
Sonnenuhrgasse 4
1060 Vienna
Austria
+43 1 59955-0
+43 1 59955-180
office@starlinger.com
www.recycling.starlinger.com
Starlinger recycling technology
Starlinger recycling technology is a division of Austrian-based Starlinger & Co GmbH and has been producing plastics recycling machines since 1987. We provide solutions for inhouse production scrap and post-consumer plastics. Typical input streams are PET bottles, HDPE bottles, LD and LLDPE film, polyester, PA or PP fibres and filaments as well as non-wovens, PP raffia bags, PP, HDPE or PET tapes, and injection moulding articles.
We are specialized in PET bottle-to-bottle recycling, recycling of post-consumer polyolefins including odour reduction, recycling of polyester fibres and non-wovens, and recycling of PP raffia.
Typical recycling solutions:
- PET bottle-to-bottle recycling lines (FDA, EFSA, brand owner approved)
- HDPE bottle-to-bottle and cap-to-cap recycling lines (FDA approved)
- Post-consumer polyolefin and PS recycling lines
- Odour reduction technology
- PET flake-to-fibre/filament, polyester fibre/filament recycling lines
- Recycling lines for woven PP raffia materials, including recoBATCH compounding lines
- Post-consumer big bag-to-big bag recycling
- Film recycling lines (blown-, cast-, biaxially oriented film)
- EPS, EPP, EPE recycling lines
- WEEE recycling lines
- Melt filters including screen changers with power-backflush for polyolefins, PET and polyester
- Candle/sleeve filters for polyester melt filtration
PET and polyester applications
Most important for PET and polyester recycling applications is the hazzle-free reuse of the repelletised material without negatively influencing the extrusion or injection moulding process and without compromising the quality of the end product.
The Starlinger recoSTAR product line offers the ideal solutions for PET and polyester recycling as the lines are equipped with optimal pre-drying of the PET flakes, special screw design for gentle processing of the melt, inline quality control, and optional downstream Solid State Polycondensation.
The recoSTAR PET series is designed for recycling of post-consumer PET bottle flakes after the washing process, as well as for in-house recycling of PET flakes from bottles, preforms, strapping bands and sheets. The end product is always melt-filtered, uniform granulate that can be used for a wide range of applications.
Food contact applications
To prove decontamination efficiency for national authorities and brand-owners, Starlinger recycling technology has performed several challenge tests.
The results demonstrated that the system has excellent cleansing efficiency so that it is possible to use up to 100 % rPET produced on Starlinger recycling machinery for packaging with direct food contact.
With the first Letter of Non-Objection issued by the US FDA back in 2005, various proofs for food contact safety such as approvals by the US (FDA Letter of Non-Objection), Canadian, Austrian and French authorities as well as ILSI and the German BfR have been received. In addition, the conformity to EFSA and brand owner approvals underlines the superior quality of rPET produced on Starlinger recycling lines.
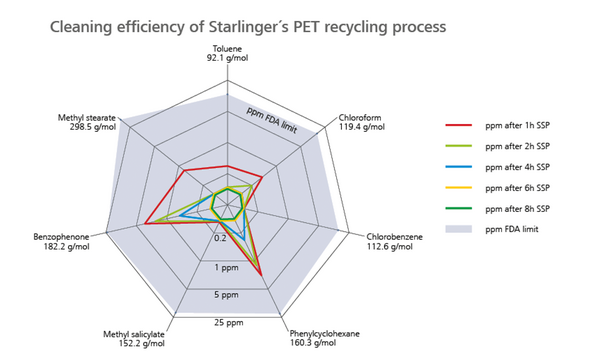
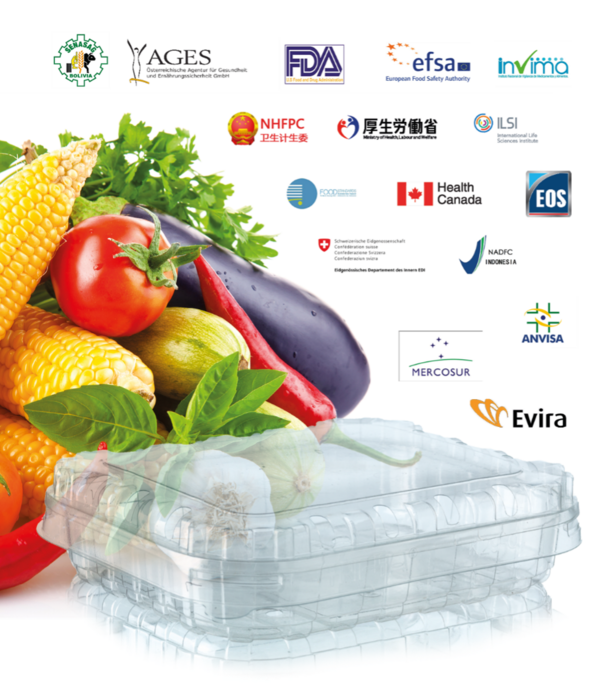
Overview of the available models of the recoSTAR PET series:
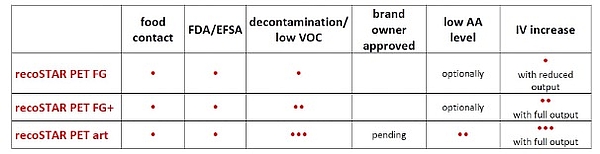
recoSTAR PET FG and FG+
PET flakes are heated and dried in a two-stage process, first with hot air, then by means of dry air or vacuum. The special design of the dryer outlets results in centre flow prevention, consistent residence time and FIFO processing. This ensures decontamination for food contact applications and ideal preparation for the extrusion process with IV increase. A choice of filtration and pelletising systems is available. Once installed, the unit can be equipped with an SSP reactor (iV+) to increase viscosity and decontamination levels.
recoSTAR FG and FG+ are cost-effective PET food-contact recycling systems with a compact footprint, minimal energy consumption and moderate IV increase.
