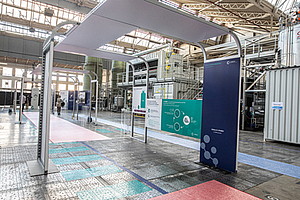
The C-ZYME® recycling process uses an enzyme that is capable of depolymerizing the macromolecular structure of PET. The depolymerized monomers are purified in the technical process before they are repolymerized into PET. According to Carbios, the quality of the rPET material obtained by enzymatic recycling is comparable to that of virgin PET material. Carbios promises unlimited recycling of all types of PET waste - clear, colored, opaque, complex plastics, polyester textiles - as well as the production of 100% recycled and 100% recyclable PET products that retain their original quality throughout.
In a first step, PET waste (flakes, textile or else) are fed into an extruder and converted into expended pellet shape. Under the prevailing process conditions and process engineering sequence in the extruder, the granules are melted. The process step prepares the PET waste in such a way that the enzymes in the subsequent depolymerization process can take up their work in the polymeric PET structure and carry out the depolymerization effectively: Over a residence time of 10 hours in the reactor, the enzymes convert the polymeric material into monomers.

Quick questions to Martin Stephan
You call the separated impurities, including the enzymes, “cakes”. What happens to them?
Martin Stephan: The “cake” is composed of residues that are mainly not PET. To date, it is incinerated but we are working on finding a better end of life for this waste in our scale up.
What is the elationship between the input quantity and the repolimerization feedstock obtained? Specifically: How many PET bottles can approximately be produced from 100,000 bottles input material (cycle capacity) if the bottle size and weight are identical? Or to put it another way: how high is the loss?
As we are depolymerizing 90% per cycle, 90.000 bottles could be recovered from the isolated monomers. In other words, there is a high yield with only a small loss.
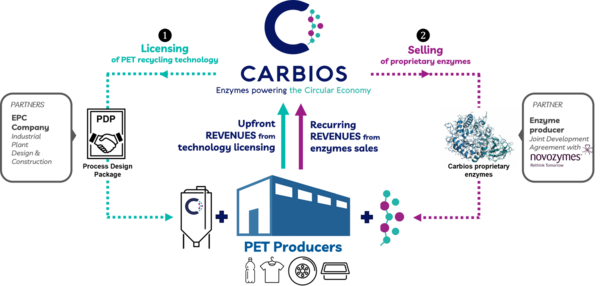
The resulting green-colored liquid is decolorized and purified in the subsequent hydrolysis in several steps. The separated impurities, including the enzymes, are discharged in the process as so-called “cakes”. The resulting monomer batches PTA and MEG are the starting material or feedstock for the repolymerization.
A team of 10 people is now responsible for producing the monomer batches on the demonstration plant and optimizing the operating parameters. They also take care of the technical and regulatory validations to ensure the defined specifications and quality features for future licensees. An initial hydrolysis has been successfully realized, which confirms that the process can be scaled up.
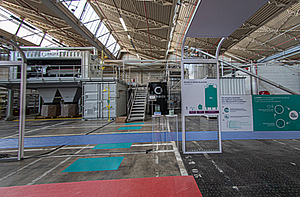
The repolymerization process step, taking place via solid-state polycondensation, is not part of the demonstration plant.
The depolymerization reactor has a capacity of 20m3 and can process around 2 tons of processed PET granulate per cycle, which corresponds to about 100,000 PET bottles.
In the next few months, in addition to the validation and process optimization, Carbios will create - using the PDP Process Design Package - the complete technical drawings and documentation required to design and construct future industrial plants. The work shall be completed by the end of 2022. C-ZYME® plants can then be operated under license.
''The continuous cycle of recycling PET waste is one step closer to becoming a reality!'' - Jean-Claude Lumaret.
The capacity of the industrial plants is estimated at 40,000 tons per year.
In his inauguration speech, Jean-Claude Lumaret, Chief Executive Officer of Carbios, said: “The continuous cycle of recycling PET waste is one step closer to becoming a reality!”
After the speeches by dignitaries from business and politics, the guests visited the demonstration facility.
_______________
* C-ZYME is a registered trademark in France and internationally
The comPETence center provides your organisation with a dynamic, cost effective way to promote your products and services.
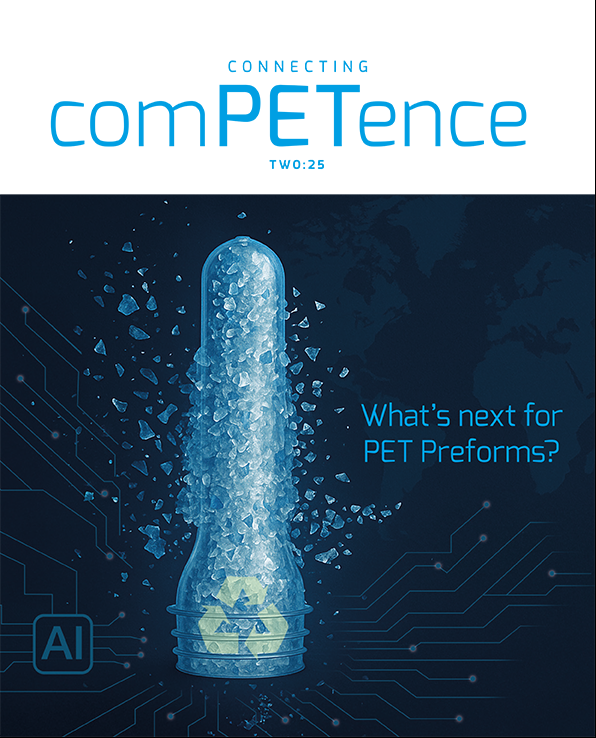
magazine
Find our premium articles, interviews, reports and more
in 3 issues in 2025.