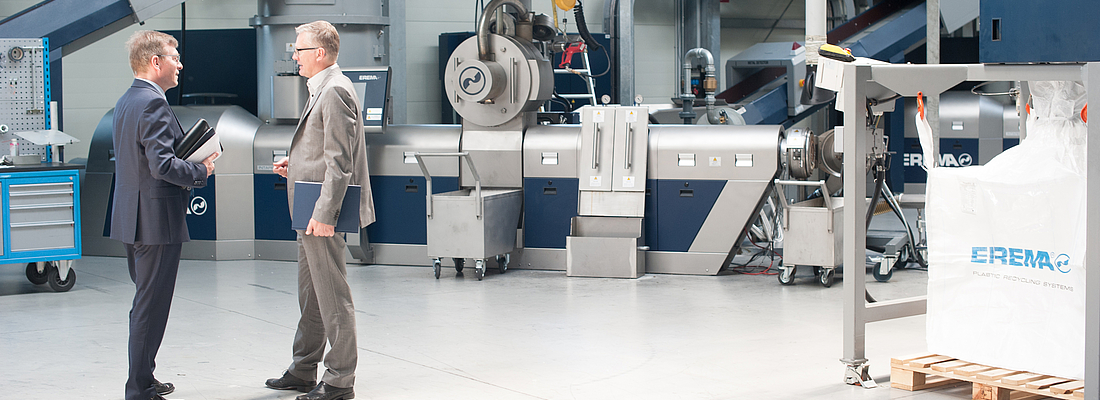
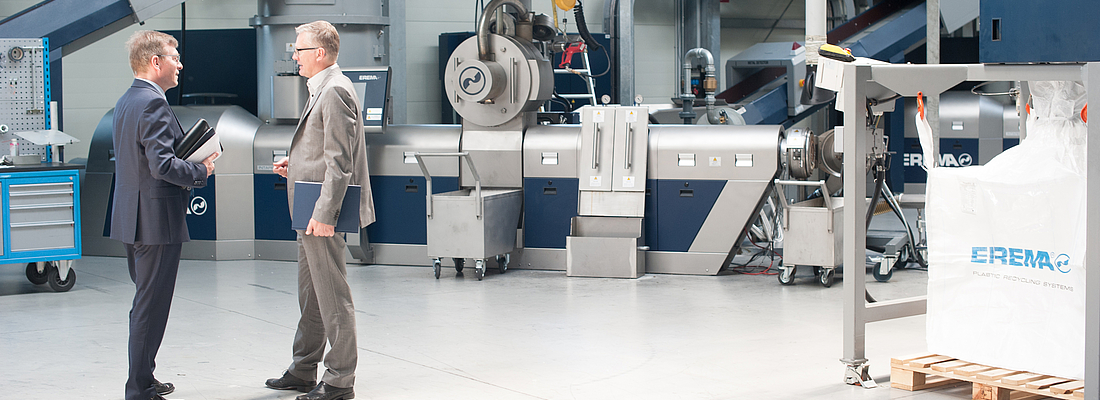
Manfred Hackl, CEO, EREMA about Recycling – Technology, Markets, People
Mr Hackl, on the EREMA website it says “EREMA: efficiency in plastics recycling”. What does this mean to you personally in terms of the company’s claim?
Better and higher-performance technology is our driving force and this is what we have been working on – with focus, perseverance and team spirit – for over 30 years. Technologies which are flexible enough to adapt to ever changing conditions in recycling and especially to the wide variety of input materials. I think this is what has made us the clear number 1 in plastics recycling plant engineering.
EREMA achieved an increase in turnover of 21% in 2014. What were the main reasons for this positive development?
This growth is primarily due to our new plant generation INTAREMA®. The sales figures – over 250 in the past 18 months – confirm that this innovation is an attractive technology for customers. The stability of the system is above average – it is unparalleled in the market. Plus: with VACUREMA® we are the market leader in the USA and in Europe our market share is in the region of 30%.
Where are EREMA’s markets in the medium term?
We are basically of the opinion that the potential is there on a global scale. This varies in size, of course, according to the continent and application – whether it is in-house recycling, post-consumer recycling or bottle recycling. If we take a look at Europe: European legislation, landfills banned – the material has to go somewhere. Recycling is becoming increasingly important in terms of this aspect alone.
