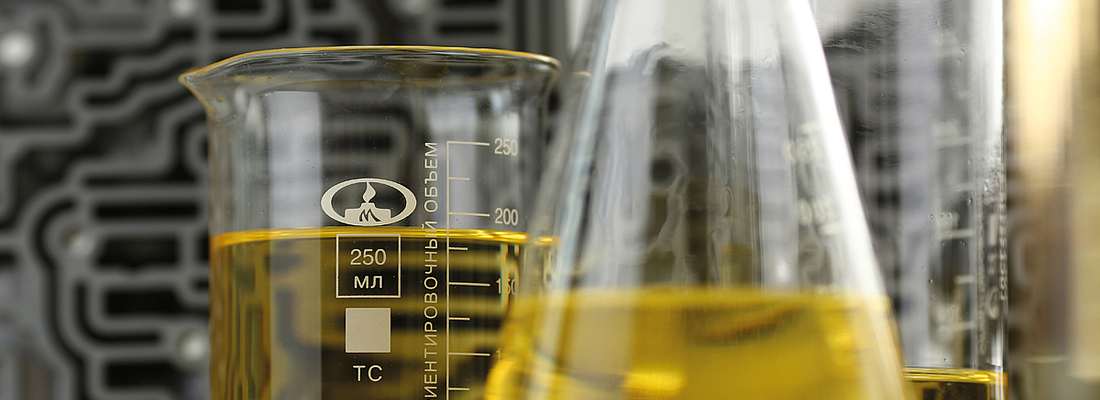
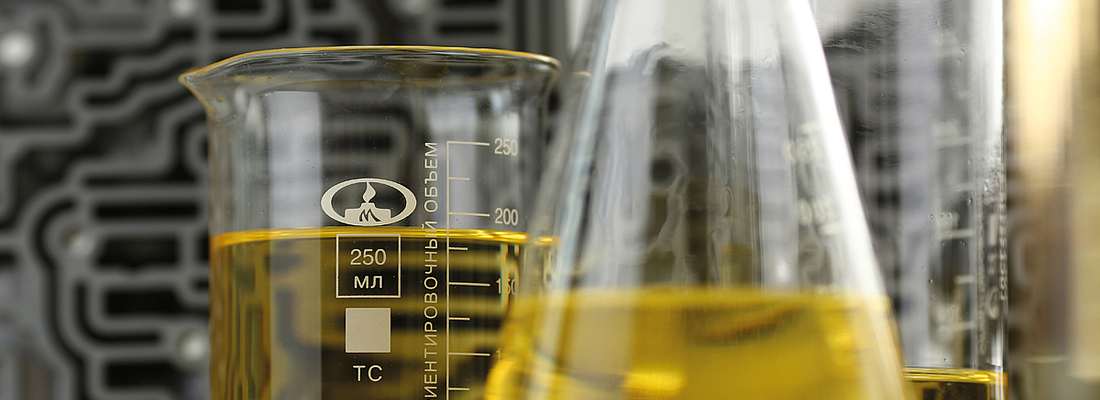
Similarly to the Middle-Age alchemists, which failed in their pursue of the Philosopher’s Stone dream but established the basis of modern chemistry, twenty-first century “alchemists” are working today to convert discarded or littered waste into one of the “golden materials” of our time: Renewable and sustainable plastics. Using the latest scientific approach and state-of-the-art technologies, success is now at hand.
PET is a wonderful plastic, with excellent properties which preserve health and nutritional ingredients of food and drinks. Unfortunately, it is under the spotlight of press, social media, NGO and governments, which blame it for ocean pollution, plastics littering and global warming. The way to address these issues has been known for years: RECYCLING. Its chemical nature makes PET an ideal candidate for reprocessing in a “circular” way, without downgrading the product to prevent littering and waste, to save energy and to reduce greenhouse gas emission.
European Union PET framework
Recycling is one of the key PET success stories, with more than half of the PET worldwide bottles being currently collected. In the European Union, postconsumer PET bottle collection rate is 55%. But 2.4 million tons of PET per year are not collected for recycling in Western Europe; this includes almost half of the normal bottles, most of PET sheet (thermoformed trays) and all the Opaque and Difficult to Recycle (ODR) bottles (black, white, multi-layer, multi-material). Two thirds of all PET products are wasted, littered, landfilled or incinerated causing harmful CO2 emissions.
