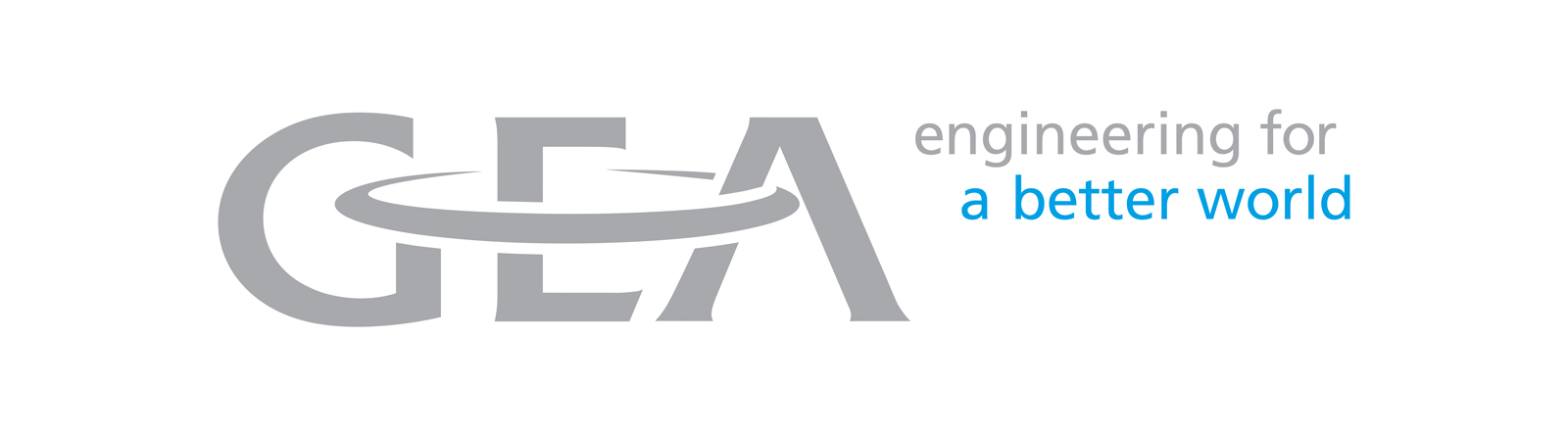
Via Fedolfi 29
43038 Sala Baganza (Parma)
Italy
+39 0521 839411
+39 0521 833879
www.gea.com
Profile

GEA Procomac S.p.A. designs, manufactures and supplies complete Aseptic and ESL filling lines for sensitive products, including juices, isotonic drinks, tea, milk and milk-based beverages with and without particulates, and traditional filling lines for water and CSD and fresh milk in plastic bottles.
GEA Procomac is recognized as the leading company in the sensitive beverages filling field with over 170 lines installed worldwide. The company offers state of the art bottle sterilization based on wet PAA technology, with ECOSpin 2 Zero for high speed and Modulbloc for low/medium speed lines, and on dry H2O2 technology with Whitebloc, recently designed specifically for the beverage and dairy industry; and the latest preform sterilization with ABF (Aseptic Blow Fill) technology - the world’s first rotary aseptic blow moulding machine with an integrated aseptic filler and capper.
GEA Procomac has developed the Aseptic Dual Filling system, comprising an Aseptic Piston Doser PX and a standard Aseptic filler for clear products, which represents the best hygienic solution worldwide for the filling of PET bottles with products containing fruit pieces of up to 10x10x10 mm.
Thanks to GEA Procomac’s R&D activities - essential to ensure its position as a technological leader - the company stands out in the packaging systems market through its ability to understand and fulfil the needs of different customers and provide tailor-made solutions.
Preventive Maintenance Program, Line Efficiency Consulting Service, Maintenance Kit, Upgrades and Retrofits, Customer Training and a new approach to Total Preventive Maintenance are part of the delivery program.
ABF (Aseptic Blow Fill) system
The ABF is the world’s first rotary aseptic blow moulding machine with an integrated aseptic filler and capper. Its principle is to sterilize the preform - not the formed bottle - with hydrogen peroxide at the exit from the oven, then blow the preforms with sterile air in a sterile environment and maintain this sterility throughout the filling and capping process. This process reduces the use of chemicals, requires no bottle rinsing, enables a simpler and smaller layout and reduces energy consumption.