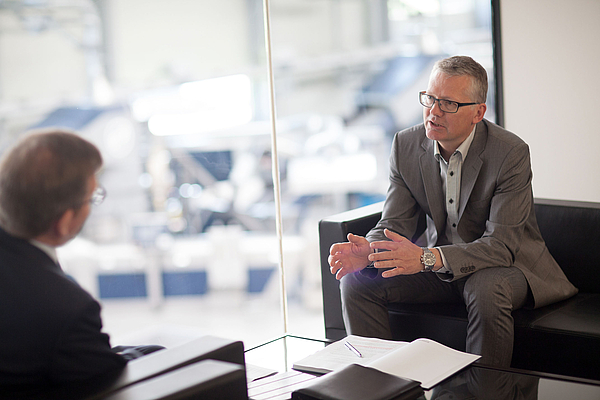
Forgive me for interrupting: you said the material has to go somewhere. Does this mean that additional sales channels are necessary for the recycled pellets which are produced?
Yes, we need new sales markets. The entire value chain and, moreover, a lot of creativity is called for here. The goal has to be as far as possible autonomous supply through closed plastics recycling loops. I see, for example, that regrind from thick-walled packaging and from the automotive and electronics sector is becoming increasingly important as material flow. EREMA has hardly been active until now in the thick-walled packaging sector. Thanks to our new developments we can now serve and target this market segment, too, so it is also up to us to create new markets.
This means that the development of new market and customer-oriented technologies is thus anchored firmly in your growth strategy?
Together with its sister companies 3S, PURE LOOP and our subsidiary EREMA North America, EREMA has been pursuing a consistent and sustainable growth strategy for many years. This also has an impact on the turnover of the EREMA Group, with consolidated sales reaching around EUR 130 million in the 2014/15 financial year.
Please tell us a little about the role and the tasks of the different sister companies.
PURE LOOP GesmbH pursues the further development of the shredder-extruder technology and, as a new sister company, helps us to continue with our expansion strategy and clear market positioning. As a result we have considerably intensified the range of services we offer in the field of In-house Recycling. Speaking of growth, I should also mention the expansion of EREMA North America’s trial centre. Due to the high demand in the USA – especially in the post-consumer recycling sector – we have significantly expanded the trial centre at the company’s head office in Ipswich, Massachusetts, with four permanent recycling systems available for our customer’s trial runs. This will go into operation in late summer. We are on a course of expansion with 3S. The production area at the new location in Wartberg im Mürztal in Styria has been increased by 4,000 m2 to 7,000 m2 in total.
Let us turn to the subject of mechanical engineering. What is your claim in the competitive environment of PET recycling?
We have taken up a clear position here: compact, flexible, turnkey solutions with top plant stability and extremely low energy and other production costs with maximum decontamination performance. As a result, we offer our customers and the customers of our customers, i.e. the brand owners, maximum reliability with the end product – thanks to ultraclean material in accordance with FDA and efsa criteria.
What can you do in recycling as a mechanical engineering company to stay at the helm?
Competence, know-how and confidence in your own strengths are without doubt important instruments to stay at the helm. Additionally, you have to recognise market and customer requirements quickly to realise accomplished developments. You have to consistently put your products to the test and take care of them. We at EREMA also take a proactive approach to raising awareness and ensure that we are represented in the key interest groups around the world to promote positive developments concerning the utilisation of secondary raw materials. In addition to this we use industry events and conferences such as PETnology, for example. Its motto – “connecting comPETence” – i.e. networking and the link between human and machine, hits the nail on the head, as the saying goes.
Is cost pressure a good driving force for sustainable machine developments and business processes in recycling?
Good question. The answer here is yes and no. Why? YES, of course, because the whole system, i.e. the recycling loop, also has to be cost-effective in the end. NO, because there is a danger that possible trends and developments will be slowed down or even stopped as a result.
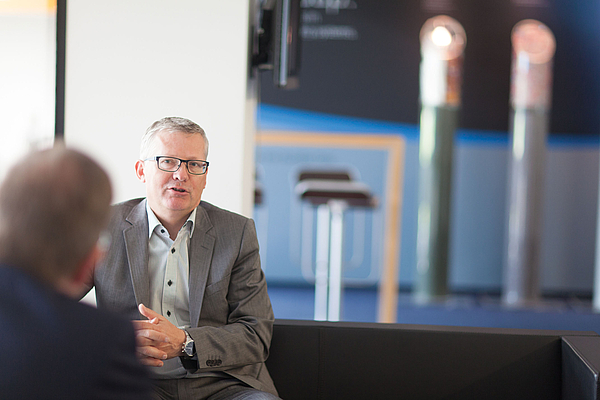
What is your opinion about the future of recycling?
