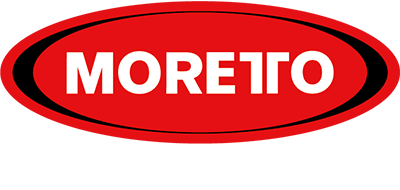
via dell'Artigianato, 3
35010 Massanzago (PD)
Italy
+39 049 9396711
info@moretto.com
www.moretto.com
ABOUT MORETTO
Established in 1980 in Massanzago (Padua), Moretto S.p.A. is a company based on the passion and dedication of Renato Moretto, founder and current President, able to anticipate the incredible application developments in the plastics’ world.
Moretto S.p.A. is an italian leading company in researching, developing, and producing automated systems for the plastics processing industry. With five production plants, operations in 9 countries and a committed dealer network, the company serves customers in over 70 countries.
Moretto provides comprehensive solutions for feeding and conveying, dosing and blending, drying, granulation, temperature control and cooling, and storage. The integration of MOWIS, a supervision and management software developed in-house, facilitates the seamless control and connection of all production processes.
Moretto serves diverse industries, including automotive, medical, optical, beverage, packaging, electronics, white goods, technical moulding, and recycling, notably making significant contributions to the PET sector, with a dedicated range of products.
Moretto excels in providing tailored solutions, employing an innovative approach (backed by 169 patents), and with a strong commitment to sustainability.
EUREKA PLUS
Eureka Plus is the Moretto’s innovative drying system designed to continuously reduce energy consumption and improve drying performance, particularly for PET, where energy efficiency makes the difference in profitability for processors.
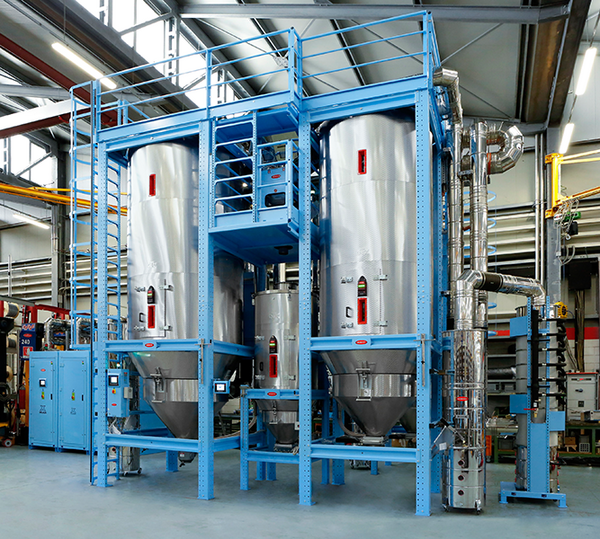
Eureka Plus is comprised of four Moretto patented technologies:
- X MAX, the unique modular multi-bed dryer with constant performance,
- FLOWMATIK, a dynamic airflow management system,
- OTX (Original Thermal eXchanger), drying hoppers with superior mass flow drying characteristics.
- MOISTURE METER, the in-line moisture analyser.
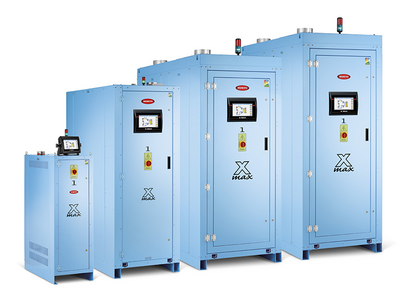
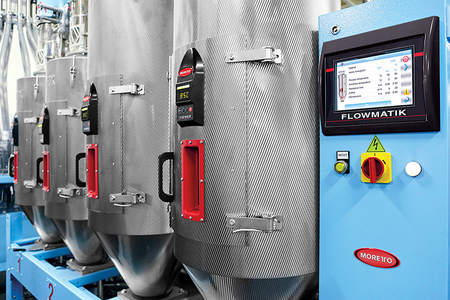

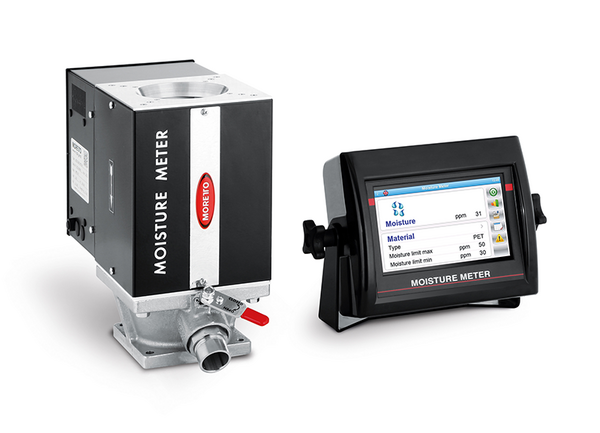
These four systems, working together, provide processors with a modular, self-adjusting, energy-saving dehumidification system.