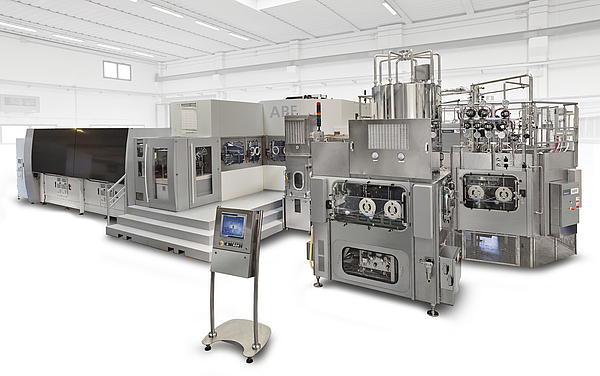
As the preform is made of thicker material than the bottle itself it’s possible to increase the temperature of the treatment without risk of shrinkage that would affect the shape of the bottle. This allows the weight of the bottle to be kept to an absolute minimum.
A key design feature of the ABF is the blowing of the preforms ‘upside down’. This enables all non-cleanable components to be located outside the sterile zone. All surfaces in the sterile zone are accessible and are very easy to clean.
The ABF is validated for both high acid and low acid products.
ABF system concept
- Sterilizing the preform instead of the bottle reduces the quantity of sterilizing agent used as the preform is smaller and has a simpler shape than the bottle itself.
- As the preform is made of thicker material than the bottle itself it’s possible to increase the temperature of the treatment without risk of shrinkage that would affect the shape of the bottle. This allows the weight of the bottle to be reduced compared with traditional aseptic systems.
- ABF provides flexibility, sustainability and space saving.
- ABF is an extremely flexible system that can blow and fill up to 48,000 bottles per hour and operate at different levels of decontamination appropriate for each product. This allows products with different shelf-life - low-acid aseptic beverages, high-acid aseptic beverages, ESL beverages, flavored water, etc. – to be produced on the same system.
- ABF can be used for ambient or cold-filling operations.
- The system uses almost no chemicals or water. Energy usage is kept to a minimum by the elimination of air conveyors, sterilization and rinsing carousels, water UHT sterilization, and steam.
- The whole system is more compact than traditional technology and requires fewer operators.
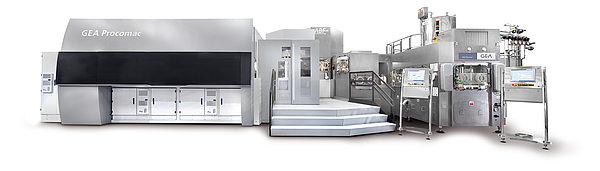
Lightweight aseptic PET bottle - A light touch in safe hands
ABF decontaminates the preforms with an H2O2 dry process: as the preform is made of a thicker material than the bottle itself, it’s possible to increase the temperature of the chemical agent with no risk of shrinkage. This allows the weight of the bottle to be kept to the very minimum.
This ability is illustrated with the introduction of a new 12g PET bottle, specifically designed by GEA Procomac for the aseptic filling market.
Sterilcap VHP R cap steriliser
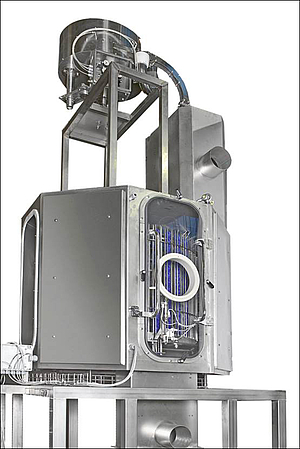
The perfect cap sterilization system for the GEA Procomac ABF is the Sterilcap VHP R: based on the dry sterilizing effect of H2O2 in vapor form at the correct concentration and temperature, it was developed to allow just one sterilizing agent to be used for the whole system. The newest feature of Sterilcap VHP R is the opportunity to sterilize both flat and sport caps on the same machine: changeover can be performed quickly, without any mechanical intervention and without losing sterility.
The design of the chutes inside the machine ensures that all the cap surfaces are exposed to prevent any shadowed area. Sterilcap VHP combines a reliable and effective treatment that achieves up to 6 Log reduction with gentle handling of the caps without removing the slipping agent and avoiding any deformation.