May I elaborate a little on this? Even greater importance is going to be attached to plastics. The benefits of this multifunctional material in terms of technology and design will drive forward innovations in many product sectors. You can see this in lightweight automotive construction, for example, to reduce fuel consumption and CO2 emissions. Plastic consumption is currently growing at a rate of 8% every year worldwide, with around 7.2 billion people living on the planet earth. The global population is expected to be in the region of 8.4 billion in the year 2030 and this will impact on the demand for plastics. The growth in population, however, will not be distributed evenly across all continents. While Europe’s contribution to the global population will shrink from 18% to 8%, other regions of the planet will grow rapidly and disproportionately – and with them also the demand for raw materials. As, however, Europe has relatively low fossil energy resources, the shortage in these areas will exacerbate and lead to an increase in prices. This means that in future we will have to drastically reduce our dependence on fossil raw materials such as crude oil or natural gas and we will have to do so in two ways. First we will have to succeed in closing the loop of existing plastic streams by means of recycling. And secondly, because transport, heating and energy still currently account for 87% of crude oil consumption, we have to make more intensive use of the material benefits of plastics to obtain renewable energy and for lightweight engineering.
So the consequence of this is a lot of potential for plastics recycling?
Enormous potential is developing for plastics recycling, because plastics are becoming increasingly valuable as a secondary raw material. But to turn waste plastic into high-quality and accepted secondary raw material calls for intensive communication within the entire plastics industry – between raw material suppliers, plastics processors and recyclers. This is the basis for successful ecodesign. Only then is it possible to develop new products which take into account their later recyclability at the time they are produced. The way forward is quite clear to me: organising material flows better and optimising the production of plastics in such a way that new, high-quality products with a high recycling content can be made from them. This is how sustainability works in a closed loop.
It sounds logical. What hurdles do we have to overcome?
For the whole thing to work there is one critical factor: plastics recycling has to be clear to the plastics processors and the quality of the raw materials supplied has to be consistent, meaning raw materials or recycled pellets with precisely specified properties for the respective end application required. Another important point is reliable availability. Or to sum it up, the very same reliability which plastics processors are used to from virgin material.
How has recycling changed in recent years? What role does sustainability play?
In order to secure the necessary material streams also for future generations the recycled material share in products has to increase dramatically. In technical terms, quite a lot is already possible – the best example is the PET bottle. Besides the technical options it is also a question of acceptance. The crux of the matter lies in a paradoxical view of the consumers and the industry with regard to plastic: as far as the industry is concerned, plastic is a high-grade raw material. The consumer can have quite a different view, with plastic frequently being frowned upon. On the other hand, however, the general public demand sustainability through recycling. This in turn is opposed by the industry of plastics processors, with many of them still refusing to use recycled pellets – although everyone is talking about sustainable corporate policy at the same time.
Will the industry be able to keep the recycling ship on course on its own?
I think legislation is required here to create the necessary economic and awareness-building framework conditions. Passing laws and directives for the collection of plastic waste for reuse is not enough, you have to stipulate defined minimum percentages of recyclates in plastic products. This would enable us to kill two birds with one stone: a higher portion of recycled material in plastic products would not only have enormous positive leverage on the entire industry, it would also be a huge improvement in terms of image. But the longer this development takes, the more difficult it will be to maintain our material flows in a sustainable way. Pressing ahead with this development requires even more global manufacturers of branded products.
Have the pioneers been counting on or will they count on the right concepts?
Some global manufacturers of branded articles realised early on that they can start a positive spiral if they introduce products which contain recycled materials. The ideas put forward by Coca-Cola, Pepsi, Nestlé for PET and more recently by Henkel for polyolefins are all well and good but it would be more effective if even more global players pulled together.
What opportunities will PET recycling have to offer tomorrow?
You have to make a difference here between B2B and inline applications such as bottle to sheet. In the case of the latter, flexibility is becoming increasingly important so that sheets of varying thickness can be produced in line with market requirements. With B2B, on the other hand, decontamination is crucial, however in this segment the cost pressure has become much more intensive in recent years due to the virgin material price which represents a major challenge.
There are challenges in B2B. But isn’t it a bit like Formula1? Technically/technologically challenging – but seen critically: do we need it?
In Europe there are hardly any other ways of turning the PET material into products again. The fibre industry in Europe has more or less ceased to exist. In China the opposite is true: everything goes into fibre there and B2B recycling takes a back seat. Successful B2B recycling with the goal (in terms of properties and processing) of having no differences in quality to virgin material also makes the Europeans somewhat more independent from the material producers in Asia. B2B certainly has a right to exist.