X MAX is a modular dehumidifying drying system that incorporates 3 or more drying units to meet drying requirements and to provide redundancy for regeneration and maintenance. Additional units (up to 10 total) can be added as drying requirements increase. Each desiccant dryer uses exclusive zeolite desiccant to deliver consistent Dew Point to -85°F (-65°C) for uncompromising drying performance. No cooling water, nor compressed air are required. Included in the system is an independent heating unit for sequencing regeneration as needed to all dryer desiccants. Adaptive airflow from strong, turbocompressor blowers provide consistent airflow to compensate for off-line dryers receiving maintenance or in regeneration. The X MAX drying system includes an icon-navigated, full-color, touchscreen control.
Flowmatik is an automatic, adaptive airflow management system for multi-hopper drying systems that eliminates traditional valves and manual balancing of airflow in multiple hoppers. Flowmatik assures delivery of optimum airflow to each hopper, based on the given hopper size and user-inputted material and throughput requirements, assuring the lowest possible energy consumption since excess airflow is removed. Flowmatik eliminates the undesirable stress on resin from over-drying, even in reduced or stopped production circumstances, protecting the intrinsic viscosity of the resin. The icon-navigated, full-color, touchscreen control prompts users to simply input material and throughput requirements in lbs or kg per hour for each material hopper.
OTX (Original Thermal eXchanger) is an advanced drying hopper design that provides optimized mass flow of materials for highly predictable resin drying. With OTX hoppers, each plastic granule is uniformly exposed to drying air and achieves full residence time in the hopper even though the hopper size is smaller, resulting in space savings and energy reduction. Mechanical features include a durable SPYRO, corrugated ceramic fiber/stainless steel skin, large clean-out door with sight glass, hinged or removable top plate, screened filter air outlet, tramp metal magnet cluster on the material inlet and a counter-balanced, swing-down cone section on models 28 cu/ft (800 liter) and larger.
Each hopper is equipped with a Viewer control, conveniently located on the hopper’s access door, which provides a confirming readout of actual temperature in the hopper, and an indicator of operating status. The Viewer can also be used for local programming of the drying temperature at the hopper. Heating units are mounted directly to the hopper to minimize heat losses.
Lastly, the Eureka Plus system includes Moisture Meter, an inline, resin moisture sensing and drying control. The Moisture Meter uses Power Peek Technology to read the moisture content of the resin itself using electromagnetic waves, which change based on the moisture within the resin. A sensing unit below the drying hopper read the moisture levels of the resin to assure the success of the dehumidification process. Based on Moisture Meter signals, the drying process is dynamically altered, in rapid and direct response to moisture readings. Moisture Meter sensitivity ranges from 15 ppm (=/- 3 ppm) to 3,000 ppm and operates with resins being dried from 68 to 356 °F (20 to 180 °C).
Eureka Plus system effectively closes the loop on resin drying by in-line measurement of each granule’s moisture content and applying this data to the adaptive drying system. Ever responsive, the system essentially provides “drying on demand”, based on the real drying needs of the polymer at any given time. Managing drying functions in direct response to environmental variables that typically interrupt predictable polymer moisture levels, the Moretto drying system can guarantee production certification and maximum energy efficiency.
The Eureka Plus drying system can be supervised by MOWIS, the supervision and management system. MOWIS, totally integrated to the local network via OPC UA, enables connectivity between machines, departments, plants and facilities.
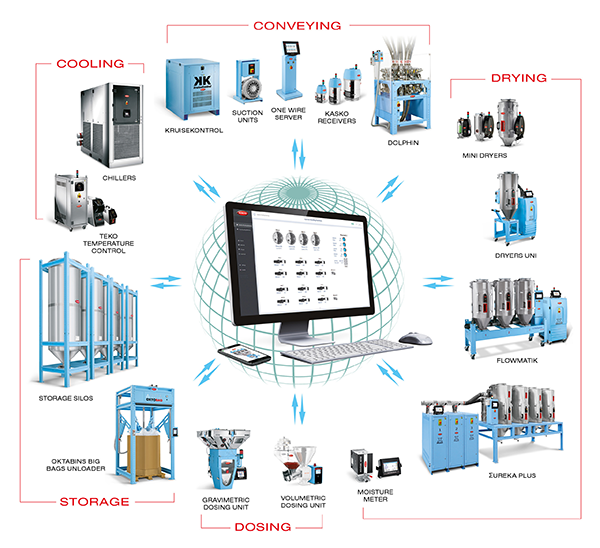
MPK crystallizer
One of the most important phases of the recycling process is the crystallization of amorphous material. MPK Crystallizer is a system designed to convert amorphous material like PET regrind to a crystallized state, ready for drying. Only perfectly treated r-PET can be used with virgin plastic polymers in other production processes.