Sterilcap VHP features:
- Compact layout
- Sterilising area physically isolated
- Effective VHP treatment
- Uniform H2O2 concentration
- Gentle treatment and handling
- No slipping agent removal
- No water consumption
- Suitable for high speed lines
The 6th generation of PAA (Peracetic Acid) based sterilising solution
As well as ABF technology, GEA Procomac offers state of the art PAA bottle sterilization with Ecospin 2 Zero for high speed and Modulbloc for medium-low speed lines. The PAA technology developed by GEA Procomac uses only one sterilizing solution, based on Peracetic acid, to sterilize the environment and the packaging materials. Only five parameters have to be controlled to achieve a robust and reliable sterilization: pressure, temperature, concentration, flow rate and contact time.
Ecospin 2 Zero comprise a rotary sterilizer, filler and capper enclosed in a microbiological isolator and it is equipped with all the necessary process units to produce sterile water, Peracetic Acid solution, cleaning and the filtration of all fluids.
ECOSpin2 Zero features a reduced critical aseptic zone and meets the market demand for sustainability with zero peroxide emissions and the lowest ever PAA, water and energy consumption. These features make ECOSpin2 Zero the best choice from an operational and investment point of view when choosing wet PAA aseptic filling technology.
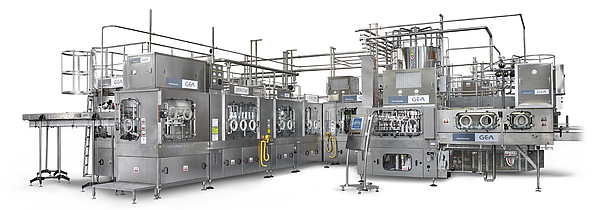
Modulbloc is the right choice even when limited space is available since it includes a sterilizer, a rinser, a filler and a capper carrousel all on a single base frame, and the ancillaries, aseptic process units and the cap sterilizing machine are located on top of the machine.
ECOSpin2 Zero and Modulbloc can be equipped with the complete range of filling valves designed and manufactured by GEA Procomac: from the FX range for any still products (clear, viscous and those with pulps, fibers and pieces with dimensions up to 6x6x6 mm) - up to the CX valve suitable for both still and carbonated drinks including clear products and those containing pulps and fibers. By installing a PX aseptic dosing machine on the in-feed carousel of the aseptic filler, it is possible to fill products containing pieces of fruit and cereals up to 10mm3.
ECOSpin2 Zero and Modulbloc are suitable for HA and LA beverages; they can reach a production speed from 6,500 up to 72,000 bottles per hour on 500 ml bottle, and allow a line availability of 165 hours without the need for intermediate SOP cycles during production.
Both ECOSpin 2 Zero and Modulbloc are FDA validated.
GEA Procomac supplies ABF technology to Amul Dairy in India
GEA Procomac is installing in these days its revolutionary ABF (Aseptic Blow-Fill) technology to Amul Dairy in India. GEA has already supplied Amul with its first aseptic filling line for PET bottles that improved productivity at the plant while changing forever the image of flavoured milk drinks, drinking yoghurt and milk shakes with young consumers in India. The new line will provide Amul with the ultimate in aseptic filling technology
The Amul Dairy in Gujarat is a leading producer that has become a model for the Indian dairy industry. Its products are marketed under the popular Amul Kool and Amul Lassi brands. Moreover the possibility of package in PET bottles pushed Amul to explore new flavors and products such as Amul Pro and Amul smoothies. PET bottles made milk drinks contemporary and glamorous allowing them to compete on equal terms with colas and other carbonated drinks on retail shelves. Generally the Amul sales are increased since the Amul product in PET bottles were introduced in the Indian market.
The new ABF technology from GEA builds on that principle by allowing even lighter-weight bottles to be used with more complex designs that are not distorted during the sterilization process.
The new ABF line is expected to be commissioned by summer 2015.
Liquid Dairy products bottling
Milk and milk based products are highly sensitive beverages that, depending on the requested shelf life, require container decontamination before filling. GEA Procomac portfolio comprises compete filling lines for pasteurized, ESL and UHT milk and milk based drinks.