The new Single Use Plastics (SUP) EU Directive raises the bar for the European PET industry:
- Mandatory collection target of PET bottles will raise to 77% by 2025 and to 90% by 2029, (current average level: 55%);
- A minimum recycled content in PET bottles of 25% is mandatory for 2025, increased to 30% for 2030 (current average level: 11%).
Established “bottle to bottle” recycling systems are based on the “Thermomechanical” concept: hot-washed PET flakes are processed in an extruder and in a system to partially rebuild the broken polymer chains. With this approach alone, it will not be possible to reach the minimum rPET target content of 30% bottles. Thermo-mechanically recycled rPET is inferior in quality to virgin PET, as more recycled content is added into bottles and as PET is cycled more times; also, many of the bottles are colored, which cannot be reverted to clear PET by mechanical means. And finally, the increasing presence of trays way and ODR bottles boosts the waste from the recycling processes.
Chemical recycling of PET
The alternative to allow PET packaging to keep growing and to meet the recycled content targets is to take advantage of the beauties of the polyethylene terephthalate molecule: using chemical reactions to break down bottles, thermoformed sheet and other polyester materials such as textiles into its pure monomers, oligomers or primary raw materials. Those will become the “building blocks” for new PET molecules that will perform identically to conventional petrochemical precursors, allowing an endless loop of PET reuse and making PET part of a “Circular Economy”.
Although some PET chemical recycling processes date to decades back, they are of little relevance on an industrial scale because costs (investment and operations) are higher than the thermo-mechanical ones. But the new sustainability standards and the development of breakthrough technologies are going to change this situation. To meet the Single Use Plastics directive requirements in the EU, 600,000 tons/year of chemically recycled PET might be needed in 2025, which may increase to 800,000 tons/ year by 2030.
There are four basic ways to commercially achieve this, which will be presented in order of difficulty (easiest to most challenging).
“Melt-in” or “Semi-chemical” recycling
Most existing PET resin plants can be modified with low / medium CAPEX to produce a resin with 10 to 50 % rPET content. This is a variation of glycolysis and is classified as “chemical recycling” by EFSA and FDA, so there is no need to present a Dossier for food-contact approval. In the “melt-in” process, flakes or rPET granules are incorporated into a polymerization plant, mixed with virgin raw materials. These resins have been commercially available in Western Europe for years by EQUIPOLYMERS (10% rPET content) and JBF (25% content). Melt-in recycling offers good conversion cost, low energy usage and low carbon footprint. The main drawback: It needs very high quality clear/light blue flakes (expensive), so it competes in post-consumer bale sourcing with bottle to bottle thermo-mechanical recycling. It can handle mono-material PET trays, but not colored or opaque bottles and is very sensitive to non-PET plastics contamination.
Glycolysis
In the standard glycolysis concept, PET is reacted at high temperature with an excess of glycol. The final product is PET’s monomer (BHET) and low molecular weight oligomers. BHET is purified by melt filtration under pressure or with special distillation processes and is relatively easy to re-polymerize into PET or textile polyester. Glycolysis can treat textiles and packaging products, although it will face difficulties with colored, opaque, multilayer or multi-material bottles. There are several glycolysis plants operating on industrial scale (mostly in Asia), processing PET bottles and textile waste, for conversion into fibers and yarns. Among the technology licensors, there is perPETual (UK based) and Jeplan (Japan). Other glycolysis processes not yet available in commercial scale are Garbo (Italy), Cumapol (Netherlands) and a very novel technology – using magnetic fluids as solvent – from Ioniqa (Netherlands).
Methanolysis
Methanolysis is the oldest chemical recycling technology. Developed by EASTMAN Chemical decades back, reaction of PET with methanol produces dimethyl terephthalate (DMT), which is re-polymerized back to PET. DMT can be purified by distillation to remove contaminants.
As there are no PET plants in the world using dimethyl terephthalate as feedstock, for Methanolysis to succeed either DMT must be converted to purified terephthalic acid – PTA – (feasible, but costly) or polymerization plants need to be modified to accept DMT instead of PTA (practicable, but expensive in capital and in operation costs). DMT is dangerous to handle, and its polymerization generates crude methanol as by-product. That said, there is a recent development by Loop Industries (Canada) that claims that a solvent assisted Methanolysis can produce competitively priced DMT and mono-ethylene glycol (MEG) for 100% rPET polymerization, and that its low temperature process can handle impure and mixed plastics streams.
Hydrolysis
Hydrolysis is a more complicated chemical process, which seeks to break the ester bonds in the polyester chain. The result will be the two raw materials of PET (PTA and MEG) which, once purified, can substitute their equivalents of petrochemical origin. This is a “drop-in solution”, where any PET polymerization unit can switch seamlessly to 100% recycled feedstock, without modifications.