The latest version of MPK greatly focuses on usability with a single touch screen control panel mounted on the dryer and designed to manage all the system functions.
Some of the original characteristics of the Crystallizer allow to eliminate the typical problems related to the processing of recycled polymers.
Ease of use and cleaning are fundamental features in machines that treat post-consumer material, especially to limit production change times and / or filter clogging.
The cone, openable with assisted device in only 2 minutes allows the operator to proceed rapidly with cleaning and maintenance activities. An exceptional usability factor to handle critical materials such as regrind and flakes.
The mixing chamber is equipped with removable blades that can be easily adapted to different material types. Thanks to their profile, the blades mix the regrind homogeneously avoiding any material clumps during the crystallization phase.
The patented schockproof stainless steel hopper coating - SPYRO - isolates the mixer body from external agents and contains heat dispersion, increasing its energy efficiency.
MPK is a next generation product, a solution designed for the smart factory. Equipped with an intuitive touch control graphic interface, this system can be connected to the other system automations via web and remotely controlled through MOWIS, the supervision software which completes connectivity via OPC UA, ETHERNET, MODBUS.
MPK is equipped with the Vortex filtration device, which intercepts dust up to 20 microns and greatly increases the autonomy of the filter inside the dryer body and the Purex condensate separator which captures and removes oily and/or resinous substances contained in the vapors after the process, impurities typically present in materials of post-consumer origin.
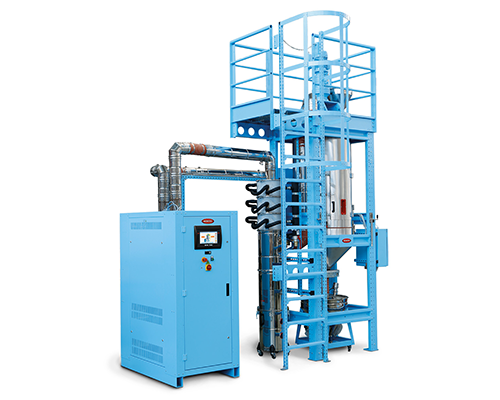
DS Series Mold Space dehumidifiers
Mold space dehumidification is a critical component in high volume production of PET and other hygroscopic plastic products, especially those with elevated processing temperatures. DS mold space dehumidifiers preserve molds from water condensation and maintain a dry atmosphere for the molding process, increasing the performance both in terms of final product quality and energy efficiency and enlarging the life cycle of the molds.
DS mold space dehumidifiers from Moretto are available in a range of 3 sizes to meet the size of the molding area to be dehumidified. The DS provides Dew Points from 23 up to 5°F (-5 to -15 °C) assuring the nuisance of mold sweat will be reduced. A honeycomb desiccant rotor is at the heart of the DS dehumidification system, continuously rotating and providing dry air while simultaneously purging itself of moist air. Since the DS dehumidifier works on an open loop with the molding area, it constantly monitors atmospheric conditions to deliver dry air, while operating with the lowest possible energy consumption. Two blowers provide the necessary airflow for mold space dehumidification and for the regeneration of the desiccant wheel honeycomb.
Equipped with an icon-navigated, touch view control panel, the DS is easy to operate and displays both the humidity and air temperature. A security system is included to prevent unauthorized changes.
Two-stage filtration and an air intake condenser prevent contamination of the desiccant while minimizing the need for filter cleaning on both the dry air delivery and the regeneration air circuits.
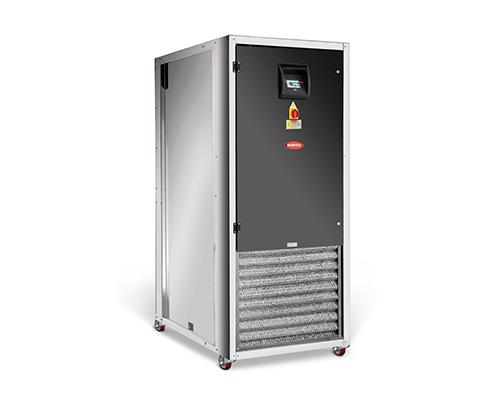