If pasteurized milk distributed via cold chain can be filled with traditional filling technology and does not require any bottle treatment, container decontamination is an essential part of the Extended Shelf Life (ESL) process. ABF 4C is the ESL configuration of ABF technology, designed specifically for the ultraclean blow filling of liquid dairy products with a shelf life of up to 120 days in PET bottles. It is a rotary ultraclean blow moulding machine (Airstar 4C) with an integrated ultraclean filler and capper.
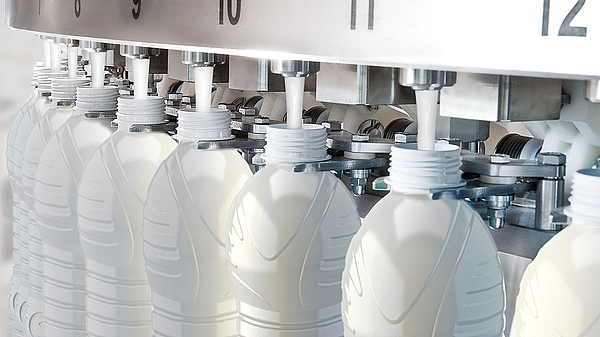
Special requirements must be addressed when sterilizing bottles for UHT milk or milk-based drinks. The GEA Procomac complete range of container sterilization technologies, both dry (ABF) and wet (ECOSpin 2 Zero and Modulbloc), is the solution that meets those requirements to obtain a shelf stable product.
In addition to these machines, GEA Procomac developed Whitebloc, a new technology concept specifically designed for the liquid dairy industry and ideal for HDPE and PET container handling. Whitebloc uses a completely dry technology and allows users to choose the right decontamination target for every kind of product, high or low acid, according to the specific shelf life required.
In both ESL and aseptic applications, the sterilization/decontamination treatment is performed by a system of nozzles that spray the containers with H2O2 solution, and a flow of hot sterile air which activates the H2O2 and then purges out any peroxide residuals.
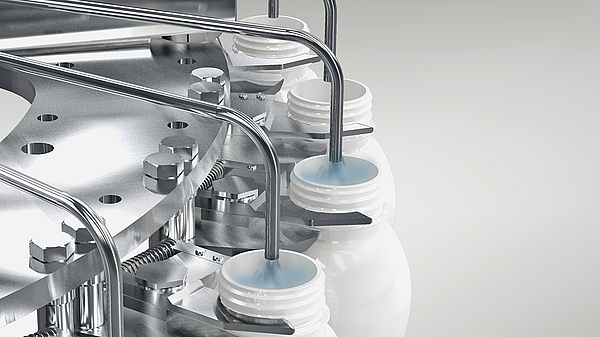
A physical isolation of the ultraclean environment (Clean Box) and an overpressure of 10 Pa of sterile air around the filler/capper zone, is the key to ESL technology. In aseptic configuration all the critical parameters are set to the highest level of hygiene thanks to a microbiological isolator which encloses the sensitive area, and a sterile overpressure air flow of 30 Pa which prevents bottles being recontaminated after the H2O2 treatment.
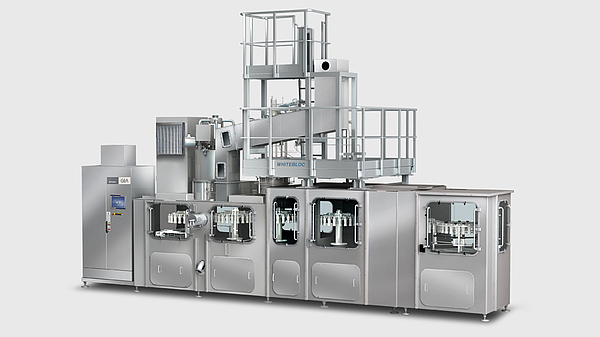
The new Sterilcap VHP L and the Sterilfoil VHP L have been specifically designed to be coupled with Whitebloc and are able to treat flat, sport caps and foils using dry H2O2.
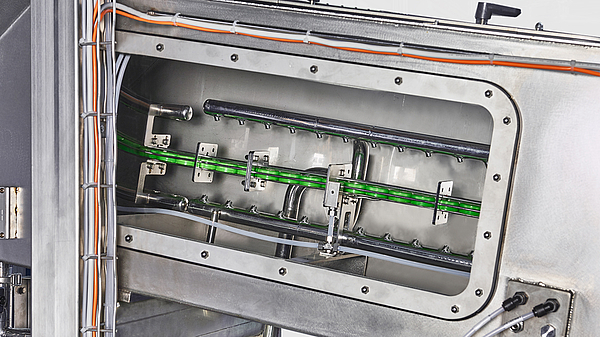
White & Safe bottle
UHT milk in PET is a rather new concept, as only some years ago it was not possible to ensure the proper light barrier to the UHT milk using PET. Thanks to new additives available on the market that can provide one, GEA Procomac created a new PET bottle specifically designed for ESL and UHT liquid dairy applications.