The end product is melt filtrated, uniform granulate that can be used for a wide range of food-contact applications.
recoSTAR PET art
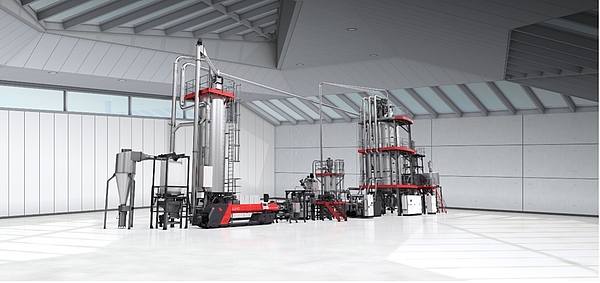
PET flakes are heated and dried in a single-stage process with hot desiccant air. The special design of the dryer outlets results in centre flow prevention, consistent residence time and FIFO processing, ensuring ideal preparation for the extrusion process. A choice of filtration and pelletising systems are available. The downstream inline vacuum SSP reactor uses the energy of the previous steps. Special FIFO design ensures consistent reaction parameters, adjustable IV increase as well as highly effective decontamination (ultra-low VOC, AA < 1 ppm) for food contact applications.
The Starlinger recoSTAR PET art produces rPET pellets of highest consistency (shape, flow behaviour, crystallinity, humidity, etc.) and highest purity (ultra-low levels of acetaldehyde, ethylene glycol and VOCs).
ADDITIONAL APPLICATIONS
PET film, polyester fibre recycling and hybrid solutions
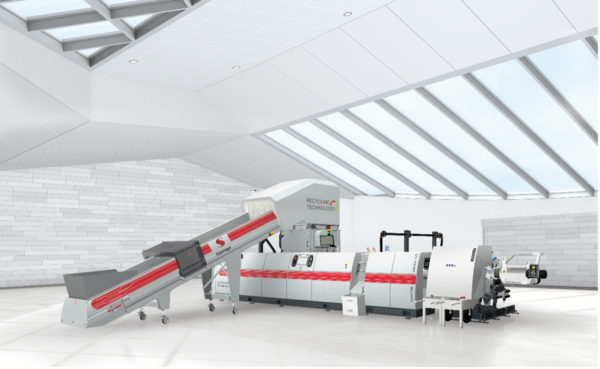
Starlinger offers additional machine platforms for BOPET film as well as fibre and filament recycling: recoSTAR dynamic and recoSTAR universal. Unlike the recoSTAR PET series they are usually not equipped with a flake dryer but with size reduction and feeding units to handle film and fibres or filament that are not free flowing. In some cases, these machines are additionally equipped with bottle flake dryers and side feeders attached directly to the extruder, transforming the machine into a hybrid solution for processing e.g. 100% bottle flake or 100% fibres, or a mixture of both. Depending on the physical form of the material to be processed and the desired rPET pellet quality, either recoSTAR dynamic or recoSTAR universal is the system of choice.
Inline recycling and PET sheet production – viscoSHEET
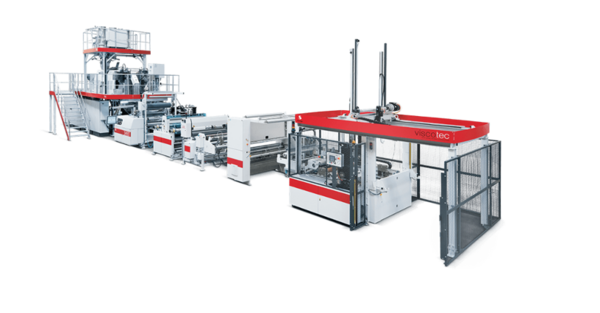
viscoSHEET PET sheet production lines combine recycling and production in one system. Processing washed PET bottle flakes, the line converts them into high-quality PET sheet that can be used for food packaging. In case of inline application, a vacuum SSP reactor (deCON, viscoSTAR) can be installed before the production extruder instead of a conventional dryer. In this step, post-consumer sheet flakes – or also a mixture of flakes from preforms and post-consumer bottles – are dried, decontaminated and the intrinsic viscosity (IV) is increased before being processed on the production line. The higher IV of the final sheet leads to better and faster processing of the material in thermoforming machines, resulting in less brittle cups or trays. viscoSHEET lines are highly automated, ensuring high efficiency in production and minimal production losses, short changeover times, flexibility and energy savings. The combination of recycling step and production step results in competitive investment costs and helps to reduce energy consumption and maintenance while remaining user-friendly.
PET strapping
PET flakes are also a valuable secondary resource for strapping bands, which can be made from up to 100 % recycled PET (rPET) when processed with the Starlinger iV+ technology.
PET has an important economic advantage: it can be “upcycled”. The quality of the recycled PET is often higher than before the recycling process. In order for rPET to achieve the high intrinsic viscosity (IV) required for strapping bands it undergoes a solid state polycondensation (SSP) process.
Results
Starlinger: Record Turnover in 2023/2024
Starlinger offices and agents