Among the hydrolysis technologies studied there are neutral hydrolysis (with water, requires high pressures and temperatures), acid hydrolysis and hydrolysis in a caustic medium (saponification). The latter is the one which may offer the best feasibility since its intermediate product, sodium terephthalate, is soluble in water which facilitates its separation from other contaminants. The by-product is the sodium sulphate salt.
Hydrolysis reaction can be done under pressure at high temperature or, via some new technologies under development – such as Carbios’ (France), by enzymatic catalysis. In this case, 90% depolymerization is achieved in 10 hours at temperatures below 70° - see Figure 1. Given the high selectivity of the enzyme, only PET reacts, and PTA and MEG will dissolve into the reaction water, while most of the contaminants and other plastics will remain at the bottom of the depolymerization reactor, from where they can be separated.
There is another hydrolysis process being developed by Gr3n (Italy), which uses microwaves to induce and catalyze the PET depolymerization process.
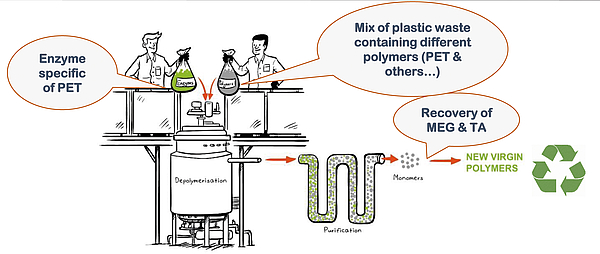
Comparison of recycling technologies
Figure 2 displays different PET recycling technologies in a “Pyramid of Difficulty”, the easiest one at the bottom (mechanical recycling) and the most difficult on top (Hydrolysis). Figure 3 gives a score (in a scale 1 to 4) to the Capital to build a plant (CAPEX), conversion cost (OPEX), Carbon Footprint impact and flexibility to use any feedstock (highest score meaning ability to use mixed plastics, color and opaque bottles, multi-layer trays, etc.).
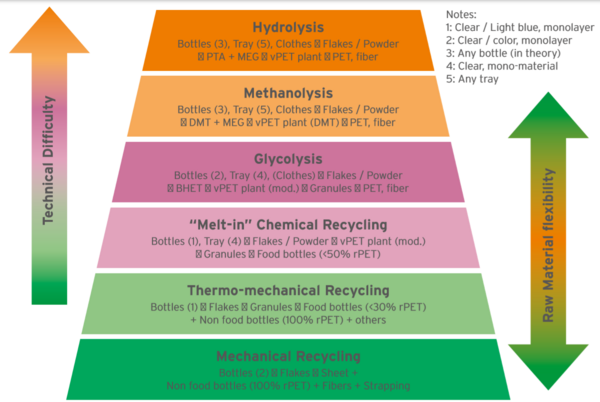
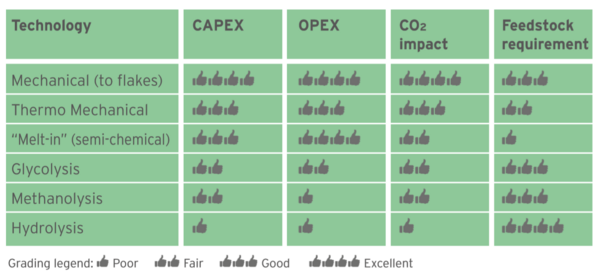
Scaling up of PET chemical recycling
One challenge faced by chemical recycling is the need to scale up quickly, to benefit from economies of size and to achieve low conversion costs. Current world-class PTA plants are built for 1.2 million tons/year, while the typical size of today’s PET site is at least 400,000 tons/year. New chemical recycling technologies are currently in the late pilot plant stages, or in the “demonstration plant sizes”, usually in the range 10,000 – 20,000 tons/year. To convert recycled monomers back into resin, small PET plants will be needed during the first years. These units are neither energy nor cost-efficient. A polymer plant using DMT (from Methanolysis) will have a conversion cost three times higher than the best PET virgin plant. A small polymerization unit using BHET or PTA + MEG from hydrolysis will have a cost twtimes higher than the one from the best conventional plant.
It may take some decades – and a big development effort - to design and to build large size depolymerization plants, so that industrial costs of chemical recycling approach those of the petrochemical route.
