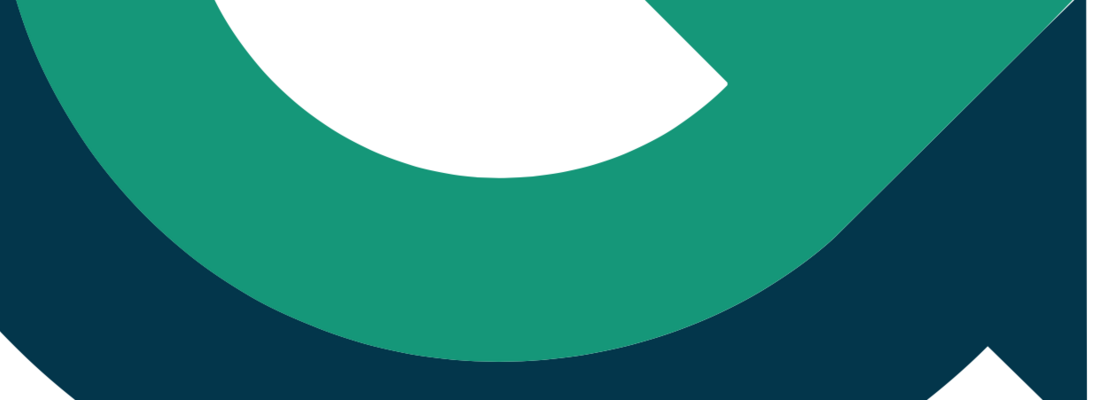
In the field of auxiliary equipment, Eisbär manufactures systems to improve quality and productivity for the plastics industry focusing on customer requirements and energy-efficiency. Our product range is including systems for cap cooling, drying of plastic resin, processing PET flakes, crystallization, mixing and dosing as well as to avoid condensation on cooled moulds.
CONSEQUENCES OF CONDENSATION ON COOLED MOULDS
Top priority of injection moulding is the production of high- quality plastic parts with the highest degree of accuracy in the shortest possible cycle times. Short cycle times save time and money! An essential part for optimal operation of injection moulding equipment is mould cooling.
If the surface temperature of an object sinks below the dew point of the ambient air, condensation builds on this object - like taking a chilled bottle out of the fridge on a warm day. This problem specifically appears on cooled moulds of plastic processing machines. For this reason, the optimum of the mould cooling process cannot be realized. The cooling temperature has to be increased to avoid condensation and subsequently to prevent watermarks and other quality- degrading effects – no favourable production conditions!
Eisbär offers the energy efficient and right solution to avoid condensation.
PERFORMANCE IS IN THE AIR
Air affects our life at any time - it can be hot, cold, humid, dry etc. It is obvious that the properties of the process air significantly influence the productivity and quality of injection moulding. Thousands of Eisbär DAS systems for mould dehumidification are in daily use at our customers from all over the world to ensure optimal production conditions. Performance is in the air - this is the primary focus of Eisbär!
The heart of all Eisbär products for drying the air is a desiccant wheel positioned inside our systems. A type of honey combed structure designed to retain humid air very efficiently. One part of the wheel dehumidifies the processed air – other segments regenerate the wheel while operating in a continuous process. The saturated adsorption wheel is regenerated at low temperature.
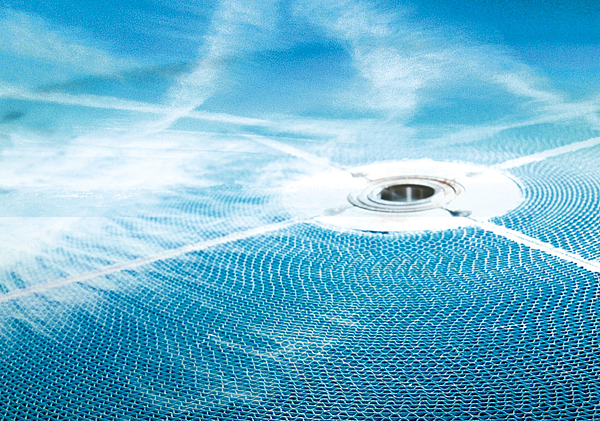
NEW GENERATION – EISBÄR DAS-K
The new generation of the Eisbär DAS-K adsorption dryers are specifically designed to prevent condensation on cooled moulds with the lowest possible energy consumption. The system offers no limits regarding ambient conditions and low mould temperatures using a closed circuit for continuous and rapid drying of the process air. The adsorption drying technology offers user-optimized design and easy maintenance. The continuous drying process, low energy consumption and long life are basic advantages of the system to ensure the optimal mould cooling process.
The Eisbär DAS-K series is a highly effective solution to prevent condensation on cooled moulds. Watermarks and other quality-degrading effects belong to the past! More than 500 DAS-K systems are in daily use at our customers from all over the world.
Overall, the Eisbär DAS-K system brings highest efficiency in production combined with limited requirement for maintenance - an all-round carefree package.
EXPERIENCE AND KNOWLEDGE
Our experience as an established manufacturer with extensive practical knowledge and focus in understanding the customer requirements is our outstanding strength.
The customer therefore has a flexible partner with Eisbär for new, competitive and energy-efficient tailor-made system solutions. Another important Eisbär competence is digitalisation and clearly structured visualisation as well as data connectivity of all operational data for efficient control and maintenance.
The comPETence center provides your organisation with a dynamic, cost effective way to promote your products and services.
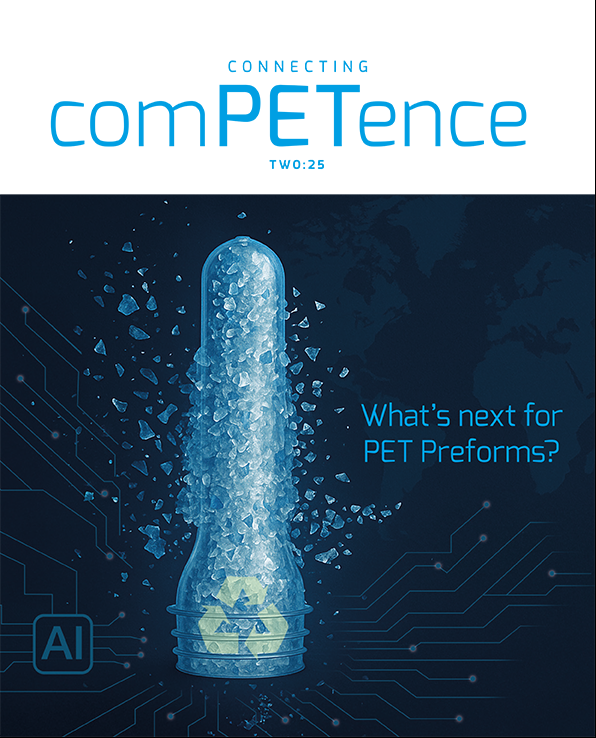
magazine
Find our premium articles, interviews, reports and more
in 3 issues in 2025.