If you compare PET recycling and polyolefins, where do you see advantages, disadvantages or trends?
With regard to PET, the end applications for rPET have already positioned well in the market. This applies to the products bottle, sheet, strapping and fibre. This is hardly the case at all in the PO sector. That means there is still work to be done. The same applies to collection and utilisation quotas.
What risks are there to PET recycling taking into consideration technical and commercial aspects? Were there mistakes in the past and do they still cause any problems today?
Existing and future virgin material capacities certainly put commercial pressure on B2B recycling. From a technical point of view, the recycling industry will continue to face new challenges as in the past. These have been solved so far, and this will also be the case in the future. With regard to the process chain I see the whole big problem at its beginning: the input of bottles which is not controlled in the medium term – and with it, the material quantities – brings instability to the whole recycling system. This is an important starting point in increasing effectiveness.
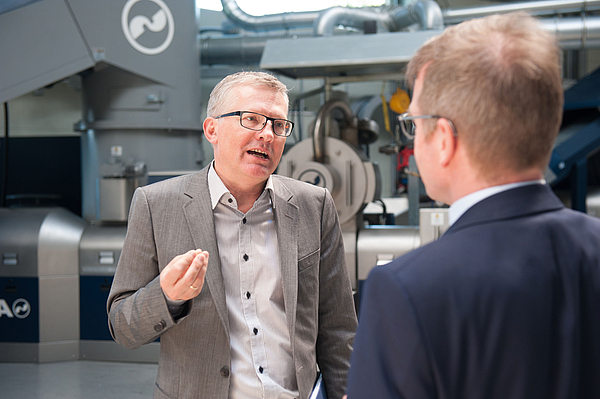
What are your short-, medium- and long-term forecasts for PET recycling – worldwide?
This is difficult to answer as it varies a great deal from region to region and above all from continent to continent. With regard to Europe: besides the various market trends there are also system-inherent trends which initiate the wide variety of framework conditions. Examples I can mention here include the United Kingdom, with PET sheets made from rPET, Germany has its own deposit system and Austria has voluntary commitment in the beverage industry. It is a fact that in the long term we will not be able to afford not to put all possible resources, i.e. “waste PET bottles”, into the recycling loop and reutilise them again in the EU. This means that there will still be growth in the long term, even if it is no longer as strong as it was in the past. The PET recycling sector is already well positioned in the EU. This can be seen not only in terms of quality, quality analyses and quality stability but also in the end markets which have developed. There is still potential to be tapped here, too. All in all, PET recycling does have a very sound position compared to PO recycling. What remains to be seen here, however, is the level of stability with regard to supply chain management as the input is not constantly secure in the medium term, barring exceptions of completely closed loop systems in individual countries.
Mr Hackl,
many thanks for the interview.
The comPETence center provides your organisation with a dynamic, cost effective way to promote your products and services.
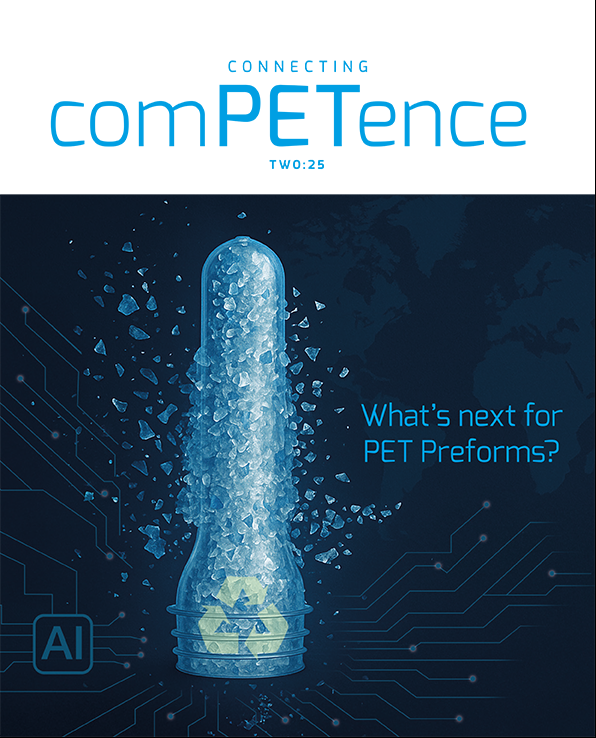
magazine
Find our premium articles, interviews, reports and more
in 3 issues in 2025.