Environmental aspects – Carbon Footprint
Focusing on the greenhouse gas effect (carbon footprint), Figure 4 compares different technologies when allocating to chemically recycled PET a positive credit for 33% of the PET combustion carbon, because this avoids incinerating PET waste. Thus, chemical reprocessing of PET proves to be among the lowest carbon impact solutions to minimize global greenhouse gas effects from polyethylene terephthalate.
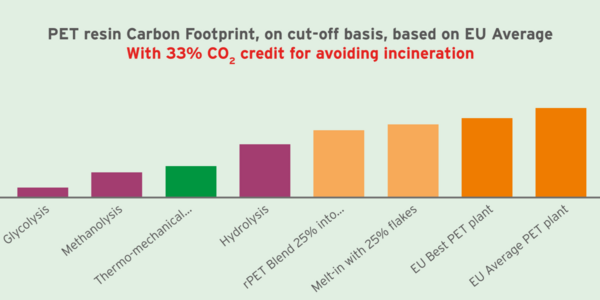
In conclusion
Chemical recycling will be the best way to sustainably revalorize high volumes of PET which cannot be recycled otherwise. However, the following factors must be considered:
- Energy consumption and conversion costs from a chemical recycling plant are higher than for production of virgin PET or for thermo-mechanical recycling;
- The chemical process must use cheap waste PET feedstocks. Ideal candidates are thermoformed sheet, colored or opaque bottles, fines from mechanical recycling, mixtures of plastics and textile waste. The involvement of Material Recycling Facilities (MRF) and of organizations that manage collection and treatment of waste is fundamental;
- Purchasers of chemically recycled PET must pay more for recycled polymer than for virgin plastic. Or, alternatively, legal and fiscal incentives must be deployed to favor recycled PET;
- Economies of scale are very important. Assessments must be done to find the optimal size of the recycling plants, considering also integration upstream (co-location with waste collection centers) or downstream (co-location with PTA or PET manufacturers);
- Investment needs for a chemical recycling plant are much higher than for thermo-mechanical recycling.
There will be no clear winner in the race for successful PET recycling. All technologies, from humble wash-lines to high-end bio-engineered enzymes processes may find its niche to thrive in the future PET circular economy.
And let’s not forget that, worldwide, rigid PET packaging is 1/4 of the total polyethylene terephthalate usage. The other 3/4 are mainly textiles (and flexible packaging), which are currently not recycled, and which cannot be mechanically reprocessed. Therefore, the window of opportunity for future chemical recycling of PET and polyester is enormous.
__________________
K-PET CONSULTING
Based in Barcelona (Spain) and operating Worldwide, K-PET Consulting offers specialized services and products to the PET and polyester chain, including know-how for special product manufacturing such as PETG, recycling technologies, manufacturing technical support for virgin and recycled products, and procurement and sales of PET, rPET and special polyester resins (info@kpetconsulting. com, www.kpetconsulting.com).
The comPETence center provides your organisation with a dynamic, cost effective way to promote your products and services.
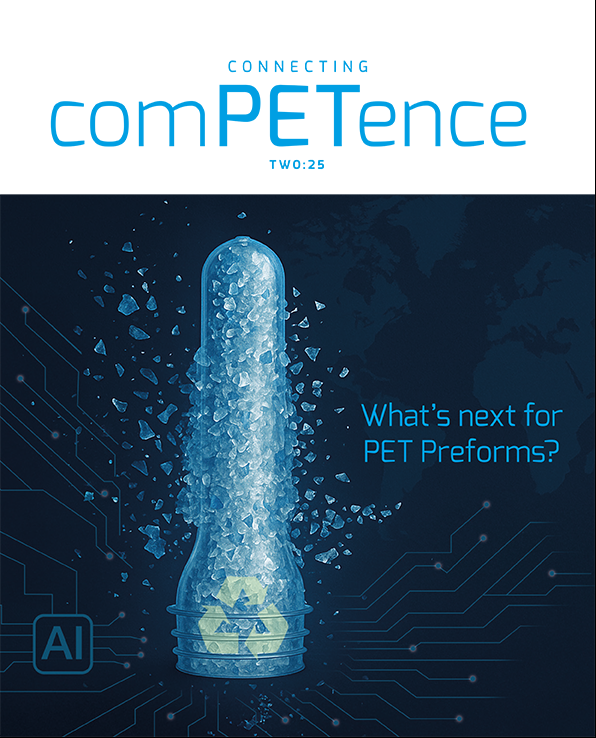
magazine
Find our premium articles, interviews, reports and more
in 3 issues in 2025.