Designed in collaboration with P.E.T. Engineering and Novapet for the UHT dairy market, the GEA Procomac barriered PET bottle features ‘total light barrier’ (over 99.5% of the visible light spectrum), while guaranteeing over nine months shelf life and significant advantages over previous materials.
Barriered PET in addition to a flexible and modular light barrier functionality, offers the potential to allow lightweighting in exactly the sasme way as ordinary PET, and a significant reduction of material costs with the same recyclability potential as for normal PET.
The level of light protection provided by the bottle can be simply customized by adjusting the dosage (%) of concentrate (DCU® by Novapet) in the preform to match the needs of each individual product, with a level of control over operating costs that has not been possible to date. There is no need for dedicated technology for the injection process. With little investment the preforms can be produced by a high speed standard mono-layer injection machine at whatever DCU dosage (%) is required without any risk of delamination during blow molding process due to the single-layer technology.
“White & Safe” bottle weighs only 21 g for a 1,0 l size, features a 33/15 neck finish and its shape gives the bottle a good performance in terms of top load and resistance to the vacuum.
New trends: beverages with fruit pieces
GEA Procomac has developed the new Aseptic Dual Filling System for the bottling of still beverages that contain pulps, fibres, and pieces of fruit or cereals with dimensions of up to10 x 10 x 10 mm. This is believed to be the first time this process has been used in a cold-fill environment for PET bottles. The Piston Doser PX achieves the aseptic dosing of the valuable solid pieces ahead of the subsequent liquid filling process, with a high level of accuracy.
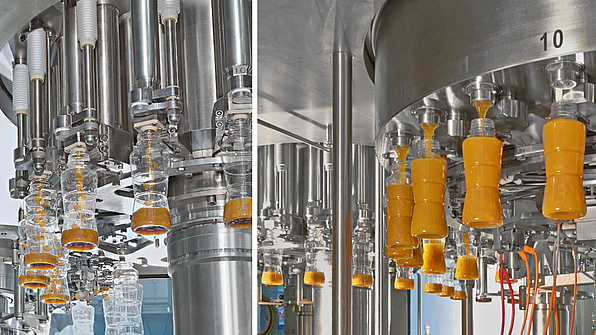
The Piston Doser PX is simple but effective. A cam-driven piston first draws into a cylinder the prescribed volume of solid particles, before injecting it into the awaiting PET bottle. The bottle then moves onto a standard volumetric, electronic filler to add the liquid juice and complete the aseptic filling process. The dual fill system requires a two-stream process line: one dedicated to the thermal treatment of the pieces and the other to the thermal treatment of the clear liquid.
Aseptic filling, in a book
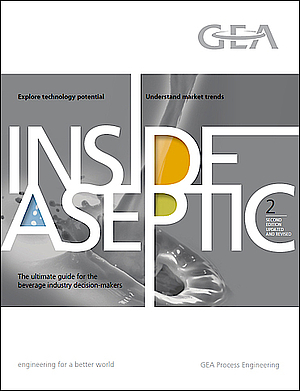
The second edition of GEA Procomac’s book, Inside Aseptic was launched during drinktec 2013 in Munich. The publication was eagerly awaited by the company’s customers, students, and industry professionals as it provides a unique insight into the world of aseptic bottling and describes both current technology and speculates on what the future might hold in store for this relatively young industry.
Aseptic bottling has been an accepted technique for around 20 years and so the technology is rapidly developing as new opportunities arise. Inside Aseptic has become recognized as an authoritative publication that rises above commercial promotion to provide readers with information, knowledge and inspiration to help them understand the processes involved and the opportunities for aseptic processing within their own field of operation.
Subjects tackled include aseptic blow filling, the future of sustainability, filling trends, cap sealing techniques, plant productivity improvement through Total Productive Maintenance, FDA insights and electronic validation.
No contact data available